Preparation method of hydroxyapatite/polylactic acid composite coating on the surface of medical magnesium alloy
A technology of hydroxyapatite and composite coating, which is applied to the device for coating liquid on the surface, metal material coating process, coating and other directions to achieve the effect of improving biocompatibility, reducing corrosion rate and avoiding local infection
- Summary
- Abstract
- Description
- Claims
- Application Information
AI Technical Summary
Problems solved by technology
Method used
Image
Examples
Embodiment 1
[0032] (1) Simple pretreatment of the substrate: cut the ZK60 magnesium alloy into moderate-sized samples with a wire cutting machine, and then use 800# and 2000# alumina water-resistant sandpapers in turn to remove the oxide layer on the surface of the magnesium alloy, followed by deionized water. Ultrasonic cleaning with absolute ethanol for 10min, and drying at room temperature for use;
[0033] (2) Acid etching pretreatment: The magnesium alloy substrate obtained by simple pretreatment was placed in a 90% (v%) phosphoric acid solution at 55°C for acid etching treatment for 30s, then placed in a 1M NaOH solution for neutralization treatment for 90s, and then in distilled water. Wash in medium for about 30s and dry for later use.
[0034] (3) Configuration of transformation solution: The transformation solution adopted is prepared from sodium dihydrogen phosphate dihydrate and calcium nitrate tetrahydrate, and a low-concentration transformation solution (as shown in Table 1)...
Embodiment 2
[0041] (1) Simple pretreatment of the substrate: cut the ZK60 magnesium alloy into moderate-sized samples with a wire cutting machine, and then use 800# and 2000# alumina water-resistant sandpapers in turn to remove the oxide layer on the surface of the magnesium alloy, followed by deionized water. Ultrasonic cleaning with absolute ethanol for 10min, and drying at room temperature for use;
[0042] (2) Acid etching pretreatment: The magnesium alloy substrate obtained by simple pretreatment was placed in a 90% (v%) phosphoric acid solution at 55°C for acid etching treatment for 40s, then placed in a 1M NaOH solution for neutralization treatment for 2min, and then in distilled water. Wash in medium for about 30s and dry for later use.
[0043] (3) Configuration of transformation solution: The transformation solution adopted is prepared from sodium dihydrogen phosphate dihydrate and calcium nitrate tetrahydrate, and a low-concentration transformation solution (as shown in Table 1...
Embodiment 3
[0050] (1) Simple pretreatment of the substrate: cut the ZK60 magnesium alloy into moderate-sized samples with a wire cutting machine, and then use 800# and 2000# alumina water-resistant sandpapers in turn to remove the oxide layer on the surface of the magnesium alloy, followed by deionized water. Ultrasonic cleaning with absolute ethanol for 20min, and drying at room temperature for subsequent use;
[0051] (2) Acid etching pretreatment: The magnesium alloy substrate obtained by simple pretreatment was placed in a 90% (v%) phosphoric acid solution at 55°C for acid etching treatment for 30s, then placed in a 1M NaOH solution for neutralization treatment for 90s, and then in distilled water. Wash in medium for about 30s and dry for later use.
[0052] (3) Configuration of transformation solution: The transformation solution adopted is prepared from sodium dihydrogen phosphate dihydrate and calcium nitrate tetrahydrate, and a high-concentration transformation solution (as shown...
PUM
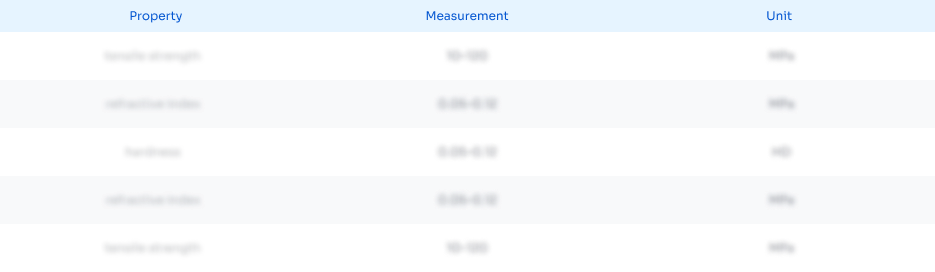
Abstract
Description
Claims
Application Information

- R&D Engineer
- R&D Manager
- IP Professional
- Industry Leading Data Capabilities
- Powerful AI technology
- Patent DNA Extraction
Browse by: Latest US Patents, China's latest patents, Technical Efficacy Thesaurus, Application Domain, Technology Topic, Popular Technical Reports.
© 2024 PatSnap. All rights reserved.Legal|Privacy policy|Modern Slavery Act Transparency Statement|Sitemap|About US| Contact US: help@patsnap.com