Method for modifying aluminium profile for buildings
A technology for aluminum profiles and construction, which is applied in the direction of metal material coating technology, etc., can solve the problems such as the performance of aluminum alloy profiles that needs to be improved, and achieve the effects of small loss, improved performance, and good performance
- Summary
- Abstract
- Description
- Claims
- Application Information
AI Technical Summary
Problems solved by technology
Method used
Image
Examples
Embodiment 1
[0034] Aluminum profile preparation: Melt aluminum ingots into liquid aluminum, add zirconium-wrapped titanium dioxide and zirconium-wrapped silica mixed powders at a mass ratio of 1:2, the mixed powders account for 0.5% of the mass of the aluminum ingots, and then melt at the melting temperature Keep it for 3 hours; then pour it into a mold above 600°C under a pressure of 1.1MPa. After pouring into the mold, cool it to 350°C at a rate of 60-80°C per hour, then keep it warm for 2 hours, and then cool it at a rate of 30°C per hour to Insulate at 80°C for 1 hour; then cool at room temperature and release the aluminum profile.
[0035] Preparation of bright and anti-corrosion aluminum profiles:
[0036] Modifier preparation: prepare 40 parts of sodium fluoride, 60 parts of ammonium bifluoride, 20 parts of potassium permanganate, 50 parts of potassium chromate, 25 parts of zinc phosphate, 18 parts of sodium nitrate, 12 parts of praseodymium chloride, and 16 parts of diaminetetraa...
Embodiment 2
[0042] Aluminum profile preparation: Melt aluminum ingots into liquid aluminum, add zirconium-wrapped titanium dioxide and zirconium-wrapped silica mixed powders at a mass ratio of 1:3, the mixed powders account for 1.2% of the mass of the aluminum ingot, and then melt at the melting temperature Keep it for 5 hours; then pour it into a mold above 600°C under a pressure of 1.5MPa, cool it to 450°C at a rate of 80°C per hour after pouring into the mold, keep it for 3 hours, and then cool it to 100°C at a rate of 40°C per hour Keep warm for 2 hours; then cool at room temperature and demould the aluminum profile.
[0043] Preparation of bright and anti-corrosion aluminum profiles:
[0044] Modifier preparation: prepare 40 parts of sodium fluoride, 60 parts of ammonium bifluoride, 20 parts of potassium permanganate, 40-50 parts of potassium chromate, 25 parts of zinc phosphate, 18 parts of sodium nitrate, and 12 parts of praseodymium chloride by weight , 16 parts of ethylenediamin...
Embodiment 3
[0050] Aluminum profile preparation: Melt aluminum ingots into liquid aluminum, add zirconium-wrapped titanium dioxide and zirconium-wrapped silica mixed powders at a mass ratio of 1:2-3, the mixed powders account for 0.9% of the mass of the aluminum ingots, and then melt Keep at the temperature for 4 hours; then pour it into a mold above 600°C under a pressure of 1.3MPa, pour it into the mold and cool it to 390°C at a rate of 70°C per hour, then keep it for 2.5 hours, and then cool it at a rate of 38°C per hour to Insulate at 90°C for 1.5 hours; then cool at room temperature and release the aluminum profile.
[0051] Preparation of bright and anti-corrosion aluminum profiles:
[0052] Modifier preparation: prepare 26 parts of sodium fluoride, 40 parts of ammonium bifluoride, 18 parts of potassium permanganate, 46 parts of potassium chromate, 19 parts of zinc phosphate, 12 parts of sodium nitrate, 9 parts of praseodymium chloride, and 13 parts of diaminetetraacetic acid, 9 pa...
PUM
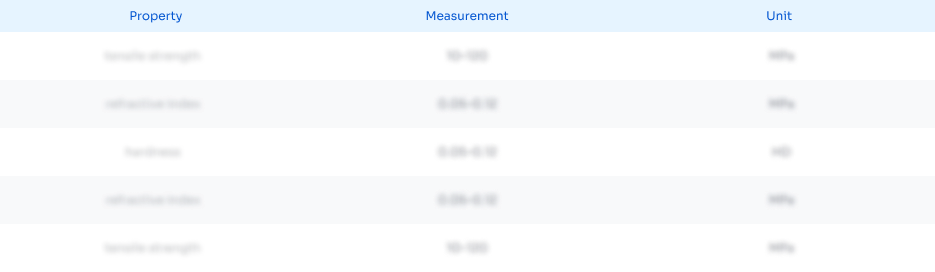
Abstract
Description
Claims
Application Information

- Generate Ideas
- Intellectual Property
- Life Sciences
- Materials
- Tech Scout
- Unparalleled Data Quality
- Higher Quality Content
- 60% Fewer Hallucinations
Browse by: Latest US Patents, China's latest patents, Technical Efficacy Thesaurus, Application Domain, Technology Topic, Popular Technical Reports.
© 2025 PatSnap. All rights reserved.Legal|Privacy policy|Modern Slavery Act Transparency Statement|Sitemap|About US| Contact US: help@patsnap.com