Oxygen-enriched side-blown double-zone molten pool smelting furnace and method for smelting matte copper-containing complex materials
A molten pool smelting furnace, molten pool technology, applied in furnaces, electric furnaces, rotary drum furnaces and other directions, can solve the problems of no reasonable sedimentation separation space, inability to quickly and completely separate, maintenance and maintenance difficulties, etc., and achieve significant energy saving and consumption reduction. The effect of improving bed energy rate and easy operation
- Summary
- Abstract
- Description
- Claims
- Application Information
AI Technical Summary
Problems solved by technology
Method used
Image
Examples
Embodiment 1
[0033] For materials containing 1.8% copper, add calcium carbide slag with a weight ratio of 8%, and mix the copper-containing material and flux with a weight ratio of CaO: 10%, MgO: 7%, and a ratio of Fe / SiO2 of 1.5. And pressed into bricks or balls by a brick making machine, air-dried and sent to the oxygen-enriched side-blown double-zone melting pool melting furnace, coke is added to the melting furnace according to 20% of the raw material weight; Enter O 2 Oxygen-enriched air with a concentration of 24%, tuyere pressure of 0.15Mpa, output copper matte containing 20% copper, and slag containing 0.5% copper, the matte is crushed and put into storage, and the slag is sent to the slag dump after being cooled by circulating water , The flue gas is separated into soot and sulfur-containing flue gas by the dust collection device, and the flue gas is collected and reused as copper-containing materials mixed with raw materials, and the flue gas is discharged after desulfurization...
Embodiment 2
[0035] For materials containing 2% copper, add a mixture of quartz stone and calcium carbide slag with a weight ratio of 20%, and mix the copper-containing material and flux with a weight ratio of CaO: 15%, MgO: 9%, and a ratio of Fe / SiO2 of 1.8 Mix evenly, and press it into bricks or balls by a brick making machine. After air drying, send them to the oxygen-enriched side-blown double-zone molten pool melting furnace. Coke is added to the melting furnace according to 18% of the raw material weight; The vent feeds into the O 2 Oxygen-enriched air with a concentration of 40%, tuyere pressure of 0.12Mpa, output copper matte with a copper content of 32%, and slag with a copper content of 0.4%. , The flue gas is separated into soot and sulfur-containing flue gas by the dust collection device, and the flue gas is collected and reused as copper-containing materials mixed with raw materials, and the flue gas is discharged after desulfurization.
Embodiment 3
[0037]For a material containing 3% copper, add quartz stone with a weight ratio of 15%, and mix the copper-containing material and flux with a weight ratio of CaO: 12%, MgO: 8%, and a ratio of Fe / SiO2 of 1.5. The brick making machine is pressed into bricks or balls, and after being air-dried, it is sent to the oxygen-enriched side-blown double-zone melting pool melting furnace. 2 Oxygen-enriched air with a concentration of 27%, tuyere pressure of 0.14Mpa, coke added to the molten pool is 3% of the slag, and matte with copper content of 35% is produced, and slag with copper content of 0.5% is produced. The slag is cooled by circulating water and sent to the slag dump. The flue gas is separated into soot and sulfur-containing flue gas by the dust collection device. After the flue dust is collected, it is mixed with copper-containing materials and raw materials for reuse. The flue gas is discharged after desulfurization.
PUM
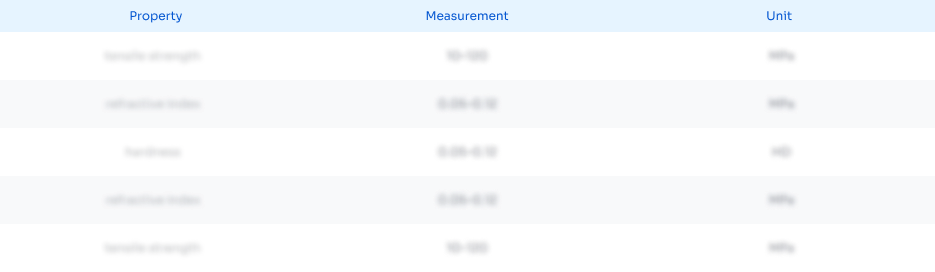
Abstract
Description
Claims
Application Information

- Generate Ideas
- Intellectual Property
- Life Sciences
- Materials
- Tech Scout
- Unparalleled Data Quality
- Higher Quality Content
- 60% Fewer Hallucinations
Browse by: Latest US Patents, China's latest patents, Technical Efficacy Thesaurus, Application Domain, Technology Topic, Popular Technical Reports.
© 2025 PatSnap. All rights reserved.Legal|Privacy policy|Modern Slavery Act Transparency Statement|Sitemap|About US| Contact US: help@patsnap.com