Superaustenitic stainless steel electrode
A technology of austenitic stainless steel and electrode, applied in welding medium, welding equipment, welding/cutting medium/material, etc., can solve halide pitting corrosion, pitting corrosion, crevice corrosion stress corrosion, lack of corrosion resistance, sulfuric acid resistance , poor phosphoric acid, etc., to achieve the effect of improving moisture resistance, reducing powder loss, and strong adaptability
- Summary
- Abstract
- Description
- Claims
- Application Information
AI Technical Summary
Problems solved by technology
Method used
Image
Examples
Embodiment 1
[0023] Embodiment 1: the percentage by weight of each component in the drug skin is shown in the following table:
[0024] Raw material name
weight percentage
Raw material name
weight percentage
35
metal chrome
6
Titanium dioxide
5
Electrolytic manganese
6.5
marble
12
ferro-titanium
3
6
Chrome Oxide Green
1
3
2
6.5
0.5
Dehydrated feldspar
8
0.5
Dehydrated Phlogopite
5
[0025] The deposited metal composition of the electrode prepared according to the above ratio is shown in the following table:
[0026]
[0027] The mechanical properties of the deposited metal of the electrode prepared according to the above ratio are shown in the following table:
[0028]
Embodiment 2
[0029] Embodiment 2: the percentage by weight of each component in the drug skin is shown in the following table:
[0030] Raw material name
weight percentage
Raw material name
weight percentage
45
metal chrome
8
Titanium dioxide
2
Electrolytic manganese
8
marble
6
ferro-titanium
4.5
7.5
Chrome Oxide Green
1.5
1
nickel powder
4
3.5
1
Dehydrated feldspar
4
1
Dehydrated Phlogopite
3
[0031] The deposited metal composition of the electrode prepared according to the above ratio is shown in the following table:
[0032]
[0033] The mechanical properties of the deposited metal of the electrode prepared according to the above ratio are shown in the following table:
[0034]
Embodiment 3
[0035] Embodiment 3: the percentage by weight of each component in the drug skin is shown in the following table:
[0036] Raw material name
weight percentage
Raw material name
weight percentage
rutile
40
metal chrome
6
Titanium dioxide
3.5
Electrolytic manganese
5.5
marble
8
ferro-titanium
4
dolomite
8
Chrome Oxide Green
2
quartz
2
nickel powder
3
cryolite
5
1.5
Dehydrated feldspar
6
1.5
Dehydrated Phlogopite
4
[0037] The deposited metal composition of the electrode prepared according to the above ratio is shown in the following table:
[0038]
[0039]
[0040] The mechanical properties of the deposited metal of the electrode prepared according to the above ratio are shown in the following table:
[0041]
[0042] It can be seen from the above three em...
PUM
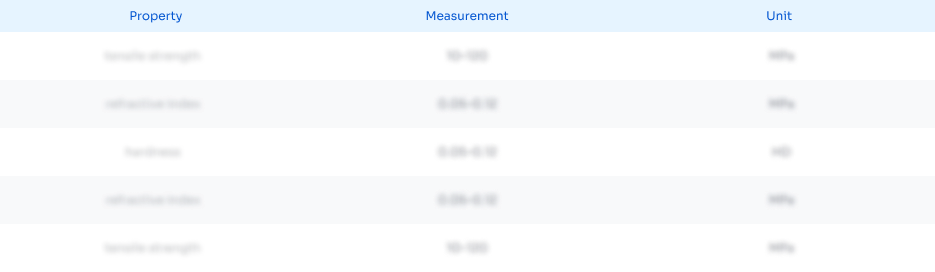
Abstract
Description
Claims
Application Information

- R&D
- Intellectual Property
- Life Sciences
- Materials
- Tech Scout
- Unparalleled Data Quality
- Higher Quality Content
- 60% Fewer Hallucinations
Browse by: Latest US Patents, China's latest patents, Technical Efficacy Thesaurus, Application Domain, Technology Topic, Popular Technical Reports.
© 2025 PatSnap. All rights reserved.Legal|Privacy policy|Modern Slavery Act Transparency Statement|Sitemap|About US| Contact US: help@patsnap.com