Waterborne light-cured modified chlorinated polypropylene coating polymer for polypropylene films and preparation method and application thereof
A technology of chlorinated polypropylene and polypropylene film, which is applied in the direction of coating, etc., can solve the problems of small force and weak adhesion of printing ink, etc., and achieve improved adhesion, good adhesion effect, and high adhesion Good results
- Summary
- Abstract
- Description
- Claims
- Application Information
AI Technical Summary
Problems solved by technology
Method used
Image
Examples
Embodiment 1
[0029] (1) In parts by weight, take 20 parts of chlorinated polypropylene (35% by mass percentage of chlorine) and 75 parts of butyl acetate and dissolve them in a reactor with a stirrer and a condenser tube, stir for 30min, and heat up to 95°C , add 2 parts of methacrylic acid, 1 part of maleic anhydride, 3 parts of hydroxyethyl methacrylate, 1 part of ethyl acrylate, 1.2 parts of di-tert-butyl peroxide, and react for 9h. Then cool down, add 1 part of pyridine, 0.5 part of 4-dimethylaminopyridine, and 1.2 parts of cinnamoyl chloride under ice bath, and continue to react for 6 hours. ;
[0030] Dissolve 30 parts of the above-mentioned coating polymer in butyl acetate, add 65 parts of water after neutralization, stir and disperse, remove butyl acetate to obtain an emulsion-like polypropylene film with a solid content of 32% and water-based photocuring Modified chlorinated polypropylene coating material.
[0031] (2) Take the coating material and apply a film with a thickness ...
Embodiment 2
[0034] (1) In parts by weight, take 20 parts of chlorinated polypropylene (40% by mass percentage of chlorine) and 65 parts of toluene and dissolve them in a reactor with a stirrer and a condenser tube, stir for 30min, heat up to 100°C, add 2 parts of acrylic acid, 1.3 parts of maleic anhydride, 3 parts of hydroxyethyl methacrylate, 1 part of propyl methacrylate, 1 part of benzoyl peroxide, and react for 7 hours. Then lower the temperature, add 2 parts of triethylamine and 2 parts of cinnamoyl chloride under an ice bath, continue to react for 6 hours, and obtain a polypropylene film after purification with a water-based photocurable modified chlorinated polypropylene coating polymer;
[0035] Take 25 parts of the above-mentioned coating polymer and dissolve it in toluene, add 70 parts of water after neutralization to neutrality, stir and disperse, remove the toluene, and obtain an emulsion-like polypropylene film with a solid content of 26%. Polypropylene coated material.
[...
Embodiment 3
[0039] (1) In parts by weight, take 20 parts of chlorinated polypropylene (35% by mass percentage of chlorine) and 60 parts of toluene and dissolve them in a reactor with a stirrer and a condenser, stir for 30 minutes, heat up to 110°C, add 1 part of acrylic acid, 1 part of maleic anhydride, 2.5 parts of hydroxyethyl methacrylate, 1 part of methyl acrylate, 1.2 parts of benzoyl peroxide, and react for 6 hours. Then cool down, add 2 parts of pyridine and 1.5 parts of cinnamoyl chloride under ice bath, continue to react for 4 hours, and obtain polypropylene film after purification with water-based photocurable modified chlorinated polypropylene coating polymer;
[0040]Dissolve 25 parts of the above-mentioned coating polymer in xylene, add 60 parts of water after neutralization to neutrality, remove toluene after stirring and dispersing, and obtain an emulsion-like polypropylene film with a solid content of 30% and water-based photocurable modified chlorine dioxide. Polypropylen...
PUM
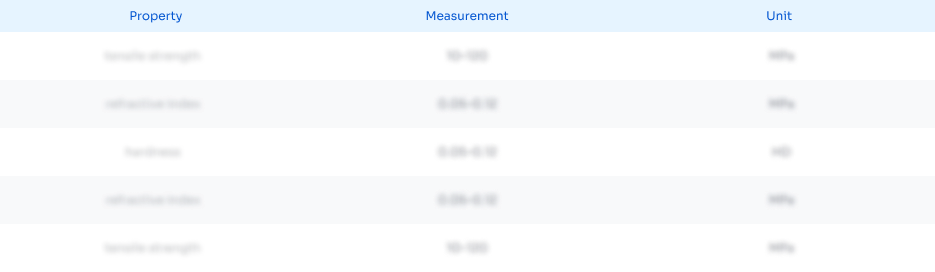
Abstract
Description
Claims
Application Information

- R&D
- Intellectual Property
- Life Sciences
- Materials
- Tech Scout
- Unparalleled Data Quality
- Higher Quality Content
- 60% Fewer Hallucinations
Browse by: Latest US Patents, China's latest patents, Technical Efficacy Thesaurus, Application Domain, Technology Topic, Popular Technical Reports.
© 2025 PatSnap. All rights reserved.Legal|Privacy policy|Modern Slavery Act Transparency Statement|Sitemap|About US| Contact US: help@patsnap.com