A kind of magnesium alloy anodic oxidation method
A technology of anodic oxidation and magnesium alloy, applied in the direction of anodic oxidation, etc., can solve the problems of anodic oxidation film burning, unsatisfactory corrosion resistance, and varying degrees of reaction intensity, so as to reduce alkalinity, reduce chemical corrosion, and reduce oxidation film uniform effect
- Summary
- Abstract
- Description
- Claims
- Application Information
AI Technical Summary
Problems solved by technology
Method used
Image
Examples
Embodiment 1
[0022] A method for anodizing magnesium alloys, comprising the steps of:
[0023] Degreasing: using Na 3 PO 4 10~30g / L, Na 2 CO 3 10~50g / L, OP-102~10ml / L to clean the magnesium alloy sample, remove the oil stain on the surface of the magnesium alloy, the temperature is 40~60℃, and the time is 5~15min.
[0024] Pickling: Use 3-10% dilute nitric acid solution to remove oxides and other dirt on the surface of the magnesium alloy. The temperature is room temperature and the time is 10-30s.
[0025] Alkali etching: Use 50-150g / L NaOH solution to remove the residues produced in the pickling step at a temperature of 70-100°C for 3-15 minutes.
[0026] Anodizing: The electrolyte formula used is NaOH10~100g / L, NaOH 2 SiO 3 10~100g / L and trisodium citrate 2~30g / L. The operating frequency is 300Hz, the positive pulse duty cycle is 10%, the negative pulse duty cycle is 10%, and the positive pulse current density is 1.5A / dm 2 , negative pulse current density 3A / dm 2 , a temperatur...
Embodiment 2
[0030] A method for anodizing magnesium alloys, comprising the steps of:
[0031] Degreasing: using Na 3 PO 4 10~30g / L, Na 2 CO 3 10~50g / L, OP-102~10ml / L to clean the magnesium alloy sample, remove the oil stain on the surface of the magnesium alloy, the temperature is 40~60℃, and the time is 5~15min.
[0032] Pickling: Use 3-10% dilute nitric acid solution to remove oxides and other dirt on the surface of the magnesium alloy. The temperature is room temperature and the time is 10-30s.
[0033] Alkali etching: Use 50-150g / L NaOH solution to remove the residues produced in the pickling step at a temperature of 70-100°C for 3-15 minutes.
[0034] Anodizing: The electrolyte formula used is NaOH10~100g / L, NaOH 2 SiO 3 10~100g / L and trisodium citrate 2~30g / L. The operating frequency is 400Hz, the positive pulse duty cycle is 5%, the negative pulse duty cycle is 10%, and the positive pulse current density is 2A / dm 2 , negative pulse current density 2A / dm 2 , a temperature o...
Embodiment 3
[0037] A method for anodizing magnesium alloys, comprising the steps of:
[0038] Degreasing: using Na 3 PO 4 10~30g / L, Na 2 CO 3 10~50g / L, OP-102~10ml / L to clean the magnesium alloy sample, remove the oil stain on the surface of the magnesium alloy, the temperature is 40~60℃, and the time is 5~15min.
[0039] Pickling: Use 3-10% dilute nitric acid solution to remove oxides and other dirt on the surface of the magnesium alloy. The temperature is room temperature and the time is 10-30s.
[0040] Alkali etching: Use 50-150g / L NaOH solution to remove the residues produced in the pickling step at a temperature of 70-100°C for 3-15 minutes.
[0041] Anodizing: The electrolyte formula used is NaOH10~100g / L, NaOH 2 SiO 3 10~100g / L and trisodium citrate 2~30g / L. The operating frequency is 400Hz, the positive pulse duty cycle is 10%, the negative pulse duty cycle is 5%, and the positive pulse current density is 1A / dm 2 , negative pulse current density 1A / dm 2 , a temperature of ...
PUM
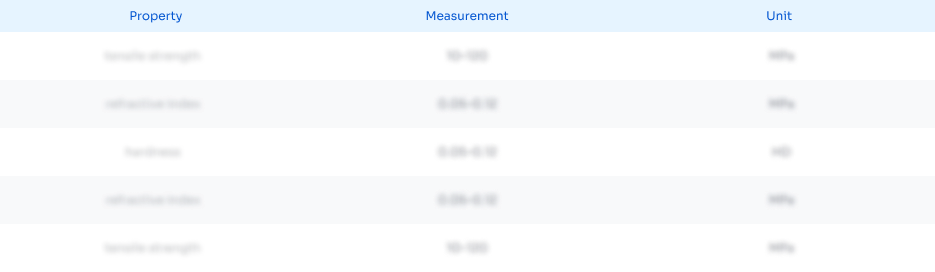
Abstract
Description
Claims
Application Information

- R&D
- Intellectual Property
- Life Sciences
- Materials
- Tech Scout
- Unparalleled Data Quality
- Higher Quality Content
- 60% Fewer Hallucinations
Browse by: Latest US Patents, China's latest patents, Technical Efficacy Thesaurus, Application Domain, Technology Topic, Popular Technical Reports.
© 2025 PatSnap. All rights reserved.Legal|Privacy policy|Modern Slavery Act Transparency Statement|Sitemap|About US| Contact US: help@patsnap.com