Method of preparing adipic acid by directly oxidizing cyclohexane
A technology of cyclohexane and adipic acid, applied in the field of direct oxidation of cyclohexane to adipic acid, which can solve the problems of low conversion rate of cyclohexane and low yield of adipic acid
- Summary
- Abstract
- Description
- Claims
- Application Information
AI Technical Summary
Problems solved by technology
Method used
Examples
Embodiment 1
[0017] 5mol acetic acid, 0.025mol NHPI, 0.025mol NAPI, 0.0025mol cobalt acetate, 0.0025mol manganese acetate, 0.005mol PEG2000 and 1mol cyclohexane (that is, the molar ratio of solvent, free radical catalyst, metal catalyst, cocatalyst, cyclohexane 5:0.05:0.005:0.005:1) into a 1-liter high-pressure reactor (with a reflux condensing device, the reflux condensing device is connected to the atmosphere through a backup pressure valve), sealed and stirred, heated to 100 ° C, and 5 liters / Continuously feed air in minutes, control the internal pressure of the kettle and keep it at 1MPa. After reacting for 5 hours, cool to room temperature, take out the reaction mixture for analysis, and the analysis results: the conversion rate of cyclohexane is 80%, and the yield of adipic acid is 45%. The main reaction conditions and reaction results are listed in Table 1 for comparison.
Embodiment 2
[0019] 5mol acetic acid, 0.025mol NHPI, 0.025mol NAPI, 0.0025mol cobalt acetate, 0.0025mol manganese acetate, 0.005mol PEG400 and 1mol cyclohexane (that is, the molar ratio of solvent, free radical catalyst, metal catalyst, cocatalyst, cyclohexane 5:0.05:0.005:0.005:1) into a 1-liter high-pressure reactor (with a reflux condensing device, the reflux condensing device is connected to the atmosphere through a backup pressure valve), sealed and stirred, heated to 100 ° C, and 5 liters / Continuously feed air in minutes, control the internal pressure of the kettle and keep it at 1MPa. After reacting for 5 hours, cool to room temperature, take out the reaction mixture for analysis, and the analysis results: the conversion rate of cyclohexane is 65%, and the yield of adipic acid is 30%. The main reaction conditions and reaction results are listed in Table 1 for comparison.
Embodiment 3
[0021]5mol acetic acid, 0.025mol NHPI, 0.025mol NAPI, 0.0025mol cobalt acetate, 0.0025mol manganese acetate, 0.005mol 18-crown-6 and 1mol cyclohexane (i.e. solvent, free radical catalyst, metal catalyst, promoter, cyclohexane The molar ratio of alkanes is 5:0.05:0.005:0.005:1) into a 1-liter high-pressure reactor (with a reflux condensing device, which is connected to the atmosphere through a backup pressure valve), sealed and stirred, and heated to 100 ° C. Air was continuously fed in at 5 liters / minute, and the pressure in the kettle was kept at 1 MPa. After 5 hours of reaction, it was cooled to room temperature, and the reaction mixture was taken out for analysis. The analysis results showed that the conversion rate of cyclohexane was 90%, and the yield of adipic acid was 50%. %, for the convenience of comparison, the main reaction conditions and reaction results are listed in Table 1.
PUM
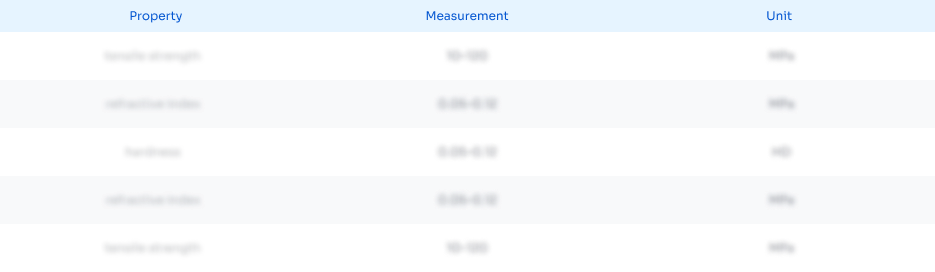
Abstract
Description
Claims
Application Information

- R&D
- Intellectual Property
- Life Sciences
- Materials
- Tech Scout
- Unparalleled Data Quality
- Higher Quality Content
- 60% Fewer Hallucinations
Browse by: Latest US Patents, China's latest patents, Technical Efficacy Thesaurus, Application Domain, Technology Topic, Popular Technical Reports.
© 2025 PatSnap. All rights reserved.Legal|Privacy policy|Modern Slavery Act Transparency Statement|Sitemap|About US| Contact US: help@patsnap.com