A kind of metallographic sample preparation method of plasma spraying tungsten carbide coating
A technology of tungsten carbide coating and metallographic sample, which is applied in the field of metallographic sample preparation of ion sprayed tungsten carbide coating, can solve the problems such as the real judgment of tungsten carbide coating quality, achieve the improvement of preparation level, significant economical Benefits, the effect of huge social benefits
- Summary
- Abstract
- Description
- Claims
- Application Information
AI Technical Summary
Problems solved by technology
Method used
Image
Examples
Embodiment 1
[0028] Sampling of WC coating by wire cutting method (such as figure 1 ). To inlay the sample taken, the volume ratio of Epofix type epoxy resin and curing agent is 15:2, stir, place for 8~15min, pour into the sample ring for curing. Then under 20 Newton / piece pressure, use 120 # 6~8 sheets of sandpaper, 300 rpm, water cooling for rough grinding, after rough grinding, under 20 Newton / piece pressure, 220 # 、320 # 、500 # , 800 # , 1200 # , 2400 # and 4000 # Sandpaper, 2 sheets / model, each sandpaper for 30 seconds, 300 rpm, water cooling for fine grinding. Finally, use a lint-free cloth, conventional lubricant, and 1 μ diamond polishing agent to polish the finely ground sample for 2 minutes at 300 rpm.
[0029] From figure 1 It can be seen that the coating structure is clear, there is no crack, and various damages to the sample can be minimized. Since no alumina powder with a mass ratio of 20% was added to the mixed epoxy resin, the hardness difference between the epox...
Embodiment 2
[0031] The mosaic process was carried out on the sample prepared by the wire cutting method in Example 1. The mosaic process was improved on the commonly used cold mounting method, that is, 20% alumina powder was added to the mixed epoxy resin. The process parameters of cold mounting method are (such as figure 2 ): The volume ratio of Epofix type epoxy resin and curing agent is 15:2, add alumina powder with a mass ratio of 20% to the mixed epoxy resin, stir, place for 8~15min, and then pour into the sample Curing takes place in the ring. Then under 20 Newton / piece pressure, use 120 # 6~8 sheets of sandpaper, 300 rpm, water cooling for rough grinding, after rough grinding, under 20 Newton / piece pressure, 220 # 、320 # 、500 # , 800 # , 1200 # , 2400 # and 4000 # Sandpaper, 2 sheets / model, each sandpaper for 30 seconds, 300 rpm, water cooling for fine grinding. Finally, use a lint-free cloth, conventional lubricant, and 1 μ diamond polishing agent to polish the finely gr...
Embodiment 3
[0034] The samples prepared in Example 2 were subjected to rough grinding, fine grinding and polishing processes. The process parameters of coarse grinding, fine grinding and polishing are (such as image 3 ): Coarse Grinding: 25 N / piece under pressure, 120 # 6~8 sheets of sandpaper, 300 rpm, water cooling; fine grinding: 25 Newtons / piece pressure, 220 # 、320 # 、500 # , 800 # , 1200 # , 2400 # and 4000 # Sandpaper, 2 sheets / model, 30 seconds per sandpaper, 300 rpm, water cooling; polishing: lint-free cloth, conventional lubricant, 1μ diamond polishing agent, 300 rpm, polishing for 2 minutes.
[0035] From image 3 It can be seen that with figure 2 compared to, image 3The coating structure in Fig. 1 is in line with the typical morphology of WC coatings. Although there are holes, the edges of the holes are clear and angular, indicating that these holes exist in the original WC coating and reflect the real structure of the coating.
PUM
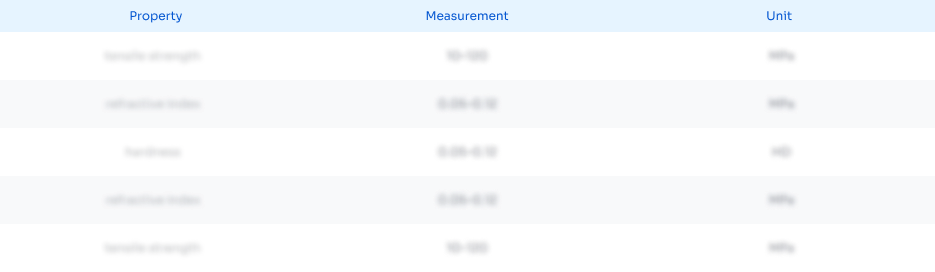
Abstract
Description
Claims
Application Information

- R&D
- Intellectual Property
- Life Sciences
- Materials
- Tech Scout
- Unparalleled Data Quality
- Higher Quality Content
- 60% Fewer Hallucinations
Browse by: Latest US Patents, China's latest patents, Technical Efficacy Thesaurus, Application Domain, Technology Topic, Popular Technical Reports.
© 2025 PatSnap. All rights reserved.Legal|Privacy policy|Modern Slavery Act Transparency Statement|Sitemap|About US| Contact US: help@patsnap.com