Preparation method of micro-capsule fly ash floating bead toughened and reinforced phenolic foam
A technology of fly ash floating beads and phenolic foam is applied in the field of foam materials, which can solve the problems of high brittleness and low strength of phenolic foam, and achieve the effects of improving impact strength, improving compressive strength and good toughness.
- Summary
- Abstract
- Description
- Claims
- Application Information
AI Technical Summary
Problems solved by technology
Method used
Examples
Embodiment 1
[0030] Prepare polyurethane prepolymer: add 20g PEG-200 and 50ml tetrahydrofuran solution to the solution of 69.6gTDI and 100ml tetrahydrofuran, heat up to 60 o C was stirred for 6h, and the solvent was removed under reduced pressure to obtain a polyurethane prepolymer.
[0031] Preparation of microcapsule fly ash floating beads: add 2g of gelatin to 100g of modified fly ash floating beads, then add 10g of polyurethane prepolymer, adjust the pH to 8 with NaOH solution, at 80 o C insulation for 0.5h, drying to obtain polyurethane-coated fly ash floating beads.
[0032] Preparation of phenolic foam: Add 5g of the above-mentioned microcapsule fly ash floating beads to 100g of resole phenolic resin, stir at high speed to obtain a uniform mixture, then add 3g of silicone oil, 9g of pentane, and then add p-toluenesulfonic acid, water and phosphoric acid. 10g of the mixed solution (the mass ratio of p-toluenesulfonic acid, water and phosphoric acid is 2:2:1, the same below), stir vi...
Embodiment 2
[0035] Preparation of polyurethane prepolymer: Add 60g PEG-600 and 50ml THF solution to 69.6g TDI and 100ml THF solution, heat up to 70 o C was stirred for 7h, and the solvent was removed under reduced pressure to obtain a polyurethane prepolymer.
[0036] Preparation of microcapsule fly ash floating beads: add 2g gelatin to 100g modified fly ash floating beads, then add 20g polyurethane prepolymer, adjust the pH to 8 with NaOH solution, at 80 o C insulation 1h, dry to obtain the polyurethane coated fly ash floating beads.
[0037] Preparation of phenolic foam: Add 10g of the above-mentioned microcapsule fly ash floating beads to 100g of resole phenolic resin, stir at high speed to obtain a uniform mixture, then add 4g of silicone oil, 10g of pentane, and then add p-toluenesulfonic acid, water and phosphoric acid. 12g of the mixed solution was poured into the mould, after vigorously stirring evenly, at 70 o C foaming and solidification molding to obtain toughened and strengt...
Embodiment 3
[0040] Preparation of polyurethane prepolymer: Add 100g PEG-1000 and 50ml THF solution to 69.6g TDI and 100ml THF solution, heat up to 70 o C was stirred for 7h, and the solvent was removed under reduced pressure to obtain a polyurethane prepolymer.
[0041] Preparation of microcapsule fly ash floating beads: add 3 g of gelatin to 100 g of modified fly ash floating beads, then add 30 g of polyurethane prepolymer, adjust the pH to 9 with NaOH solution, and adjust the pH to 9 at 80 o C heat preservation 2h, dry and obtain the fly ash floating beads coated with polyurethane.
[0042] Preparation of phenolic foam: Add 20g of the above-mentioned microcapsule fly ash floating beads to 100g of resole phenolic resin, stir at high speed to obtain a uniform mixture, then add 4g of silicone oil, 10g of pentane, and then add p-toluenesulfonic acid, water and phosphoric acid. 12g of the mixed solution was poured into the mould, after stirring vigorously, at 80 o C foaming and solidificat...
PUM
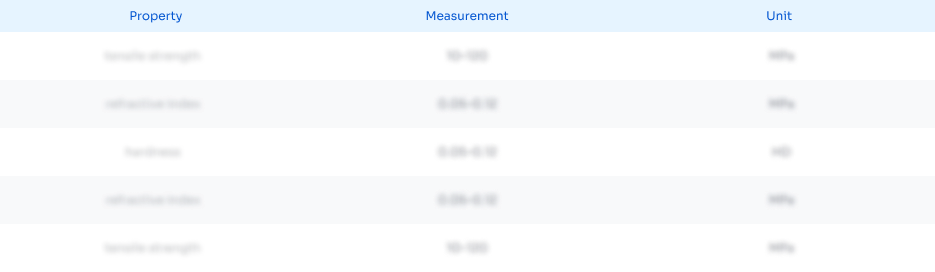
Abstract
Description
Claims
Application Information

- Generate Ideas
- Intellectual Property
- Life Sciences
- Materials
- Tech Scout
- Unparalleled Data Quality
- Higher Quality Content
- 60% Fewer Hallucinations
Browse by: Latest US Patents, China's latest patents, Technical Efficacy Thesaurus, Application Domain, Technology Topic, Popular Technical Reports.
© 2025 PatSnap. All rights reserved.Legal|Privacy policy|Modern Slavery Act Transparency Statement|Sitemap|About US| Contact US: help@patsnap.com