Electromagnetic modulation fusion emitting device
A launching device and electromagnetic technology, applied in the field of three-dimensional molding manufacturing, can solve the problems of high cost, unfavorable health of workers, low strength, etc., and achieve the effects of excellent manufacturing cost and durability, saving powder cleaning process, and improving structural performance.
- Summary
- Abstract
- Description
- Claims
- Application Information
AI Technical Summary
Problems solved by technology
Method used
Image
Examples
Embodiment Construction
[0020] The electromagnetic modulation melting emission device of the present invention will be further described below in conjunction with the accompanying drawings and specific embodiments:
[0021] figure 1 It is a schematic diagram of the structure of the electromagnetic modulation melting emission device of the present invention, figure 2 It is a principle diagram of material melting injection in the electromagnetic modulation melting emission device of the present invention. In the figure, the electromagnetic modulation melting emission device includes an induction heating coil 5, a three-phase linear induction heating coil 9 and a nozzle 11. Directly below the heating coil 5, the periphery of the induction heating coil 5 is provided with a support cylinder 4, the lower end of the support cylinder 4 is connected to the nozzle 11, the upper end of the support cylinder 4 is provided with a wear-resistant bushing 3, and the inner hole of the lower end of the wear-resistant...
PUM
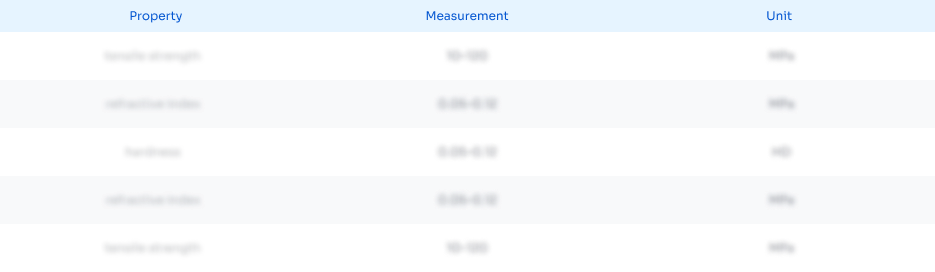
Abstract
Description
Claims
Application Information

- R&D
- Intellectual Property
- Life Sciences
- Materials
- Tech Scout
- Unparalleled Data Quality
- Higher Quality Content
- 60% Fewer Hallucinations
Browse by: Latest US Patents, China's latest patents, Technical Efficacy Thesaurus, Application Domain, Technology Topic, Popular Technical Reports.
© 2025 PatSnap. All rights reserved.Legal|Privacy policy|Modern Slavery Act Transparency Statement|Sitemap|About US| Contact US: help@patsnap.com