Method for extracting aluminum oxide
A technology for aluminum oxide and aluminum hydroxide, applied in the field of aluminum oxide extraction, can solve the problems of difficult temperature control and stability in the sintering process, harsh equipment requirements, complex iron removal process, etc. The effect of using
- Summary
- Abstract
- Description
- Claims
- Application Information
AI Technical Summary
Problems solved by technology
Method used
Image
Examples
Embodiment 1
[0030] Heat ammonium sulfate to 250°C, decompose for 2 hours to generate ammonium bisulfate, and ammonium bisulfate is made into a solution with a concentration of 70% by mass; at the same time, the generated ammonia gas is recovered with water to prepare ammonia water. Grind the fly ash containing 45% alumina and 43% silica to 325 mesh, and mix according to the molar ratio of alumina / ammonium bisulfate in the fly ash as 1:20. Under stirring conditions, raise the temperature of the mixture of fly ash and ammonium bisulfate solution to 180°C, react for 300 minutes, cool the mixture to 95°C and filter to obtain a solution containing ammonium aluminum sulfate, silicon slag, and alumina in fly ash The reaction rate of converting to aluminum ammonium sulfate was 88%. Aluminum ammonium sulfate solution cools down to precipitate crystals, and after purification, it is made into aluminum ammonium sulfate solution, which reacts with ammonia water to form aluminum hydroxide. Aluminum h...
Embodiment 2
[0032] Heat ammonium sulfate to 500°C, decompose for 15 minutes to generate ammonium bisulfate, and make ammonium bisulfate into a solution with a concentration of 10% by mass; at the same time, recover the generated ammonia gas with water to prepare ammonia water. Grind the fly ash containing 42% alumina and 51% silica to 400 mesh, and mix according to the molar ratio of alumina / ammonium bisulfate in the fly ash to 1:3. Under stirring conditions, raise the temperature of the mixture of fly ash and ammonium bisulfate solution to 400°C, react for 10 minutes, cool the mixture to 100°C and filter to obtain a solution containing ammonium aluminum sulfate, silicon slag, and alumina in fly ash The reaction rate of converting to aluminum ammonium sulfate was 61%. Aluminum ammonium sulfate solution cools down to precipitate crystals, and after purification, it is made into aluminum ammonium sulfate solution, which reacts with ammonia water to form aluminum hydroxide. Aluminum hydroxi...
Embodiment 3
[0034] Heat ammonium sulfate to 265°C, decompose for 1.5 hours to generate ammonium bisulfate, and ammonium bisulfate is made into a solution with a concentration of 98% by mass; at the same time, the generated ammonia gas is recovered with water to prepare ammonia water. Grind coal gangue containing 43% alumina and 46% silica to 400 mesh, and mix according to the molar ratio of alumina / ammonium bisulfate in fly ash to 1:7. Under stirring conditions, raise the temperature of the mixture of fly ash and ammonium bisulfate solution to 50°C, react for 45 minutes, cool the mixture to 92°C and filter to obtain a solution containing ammonium aluminum sulfate and silicon slag, alumina in fly ash The reaction rate of converting to aluminum ammonium sulfate was 83%. Aluminum ammonium sulfate solution cools down to precipitate crystals, and after purification, it is made into aluminum ammonium sulfate solution, which reacts with ammonia water to form aluminum hydroxide. Aluminum hydroxi...
PUM
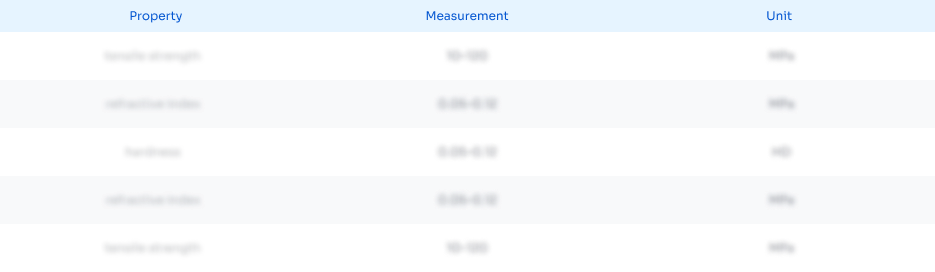
Abstract
Description
Claims
Application Information

- R&D
- Intellectual Property
- Life Sciences
- Materials
- Tech Scout
- Unparalleled Data Quality
- Higher Quality Content
- 60% Fewer Hallucinations
Browse by: Latest US Patents, China's latest patents, Technical Efficacy Thesaurus, Application Domain, Technology Topic, Popular Technical Reports.
© 2025 PatSnap. All rights reserved.Legal|Privacy policy|Modern Slavery Act Transparency Statement|Sitemap|About US| Contact US: help@patsnap.com