Method for manufacturing large cake forgings of high-carbon and high-chromium cold working die steel
A cold work die steel, high carbon and high chromium technology, applied in metal processing equipment and other directions, can solve the problems of low yield, longitudinal cracks at the surface drum, high rejection rate of large cake forgings, and achieve uniform composition and reduced Side drum shape, easy to measure and control the effect
- Summary
- Abstract
- Description
- Claims
- Application Information
AI Technical Summary
Problems solved by technology
Method used
Image
Examples
Embodiment 1
[0031] A method for manufacturing a high-carbon and high-chromium cold-work die steel large-scale cake forging, comprising the following steps:
[0032] a. Smelting: The primary smelting of electric furnace, ladle refining and vacuum degassing process are used for smelting. The composition and mass percentage of the obtained steel are C 1.50%, Mn≤0.60%, Si ≤0.40%, P≤0.030%, S0.008 %, Cr 12.10%, Mo 0.53%, V 0.21%, and the balance is iron; cast into 6 t octagonal ingot after tapping;
[0033] b. Forging cake blank: Send 6 t octagonal ingots to a 4500MN press at a temperature of ≥300°C for forging to a size of 300-500mm in diameter. After the flaw detection is qualified, then the end face is cold-sawed and blanked into a cake blank;
[0034] c. Forging cake forgings: use the above-mentioned lathe cake blank, reheat it to 1150°C~1190°C, then upsetting and forging with a 4500MN press, and finally anneal and lathe to produce large cake forgings of high-carbon and high-chromium cold...
Embodiment 2
[0039] A method for manufacturing a high-carbon and high-chromium cold-work die steel large-scale cake forging, comprising the following steps:
[0040] a. Smelting: The primary smelting of electric furnace, ladle refining and vacuum degassing process are used for smelting. The composition and mass percentage of the obtained steel are C 1.58%, Mn≤0.40%, Si ≤0.40%, P≤0.030%, S0.005 %, Cr 11.72%, Mo 0.75%, V 0.71%, and the balance is iron; cast into 9 t octagonal ingot after tapping;
[0041] b. Forging cake blank: send 9 t octagonal ingots to a 4500MN press at a temperature of ≥500°C for forging to a size of 400-600mm in diameter. After the flaw detection is qualified, then the end face is cold-sawed and blanked into a cake blank;
[0042] c. Forging cake forgings: use the above-mentioned lathe cake blank, reheat it to 1150°C~1190°C, then upsetting and forging with a 4500MN press, and finally anneal and lathe to produce large cake forgings of high-carbon and high-chromium cold...
Embodiment 3
[0047] A method for manufacturing a high-carbon and high-chromium cold-work die steel large-scale cake forging, comprising the following steps:
[0048] a. Smelting: use electric furnace primary smelting, ladle refining and vacuum degassing process to smelt. The composition and mass percentage of the obtained steel are C 1.45%, Mn≤0.60%, Si ≤0.40%, P≤0.030%, S0.003 %, Cr 12.48%, Mo 0.45%, V 0.26%, and the balance is iron; cast into 9 t octagonal ingot after tapping;
[0049] b. Forging cake blank: send 9 t octagonal ingots to a 4500MN press at a temperature of ≥500°C for forging to a size of 400-600mm in diameter. After the flaw detection is qualified, then the end face is cold-sawed and blanked into a cake blank;
[0050] c. Forging cake forgings: use the above-mentioned lathe cake blank, reheat it to 1150°C~1190°C, then upsetting and forging with a 4500MN press, and finally anneal and lathe to produce large cake forgings of high-carbon and high-chromium cold-working die ste...
PUM
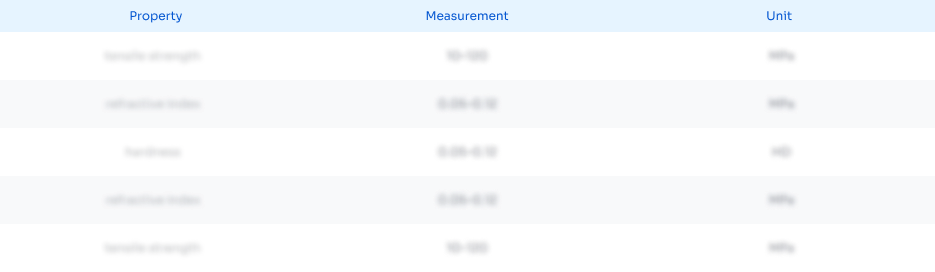
Abstract
Description
Claims
Application Information

- R&D
- Intellectual Property
- Life Sciences
- Materials
- Tech Scout
- Unparalleled Data Quality
- Higher Quality Content
- 60% Fewer Hallucinations
Browse by: Latest US Patents, China's latest patents, Technical Efficacy Thesaurus, Application Domain, Technology Topic, Popular Technical Reports.
© 2025 PatSnap. All rights reserved.Legal|Privacy policy|Modern Slavery Act Transparency Statement|Sitemap|About US| Contact US: help@patsnap.com