Preparation method of N-phenyl maleimide heat-resistant modifier
A technology of maleimide and heat-resistant modifier, applied in the field of preparation, can solve the problems such as the inability to effectively control the molecular weight and molecular weight distribution of the polymer, and achieve a mild and easy control of the reaction process, simple process and convenient control. Effect
- Summary
- Abstract
- Description
- Claims
- Application Information
AI Technical Summary
Problems solved by technology
Method used
Image
Examples
Embodiment 1
[0022] In a polymerization bottle with a reflux and stirring device, add 1.1mol styrene, 0.5mol maleic anhydride, 0.001mol azobisisobutyronitrile, 0.001mol dimethyl trithiocarbonate, 0.001mol 2-methyl-di Thiobenzimidazole benzyl ester and 1L cyclohexanone were reacted at 70°C for 5 hours under nitrogen protection, cooled to 60°C, added 0.45mol aniline, 0.009mol acetic anhydride and 0.001mol sodium acetate, and heated to 130°C for reaction 5 Hours, cool down to room temperature, pour the reactant into ethanol to precipitate the polymer, and then filter and dry to obtain the finished product.
[0023] The number-average molecular weight of the polymer obtained in this embodiment is 25×10 4 , the molecular weight distribution is 1.23.
Embodiment 2
[0025] In a polymerization bottle with a reflux and stirring device, add 1.1mol styrene, 0.6mol maleic anhydride, 0.001mol azobisisobutyronitrile, 0.003mol dimethyl trithiocarbonate, 0.003mol 2-methyl-di Thiobenzimidazole benzyl ester and 1L cyclohexanone were reacted at 75°C for 3 hours under the protection of nitrogen, cooled to 60°C, added 0.54mol aniline, 0.018mol acetic anhydride and 0.002mol sodium acetate, and heated to 140°C for reaction 4 Hours, cool down to room temperature, pour the reactant into ethanol to precipitate the polymer, and then filter and dry to obtain the finished product.
[0026] The number-average molecular weight of the polymer obtained in this embodiment is 21×10 4 , the molecular weight distribution is 1.18.
Embodiment 3
[0028] In a polymerization bottle with a reflux and stirring device, add 1.2mol styrene, 0.6mol maleic anhydride, 0.005mol azobisisobutyronitrile, 0.003mol dimethyl trithiocarbonate, 0.003mol 2-methyl-di Thiobenzimidazole benzyl ester and 1L cyclohexanone were reacted at 80°C for 3 hours under nitrogen protection, cooled to 60°C, added 0.54mol aniline, 0.027mol acetic anhydride and 0.003mol sodium acetate, and heated to 140°C for reaction 4 Hours, cool down to room temperature, pour the reactant into ethanol to precipitate the polymer, and then filter and dry to obtain the finished product.
[0029] The number-average molecular weight of the polymer obtained in this embodiment is 18×10 4 , the molecular weight distribution is 1.15.
PUM
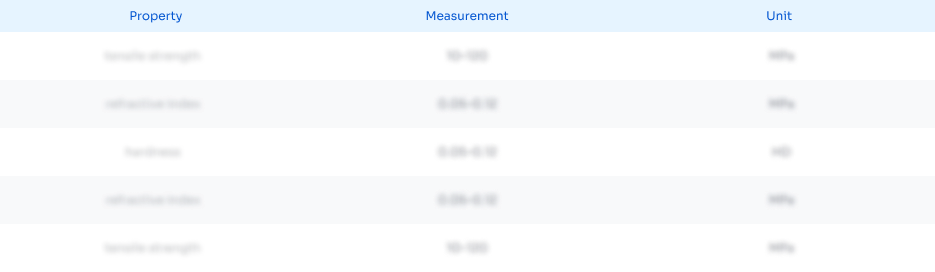
Abstract
Description
Claims
Application Information

- R&D Engineer
- R&D Manager
- IP Professional
- Industry Leading Data Capabilities
- Powerful AI technology
- Patent DNA Extraction
Browse by: Latest US Patents, China's latest patents, Technical Efficacy Thesaurus, Application Domain, Technology Topic, Popular Technical Reports.
© 2024 PatSnap. All rights reserved.Legal|Privacy policy|Modern Slavery Act Transparency Statement|Sitemap|About US| Contact US: help@patsnap.com