Polyglycerol fatty acid ester plasticizer and preparation method thereof
A technology of fatty acid ester and plasticizer, which is applied in the field of plastic industry auxiliaries and polyglycerol fatty acid ester plasticizer to achieve the effect of facilitating industrial production, improving adaptability and high biodegradability
- Summary
- Abstract
- Description
- Claims
- Application Information
AI Technical Summary
Problems solved by technology
Method used
Image
Examples
Embodiment 1
[0021] Add 340Kg of measured diglycerin and 650Kg of hydrogenated coconut oil into the reaction kettle, add 0.8Kg of sodium hydroxide, heat to 180-185°C, and carry out transesterification reaction under vacuum (-0.09 to -0.1MPa), the reaction time For 2 hours, when the monoester content is greater than 45% by gas chromatography, cool down to 80-100°C and add 1.3Kg of phosphoric acid for neutralization and filtration, followed by four-stage molecular distillation. The four-stage distillation process parameters are as follows: the first stage vacuum 500 -600Pa, temperature 135-145°C, second stage vacuum 100-200Pa, temperature 150-160°C, third stage vacuum 30-50Pa, temperature 150-160°C, fourth stage vacuum 0-10Pa, temperature 150-160°C . Remove moisture, unreacted polyglycerol, fatty acid and polyester to make the polyglycerol monoester content greater than 80%. Then put 500Kg of refined polyglycerol monoester and 460Kg of acetic anhydride into the reactor, add 40Kg of acetic a...
Embodiment 2
[0023] Add 310Kg of triglycerin and 600Kg of hydrogenated castor oil into the reaction kettle, add 0.6Kg of potassium hydroxide, heat to 220-230°C, and carry out transesterification reaction under the protection of nitrogen. The reaction time is 2.5 hours, and it is detected by gas chromatography. When the monoester content is greater than 45%, lower the temperature to 90-110°C and add 1.0Kg of phosphoric acid for neutralization and filtration, followed by four-stage molecular distillation. ℃, the second vacuum is 200-300Pa, the temperature is 150-160℃, the third vacuum is 30-50Pa, the temperature is 160-170℃, the fourth vacuum is 20-30Pa, the temperature is 160-180℃. Remove moisture, unreacted glycerin, fatty acid and polyester, so that the content of polyglycerol monoester is greater than 80%. Then put 500Kg of refined polyglycerol monoester and 510Kg of acetic anhydride into the reactor, add 50Kg of acetic acid and 0.5Kg of p-toluenesulfonic acid, heat to 115°C-135°C for ac...
Embodiment 3
[0025] Add 450Kg of diglycerin and 540Kg of lauric acid into the reaction kettle, add 1.5Kg of sodium hydroxide, heat to 180-190°C, carry out esterification reaction under vacuum (-0.09 to -0.1MPa), and the reaction time is 5 -6 hours, after measuring that the acid value is less than 2.0mgKOH / g, cool down to 80-100°C and add 2.5Kg of phosphoric acid for neutralization and filtration, followed by four-stage molecular distillation. The four-stage distillation process parameters are as follows: the first stage vacuum 700 -800Pa, temperature 145-150°C, second stage vacuum 200-300Pa, temperature 160-170°C, third stage vacuum 50-60Pa, temperature 160-170°C, fourth stage vacuum 20-30Pa, temperature 170-180°C . Remove moisture, unreacted glycerin, fatty acid and polyester, so that the content of polyglycerol monolaurate is greater than 80%. Then put 500Kg of refined polyglycerol monolaurate and 450Kg of acetic anhydride into the reactor, add 40Kg of acetic acid and 0.3Kg of p-toluene...
PUM
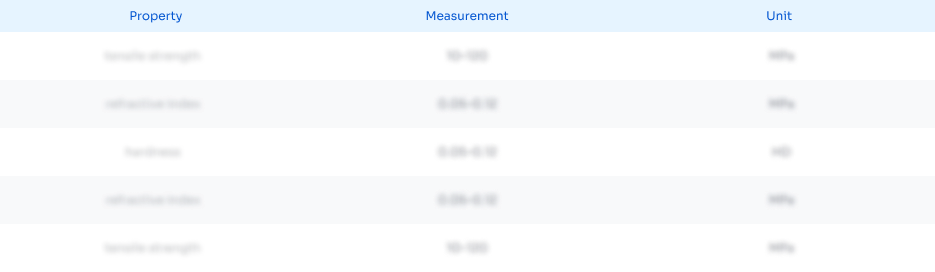
Abstract
Description
Claims
Application Information

- R&D
- Intellectual Property
- Life Sciences
- Materials
- Tech Scout
- Unparalleled Data Quality
- Higher Quality Content
- 60% Fewer Hallucinations
Browse by: Latest US Patents, China's latest patents, Technical Efficacy Thesaurus, Application Domain, Technology Topic, Popular Technical Reports.
© 2025 PatSnap. All rights reserved.Legal|Privacy policy|Modern Slavery Act Transparency Statement|Sitemap|About US| Contact US: help@patsnap.com