Method for preparing bisphenol F
A phenol and solid acid catalyst technology, applied in the chemical industry, can solve the problems of catalyst waste environmental pollution, difficult to recycle catalysts, serious corrosion of instruments and equipment, etc., and achieve easy separation, recovery and reusability, high catalyst activity and catalytic selectivity, Environmentally friendly effect of catalyst
- Summary
- Abstract
- Description
- Claims
- Application Information
AI Technical Summary
Problems solved by technology
Method used
Examples
Embodiment 1
[0017] (1) Preparation of catalyst
[0018] Weigh 60.0g of bentonite and roast at 400°C for 2h; then slowly add 50.0g of 10% methanol solution of phosphotungstic acid to 20.0g of roasted bentonite, react at room temperature for 3h, distill off the solvent, and forge at 300°C Burn for 24h to obtain solid acid catalyst C1.
[0019] (2) Synthesis of Bisphenol F
[0020] Weigh 1.56g of solid acid catalyst C1, 83.8g of phenol and 5.20g of formaldehyde (37%), and add them into the reaction flask. Heating, controlling the reaction temperature at 120°C, stirring for 2 hours, removing the catalyst by filtration, to obtain a solution containing bisphenol F, and performing post-processing such as distillation to obtain bisphenol F product with a yield of 93%.
Embodiment 2
[0022] (1) Preparation of catalyst
[0023] Weigh 60.0g of montmorillonite and roast at 200°C for 8h; then slowly add 50.0g of 5% methanol solution of silicotungstic acid to 22.5g of roasted montmorillonite, react at room temperature for 16h, distill off the solvent, Calcined at 200°C for 24 hours to obtain solid acid catalyst C2.
[0024] (2) Synthesis of Bisphenol F
[0025] Weigh 1.30g of solid acid catalyst C2, 83.8g of phenol and 10.40g of formaldehyde (37%), and add them into the reaction flask. Heating, controlling the reaction temperature at 130°C, stirring and reacting for 4 hours, filtering and removing the catalyst to obtain a solution containing bisphenol F, and carrying out post-processing such as distillation to obtain bisphenol F product with a yield of 77%.
Embodiment 3
[0027] (1) Preparation of catalyst
[0028] Weigh 60.0g of diatomite and roast at 500°C for 2h; then slowly add 50.0g of 20% methanol solution of phosphomolybdic acid to 15.0g of roasted bentonite, react at room temperature for 12h, distill off the solvent, 300°C Calcined for 16 hours to obtain solid acid catalyst C3.
[0029] (2) Synthesis of Bisphenol F
[0030] Weigh 1.30g of solid acid catalyst C3, 83.8g of phenol and 5.2g of formaldehyde (37%), and add them into the reaction flask. Heating, controlling the reaction temperature at 100°C, stirring and reacting for 4 hours, filtering and removing the catalyst to obtain a solution containing bisphenol F, and carrying out post-processing such as distillation to obtain bisphenol F product with a yield of 73%.
PUM
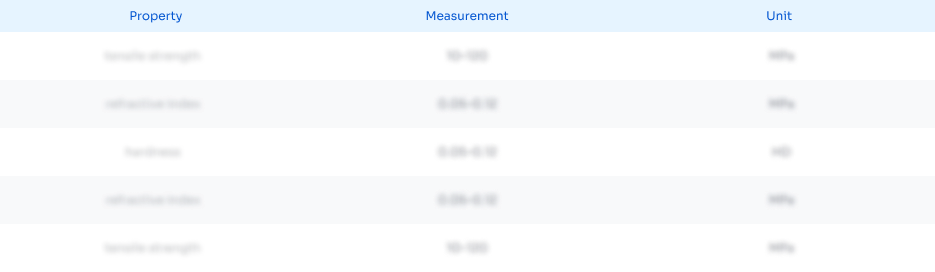
Abstract
Description
Claims
Application Information

- Generate Ideas
- Intellectual Property
- Life Sciences
- Materials
- Tech Scout
- Unparalleled Data Quality
- Higher Quality Content
- 60% Fewer Hallucinations
Browse by: Latest US Patents, China's latest patents, Technical Efficacy Thesaurus, Application Domain, Technology Topic, Popular Technical Reports.
© 2025 PatSnap. All rights reserved.Legal|Privacy policy|Modern Slavery Act Transparency Statement|Sitemap|About US| Contact US: help@patsnap.com