Method and device for blast furnace to blow coal powder
A pulverized coal and blast furnace technology, applied in blast furnaces, blast furnace details, furnaces, etc., can solve the problems of large heat dissipation, large heat loss, and shortened service life of straight blowing pipes, and achieve enhanced heat and mass transfer, increased residence time, and service life long effect
- Summary
- Abstract
- Description
- Claims
- Application Information
AI Technical Summary
Problems solved by technology
Method used
Image
Examples
Embodiment Construction
[0031] Such as figure 1 As shown, a method for blowing pulverized coal into a blast furnace is: on the straight blowing pipe 3 of each tuyere 1, insert each short spray gun 4 into each mounting seat 5, and the coal powder injected into the blast furnace is from each mounting seat 5 The injection inlet 6 that is opened on the side enters, and then arrives in each short spray gun 4 through the coal injection hole 7 that is opened on the short spray gun 4 pipe wall facing the injection inlet 6, and then the pulverized coal is sprayed by each short spray gun 4 It is sprayed into the hot air, and finally enters the blast furnace through the tuyere 1 together with the hot air.
[0032] Such as figure 1 and image 3 As shown, a blast furnace pulverized coal injection device is at least composed of a straight blow pipe 3, a short spray gun 4, a mounting seat 5, a ball valve 9, a locking device 10, a coal delivery branch pipe 11, a distributor 12, a small ball valve 14, a coal delive...
PUM
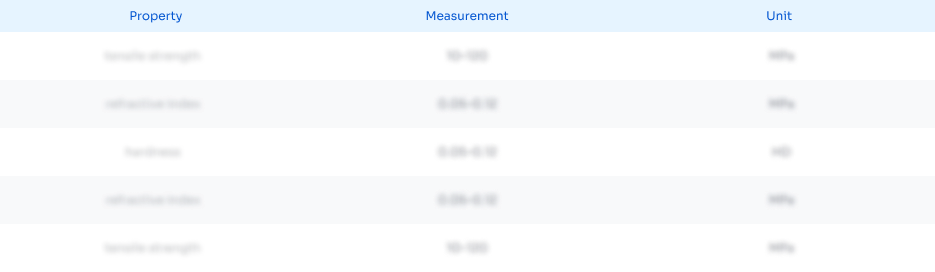
Abstract
Description
Claims
Application Information

- R&D
- Intellectual Property
- Life Sciences
- Materials
- Tech Scout
- Unparalleled Data Quality
- Higher Quality Content
- 60% Fewer Hallucinations
Browse by: Latest US Patents, China's latest patents, Technical Efficacy Thesaurus, Application Domain, Technology Topic, Popular Technical Reports.
© 2025 PatSnap. All rights reserved.Legal|Privacy policy|Modern Slavery Act Transparency Statement|Sitemap|About US| Contact US: help@patsnap.com