Method for producing hydrogen by light hydrocarbon primary steam reforming with heat exchange pre-reforming
A pre-reforming, steam technology, applied in chemical instruments and methods, hydrogen, inorganic chemistry, etc., to reduce exhaust emissions and save hydrogen production costs
- Summary
- Abstract
- Description
- Claims
- Application Information
AI Technical Summary
Problems solved by technology
Method used
Image
Examples
Embodiment 1
[0028] A first-stage steam reforming method for hydrogen production of light hydrocarbons with heat exchange and pre-reformation, comprising light hydrocarbons as raw materials, steam as oxidizing medium for light hydrocarbon conversion, heat-exchange pre-reforming furnaces, and first-stage steam reforming furnaces, among which the first-stage steam reforming furnaces Including convection section and radiation section, it is characterized by the following steps:
[0029] (1) Light hydrocarbons and steam enter the convection section of the first steam reformer for preheating, and the preheating temperature is 500-650℃;
[0030] (2) The preheated mixed gas A enters the heat-exchange pre-reforming furnace for pre-reforming reaction to obtain gas B. The pre-conversion rate of total hydrocarbon carbon is 10-50%;
[0031] (3) Gas B enters the radiant section of the first steam reformer for deep conversion reaction, and gas C is obtained. The conversion temperature at the outlet of the rad...
Embodiment 2
[0037] The hydrogen production method of natural gas first-stage steam reforming with heat exchange and pre-reformation includes the following steps:
[0038] The natural gas and steam are preheated to 530℃ in the convection section of the first steam reformer.
[0039] The preheated raw material mixed gas A (natural gas + steam) enters the heat exchange pre-reforming furnace, and the pre-reforming reaction is carried out under the action of the reforming catalyst. The pre-conversion rate of total hydrocarbon carbon in the imported raw materials is about 18%.
[0040] The heat exchange pre-reforming furnace is a vertical shell-and-tube type, with a reforming catalyst inside the tube to pre-reform the preheated raw material mixture A (light hydrocarbons + steam); a section of the steam reformer exits the high-temperature section of the tube outside the tube Gas is responsible for providing heat for the pre-conversion reaction in the tube.
[0041] The pre-reformed gas B at the o...
Embodiment 3
[0046] The hydrogen production method with heat exchange and pre-reformation of refinery dry gas first-stage steam reforming method includes the following steps:
[0047] Steam and desulfurized refinery dry gas are preheated to 530°C in the convection section of a steam reformer.
[0048] The preheated raw material mixed gas A (dry gas from the refinery + steam) enters the heat exchange pre-reformer and undergoes a pre-reformation reaction under the action of the reforming catalyst. The pre-conversion rate of total hydrocarbon carbon in the imported feedstock is about 24% .
[0049] The heat exchange pre-reforming furnace is a series of casing pipes, with reforming catalyst in the tube, pre-reforming the pre-heated raw material mixture A (dry gas from the refinery + steam); inside the casing jacket is a section of the steam reforming furnace outlet The high-temperature one-stage reforming gas is responsible for providing heat for the pre-reforming reaction in the tube.
[0050] ...
PUM
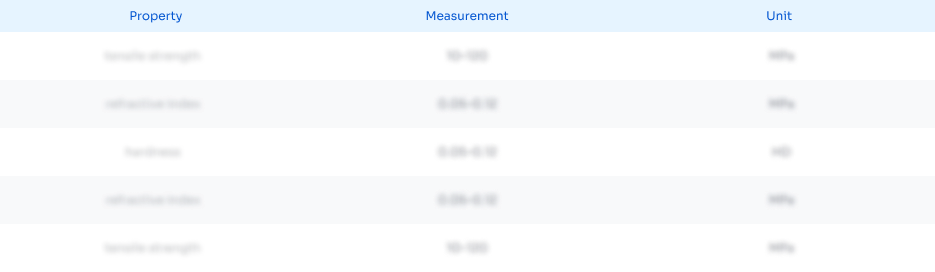
Abstract
Description
Claims
Application Information

- R&D
- Intellectual Property
- Life Sciences
- Materials
- Tech Scout
- Unparalleled Data Quality
- Higher Quality Content
- 60% Fewer Hallucinations
Browse by: Latest US Patents, China's latest patents, Technical Efficacy Thesaurus, Application Domain, Technology Topic, Popular Technical Reports.
© 2025 PatSnap. All rights reserved.Legal|Privacy policy|Modern Slavery Act Transparency Statement|Sitemap|About US| Contact US: help@patsnap.com