Method for continuous preparation of aluminum-base in-situ composite material
A technology of in-situ composite materials and aluminum-based composite materials, which is applied in the field of aluminum-based composite materials, can solve the problems of overall quality degradation of aluminum-based in-situ composite materials, severe gas absorption of aluminum and aluminum alloy melts, and increased maintenance costs and difficulties and other issues, to achieve the effect of easy industrial application, mature core technology and continuous preparation
- Summary
- Abstract
- Description
- Claims
- Application Information
AI Technical Summary
Problems solved by technology
Method used
Image
Examples
Embodiment 1
[0020] This example specifically implements a method for continuously preparing alumina particle-reinforced aluminum-based in-situ composite materials. 2 Powder and ZL101A alloy at a temperature of 630°C are added to a helical rheological extrusion device for mixing; among them, SiO 2 The amount of powder added accounts for 20% of the mass of the ZL101A alloy melt. The helical rheological extrusion device is made of hot-work die steel, and the part in contact with the aluminum melt is treated with plasma sprayed silicon nitride ceramics. It adopts a double helix form with a helix pitch of 2mm, inner cavity diameter 20mm, during use, the inner cavity temperature of the device is maintained at 630°C, and the screw rotation speed is 100r / min; the extruded mixture undergoes a chemical reaction in the tube connected to the outlet of the screw extrusion device, and the temperature of the high-temperature heating tube is The temperature is 900℃, made of silicon nitride ceramic materi...
Embodiment 2
[0023] This example specifically implements a method for continuously preparing TiC particle-reinforced aluminum-based in-situ composite materials. The specific process is: titanium powder with an average size of 30 μm and graphite powder with an average size of 10 μm that have been preheated at 350 ° C for 30 minutes The mixture and the ZL102 alloy at a temperature of 635 ° C are added to the helical rheological extrusion device for mixing; wherein, the mass ratio of titanium powder and graphite powder is 4:1, and the amount of the mixture powder accounts for 25% of the mass of the ZL102 alloy melt. The helical rheological extrusion device is made of hot work die steel, and the part in contact with the aluminum melt is treated with plasma sprayed silicon nitride ceramics. It adopts a double helix form with a helix pitch of 5mm and an inner cavity diameter of 40mm. During use, the inner cavity of the device The temperature is maintained at 635°C, and the screw rotation speed is...
Embodiment 3
[0026] This embodiment specifically implements a continuous preparation of TiB 2 The method of particle reinforced aluminum-based in-situ composite materials, the specific process is: the titanium powder with an average size of 30 μm and the B 2 o 3 The mixture of powder and ZL105 alloy at a temperature of 625°C is added to the helical rheological extrusion device for mixing; among them, titanium powder and B 2 o 3The mass ratio of the powder is 2:3, and the amount of the mixture powder accounts for 30% of the mass of the ZL105 alloy melt. The spiral rheological extrusion device is made of hot-working die steel, and the part in contact with the aluminum melt is made of plasma sprayed silicon nitride ceramics. The treatment adopts double helix form, the helix pitch is 4mm, and the inner cavity diameter is 30mm. During use, the inner cavity temperature of the device is maintained at 625°C, and the screw rotation speed is 200r / min; the extruded mixture is connected to the outle...
PUM
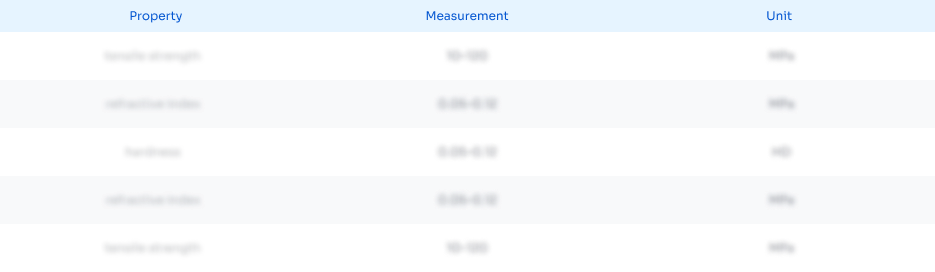
Abstract
Description
Claims
Application Information

- R&D
- Intellectual Property
- Life Sciences
- Materials
- Tech Scout
- Unparalleled Data Quality
- Higher Quality Content
- 60% Fewer Hallucinations
Browse by: Latest US Patents, China's latest patents, Technical Efficacy Thesaurus, Application Domain, Technology Topic, Popular Technical Reports.
© 2025 PatSnap. All rights reserved.Legal|Privacy policy|Modern Slavery Act Transparency Statement|Sitemap|About US| Contact US: help@patsnap.com