Triglycidyl isocyanurate dry powder extruding and pelletizing production line and triglycidyl isocyanurate dry powder extruding and pelletizing production technology
A technology of glycidyl ester and triglycidyl isocyanurate, which is applied in the field of extrusion granulation production line and production process of triglycidyl isocyanurate dry powder, can solve the problem of endangering the physical and mental health of workers, not being easy to break and disperse, and increasing product density and other problems, to achieve the effect of easy crushing and dispersion, maintaining hardness, and effective recycling
- Summary
- Abstract
- Description
- Claims
- Application Information
AI Technical Summary
Problems solved by technology
Method used
Image
Examples
Embodiment 1
[0025] A kind of triglycidyl isocyanurate dry powder extrusion granulation production process of the present invention is characterized in that: comprise wet material drying, dry powder material cyclone separation, melting extruding, put on the belt type cooling conveyor cooling after tabletting, Crushing, screening and packaging, the specific process steps are as follows:
[0026] 1) Add triglycidyl isocyanurate containing 25-30% organic solvent into the vibrating dryer 1 through the material inlet 1-2 of the vibrating dryer 1, open the vibrating dryer 1, and feed the Pass into steam in the cover, and pass into cooling water to condenser 12;
[0027] 2) When the vibrating dryer 1 heats triglycidyl isocyanurate containing 25-30% organic solvent to 70°C, start the condensing vacuum pump I12, and carry out vacuum distillation at a vacuum of 0.1MPa for 2 hours. The above materials are made into dry powder materials with a moisture content of <0.5%, and the volatile organic solve...
Embodiment 2
[0032] The present invention is a triglycidyl isocyanurate dry powder extrusion granulation production process, which is characterized in that it includes drying of materials, cyclone separation of dry powder materials, melt extrusion, tableting, cooling and crushing on a belt cooling conveyor and packaging, the specific process steps are as follows:
[0033] 1) Add triglycidyl isocyanurate containing 25-30% organic solvent into the vibrating dryer 1 through the material inlet 1-2 of the vibrating dryer 1, turn on the vibrating dryer 1, and feed the Pass into steam in the jacket, pass into cooling water to condenser 12;
[0034] 2) When the vibrating dryer 1 heats triglycidyl isocyanurate containing 25-30% organic solvent to 75°C, start the condensing vacuum pump I12, and carry out vacuum distillation at a vacuum of 0.1MPa for 1.5 hours. The above materials are made into dry powder materials with a moisture content of <0.5%, and the volatile organic solvent in the vibrating d...
PUM
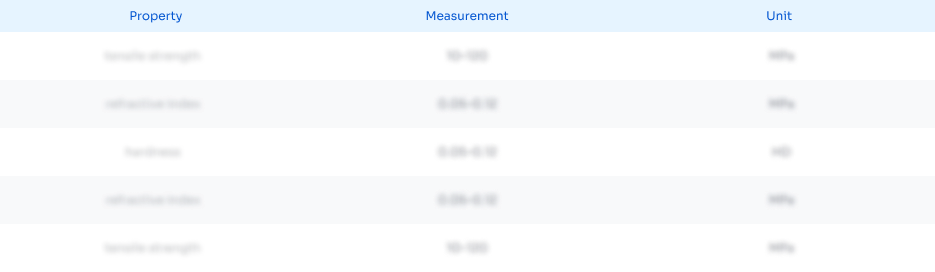
Abstract
Description
Claims
Application Information

- Generate Ideas
- Intellectual Property
- Life Sciences
- Materials
- Tech Scout
- Unparalleled Data Quality
- Higher Quality Content
- 60% Fewer Hallucinations
Browse by: Latest US Patents, China's latest patents, Technical Efficacy Thesaurus, Application Domain, Technology Topic, Popular Technical Reports.
© 2025 PatSnap. All rights reserved.Legal|Privacy policy|Modern Slavery Act Transparency Statement|Sitemap|About US| Contact US: help@patsnap.com