Method for recycling silicon cutting sand by utilizing countercurrent washing of silicon cutting waste sand cake
A technology of cutting waste sand and countercurrent washing, which is applied to chemical instruments and methods, solid waste removal, silicon carbide, etc., can solve the problem that the washing effect cannot reach the purity of silicon crystal cutting sand, increase the cost of silicon crystal cutting sand recycling, and consume Large amount of water and other problems, to achieve the effect of eradicating lye pollution sources, eliminating re-pollution, and reducing consumption
- Summary
- Abstract
- Description
- Claims
- Application Information
AI Technical Summary
Problems solved by technology
Method used
Image
Examples
Embodiment Construction
[0013] Specific embodiments of the present invention will be described in detail below in conjunction with the accompanying drawings.
[0014]As shown in Figure 1, as shown in the process flow chart of utilizing silicon crystal cutting waste sand cake four-stage countercurrent washing to reclaim silicon crystal cutting sand, the silicon crystal cutting waste sand cake in the feed tank 13 and the diluent in the liquid tank 15 are sent to Mix in the stirring tank 12, and prepare a suspension that can be transported. In this implementation, the solid mass concentration of the waste sand cake in the suspension is 30%. Then use the feed pump 11 to constantly transport the waste sand cake suspension to the inlet pipeline before the first-stage delivery pump 10, and after mixing with the overflow from the second-stage washing cyclone group 5, the first-stage The mixed suspension is transported into the first-stage cyclone group 6 by the first-stage delivery pump 10; the overflow from...
PUM
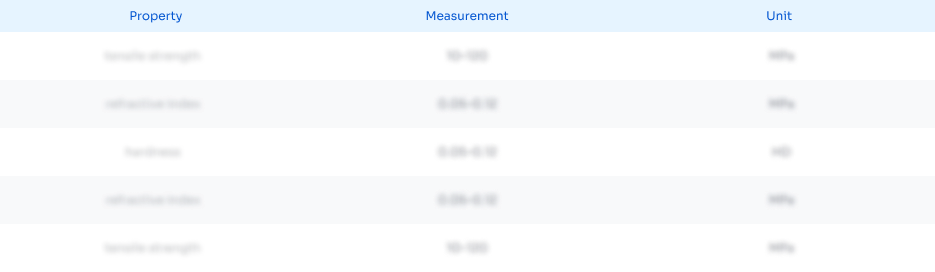
Abstract
Description
Claims
Application Information

- R&D
- Intellectual Property
- Life Sciences
- Materials
- Tech Scout
- Unparalleled Data Quality
- Higher Quality Content
- 60% Fewer Hallucinations
Browse by: Latest US Patents, China's latest patents, Technical Efficacy Thesaurus, Application Domain, Technology Topic, Popular Technical Reports.
© 2025 PatSnap. All rights reserved.Legal|Privacy policy|Modern Slavery Act Transparency Statement|Sitemap|About US| Contact US: help@patsnap.com