Rubber composite material for laser engraving
A laser engraving and composite material technology, which is applied in the processing and manufacturing industry of rubber products, can solve the problems of large release and performance degradation of rubber materials
- Summary
- Abstract
- Description
- Claims
- Application Information
AI Technical Summary
Problems solved by technology
Method used
Image
Examples
Embodiment 1
[0024] At room temperature, wrap 100 parts of natural rubber on double rollers on a rubber mixing machine, then add 5 parts of zinc oxide and 2 parts of stearic acid in sequence, and mix for 0.5 minutes; then add 0.5 part of antioxidant RD, add antioxidant 4010NA to 0.5 Part, mix for 2 minutes; then add 0.01 part of VN3 white carbon black, 1 part of N220 carbon black and 0.5 part of Si69 in batches, then mix for 5 minutes, then add 0.01 part of chlorinated paraffin and 1 part of red phosphorus, mix Refining for 0.5 minutes, and finally adding 1.5 parts of accelerator CZ and 3 parts of sulfur in the open mill, thin pass 5 times to eject the sheet, then park for 4 hours, then return to refining for 5 minutes and vulcanize to form a composite material.
[0025] The accelerator CZ is N-cyclohexyl-2-benzothiazole sulfenamide; Si69 is bis(triethoxysilylpropyl) tetrasulfide; the antioxidant RD is 2,2,4-trimethyl -1,2-Dihydroquinoline polymer (belonging to ketone-amine reaction product t...
Embodiment 2
[0027] At room temperature, wrap 100 parts of natural rubber on double rollers on a rubber mixing machine, then add 5 parts of zinc oxide and 2 parts of stearic acid in sequence, and mix for 0.5 minutes; then add 4 parts of antioxidant RD, add antioxidant 4010NA to 5 1 part and 1 part of protective wax, mixed for 5 minutes; then add 10 parts of VN3 white carbon black, 10 parts of N234 carbon black and 4 parts of Si69 in batches, then add 10 parts of brominated epoxy resin, 10 parts of alumina and 5 parts of red phosphorus, then mixed for 10 minutes, and finally add 1.5 parts of accelerator CZ, 0.2 parts of accelerator TT and 3 parts of sulfur in the open mill, thin pass 5 times, and then stop for 4 hours, then re-mix 5 minutes and vulcanization molding to obtain composite material.
[0028] The accelerator TT is tetramethylthiuram disulfide; the protective wax is a kind of anti-aging agent, which can prevent ozone aging and prolong the service life; the brominated epoxy resin bel...
Embodiment 3
[0030] At room temperature, wrap 100 parts of natural rubber on double rollers on a rubber mixing machine, then add 4 parts of zinc oxide and 1 part of stearic acid in sequence and mix for 0.5 minutes; then add 4 parts of antioxidant MB, and add antioxidant 445 to 5 Parts and 4 parts of protective wax, mix for 5 minutes; then add 50 parts of T383 white carbon black, 0.5 parts of N234 carbon black and 4 parts of Si75 in batches, then mix for 10 minutes, then add 20 parts of hydrotalcite and 0.2 parts Add 5 parts of paraffin oil and mix for 10 minutes. Finally, add 1.5 parts of accelerator DM, 3 parts of accelerator DTDM and 2 parts of sulfur in the open mill, and pass 5 times. The film is discharged, then parked for 4 hours, then re-melted for 5 minutes and vulcanized to form a composite material.
[0031] The accelerator DM is 2,2'-dithiodibenzothiazole; the accelerator DTDM is 4,4'-dithiodimorpholine; Si75 is bis(triethoxysilylpropyl) disulfide Antiaging agent MB is 2-mercaptob...
PUM
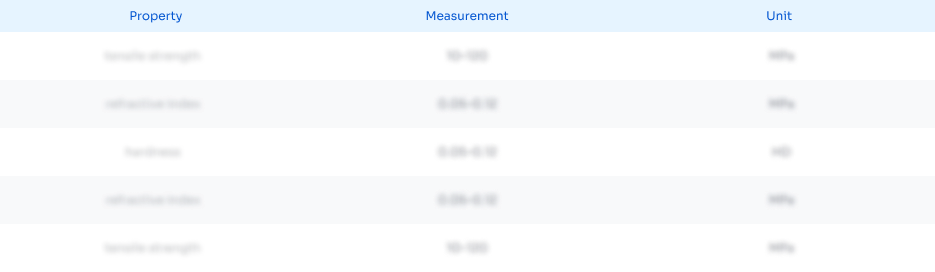
Abstract
Description
Claims
Application Information

- R&D Engineer
- R&D Manager
- IP Professional
- Industry Leading Data Capabilities
- Powerful AI technology
- Patent DNA Extraction
Browse by: Latest US Patents, China's latest patents, Technical Efficacy Thesaurus, Application Domain, Technology Topic, Popular Technical Reports.
© 2024 PatSnap. All rights reserved.Legal|Privacy policy|Modern Slavery Act Transparency Statement|Sitemap|About US| Contact US: help@patsnap.com