Nano-copper-cobalt bimetallic catalyst as well as preparation method and application thereof
A bimetallic catalyst and nano-copper technology, applied in the direction of metal/metal oxide/metal hydroxide catalyst, hydroxyl compound preparation, organic compound preparation, etc., can solve the problem of low carrier content, low specific surface area, easy sintering of catalyst, etc. problem, to achieve the effect of high dispersion, good stability and high selectivity
- Summary
- Abstract
- Description
- Claims
- Application Information
AI Technical Summary
Problems solved by technology
Method used
Image
Examples
Embodiment 1
[0033] 0.3574 g lanthanum nitrate, 0.1665 g cobalt nitrate, 0.0589 g copper nitrate, 0.4088 g citric acid and 0.0242 g ethylene glycol were dissolved in 2.1 ml deionized water. An equal volume of the above solution was impregnated in 2.1 g of ZrO 2 on the carrier. Stand for aging for 24 hours, then dry at 120°C for 24 hours, heat up at 2°C / min to 300°C for 2 hours, and repeat the above impregnation and drying process once. Finally, heat up to 300°C at 2°C / min and bake for 2 hours, and then heat up to 650°C for 5 hours at the same heating rate to obtain ZrO 2 Loaded LaCo 0.7 Cu 0.3 o 3 . Among them, Cu is 1.34%, Co is 3.16%, La 2 o 3 11.52%, ZrO 2 It was 83.98%.
[0034] The catalyst precursor that gets 0.8g above-mentioned method preparation is packed in the reactor, with the volume space velocity being 2000h -1 Access to H 2 The mixed gas of hydrogen and argon with a volume fraction of 5% was raised to 550° at a rate of 10°C / min for reduction for 3 hours, cooled na...
Embodiment 2
[0037] 1.5258 g of lanthanum nitrate, 0.7106 g of cobalt nitrate, 0.2515 g of copper nitrate, 1.7450 g of citric acid, and 0.096 g of ethylene glycol were dissolved in 1.2 ml of deionized water. An equal volume of the above solution was immersed in 1.2g Al 2 o 3 on the carrier. The obtained solid was left to age for 24 hours, and then dried at 120° C. for 24 hours. Raise the temperature at 2°C / min to 300°C for 2 hours, and then use the same heating rate to 650°C for 5 hours to obtain Al 2 o 3 Loaded LaCo 0.7 Cu 0.3 o 3 . Among them, Cu is 3.36%, Co is 7.84%, La 2 o 3 28.8%, Al 2 o 3 60%.
[0038] Get 0.8g of the catalyst precursor prepared by the above-mentioned method, pack in the reactor, take volume space velocity as 2000h -1 Access to H 2 A mixture of hydrogen and nitrogen with a volume fraction of 5% was raised to 660°C at a rate of 10°C / min for reduction for 3 hours. Cool naturally to room temperature and pass through H 2 Syngas with CO in a molar ratio o...
Embodiment 3
[0040] The preparation process of the catalyst precursor is the same as in Example 2, except that the Al 2 o 3 The carrier is replaced by CeO 2 carrier; the drying temperature was changed from 120°C to 80°C to obtain CeO 2 Loaded LaCo 0.7 Cu 0.3 o 3 catalyst precursor.
[0041] Get this catalyst precursor of 0.8g and pack in the reactor, be placed in volume space velocity and be 1500h -1 , in a mixture of hydrogen and carbon monoxide with a volume fraction of 5%, rise to 450° at a rate of 2°C / min for reduction for 3 hours, then naturally cool down to room temperature and feed H 2 Syngas with CO in a molar ratio of 2:1. The pressure is increased to 3MPa, the temperature is set to 340°C, and the space velocity of the syngas is set to 3900h -1 . The measured conversion rate of carbon monoxide is 80.28%, the selectivity of low-carbon alcohol is 48.64%, and the space-time yield of total alcohol is 207.5g / kg cat .h. The conversion rate of CO on the catalyst and the distri...
PUM
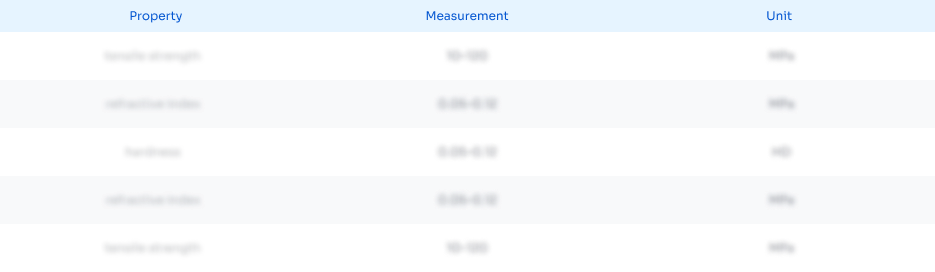
Abstract
Description
Claims
Application Information

- R&D
- Intellectual Property
- Life Sciences
- Materials
- Tech Scout
- Unparalleled Data Quality
- Higher Quality Content
- 60% Fewer Hallucinations
Browse by: Latest US Patents, China's latest patents, Technical Efficacy Thesaurus, Application Domain, Technology Topic, Popular Technical Reports.
© 2025 PatSnap. All rights reserved.Legal|Privacy policy|Modern Slavery Act Transparency Statement|Sitemap|About US| Contact US: help@patsnap.com