Method for preparing heat-conductive composite material
A technology of heat-conducting composite materials and heat-conducting fillers, applied in the field of preparing heat-conducting composite materials, can solve problems such as low production efficiency, poor mechanical properties, and good mechanical properties, and achieve the effects of improving mechanical properties, improving dispersion, and increasing thermal conductivity
- Summary
- Abstract
- Description
- Claims
- Application Information
AI Technical Summary
Problems solved by technology
Method used
Image
Examples
Embodiment 1
[0049] A raw material of a polyethylene-based heat-conducting composite material includes the following components and contents in parts by weight:
[0050]
[0051] The first step, at first prepare raw materials by above-mentioned components;
[0052] In the second step, first place the thermally conductive filler boron nitride in an oven at 100 °C for 6 hours;
[0053] In the third step, the dry boron nitride and high-density polyethylene obtained in the second step are pre-mixed in a high-density polyethylene mixer for 5 minutes at a speed of 100 rpm to obtain a thermally conductive filler and high-density polyethylene premix ;
[0054] Then, put the obtained thermally conductive filler and high-density polyethylene premix into a twin-screw extruder for melt blending, extrusion, and granulation to obtain premixed composite particles of high-density polyethylene and boron nitride. The pellets were dried in a forced air oven at 100°C for 3 hours. The temperatures of fee...
Embodiment 2
[0061] A raw material of a polyethylene-based heat-conducting composite material includes the following components and contents in parts by weight:
[0062]
[0063] The first step, at first prepare raw materials by above-mentioned components;
[0064] In the second step, first place the thermally conductive filler boron nitride in an oven at 100 °C for 6 hours;
[0065] In the third step, the dry boron nitride and high-density polyethylene obtained in the second step are pre-mixed in a high-density polyethylene mixer for 5 minutes at a speed of 100 rpm to obtain a thermally conductive filler and high-density polyethylene premix ;
[0066] Then, put the obtained thermally conductive filler and high-density polyethylene premix into a twin-screw extruder for melt blending, extrusion, and granulation to obtain premixed composite particles of high-density polyethylene and boron nitride. The pellets were dried in a forced air oven at 100°C for 3 hours. The temperatures of fee...
Embodiment 3
[0072] A raw material of a nylon-6 base heat-conducting composite material includes the following components and contents in parts by weight:
[0073]
[0074] The first step, at first prepare raw materials by above-mentioned components;
[0075] In the second step, dry the thermally conductive filler boron nitride in an oven at 100 °C for 6 hours; place nylon-6 in a blast oven at 100 °C for 3 hours;
[0076] In the third step, the dry boron nitride obtained above and dry nylon-6 are placed together in a high mixer for premixing for 5 minutes at a speed of 100 rpm to obtain a thermally conductive filler and nylon-6 premix;
[0077] Then, put the obtained thermally conductive filler and nylon-6 premix into a twin-screw extruder for melt blending, extrusion, and granulation to obtain premixed composite particles of nylon-6 and boron nitride, and premix the composite particles in the Dry in a blast oven at 100°C for 3 hours. The temperatures of feed port, conveying section, ...
PUM
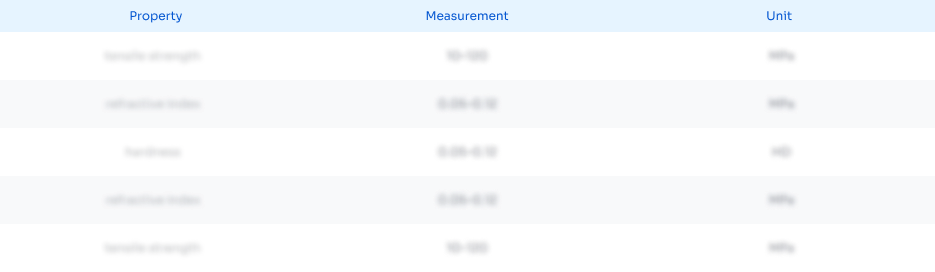
Abstract
Description
Claims
Application Information

- R&D
- Intellectual Property
- Life Sciences
- Materials
- Tech Scout
- Unparalleled Data Quality
- Higher Quality Content
- 60% Fewer Hallucinations
Browse by: Latest US Patents, China's latest patents, Technical Efficacy Thesaurus, Application Domain, Technology Topic, Popular Technical Reports.
© 2025 PatSnap. All rights reserved.Legal|Privacy policy|Modern Slavery Act Transparency Statement|Sitemap|About US| Contact US: help@patsnap.com