Printing and dyeing process of denim
A printing and dyeing technology, denim technology, applied in the direction of dyeing, textile and papermaking, can solve the problems of difficult quality control, long process route, high cost, and achieve the effects of rich colors, simple operation and less environmental pollution
- Summary
- Abstract
- Description
- Claims
- Application Information
AI Technical Summary
Problems solved by technology
Method used
Examples
Embodiment 1
[0018] A printing and dyeing process for denim, comprising the steps of:
[0019] 1) Pre-treatment gray cloth: treat the gray cloth with alkali, refining agent and hydrogen peroxide, and dehydrate and shape it;
[0020] 2) Paste printing: Prepare printing paste, pigment printing paste and sulfur dye printing paste, the viscosity is controlled at 40000Pa·S, printed on flat screen printing machine, and dried at 100°C;
[0021] The pigment printing paste is prepared by 14 parts by mass of dye paste, 30 parts by mass of water-based polyurethane adhesive, 45 parts by mass of emulsified paste, and 7 parts by mass of urea;
[0022] The sulfur dye printing paste is prepared by 7 parts by mass of sulfur dye, 25 parts by mass of sodium formaldehyde sulfoxylate dihydrate, 30 parts by mass of etherified starch paste, 12 parts by mass of soda ash, 8 parts by mass of glycerin, and 16 parts by mass of warm water;
[0023] 3) Steaming: temperature 90°C, 20 minutes;
[0024] 4) Water washing...
Embodiment 2
[0029] A printing and dyeing process for denim, comprising the steps of:
[0030] 1) Pre-treatment gray cloth: treat the gray cloth with alkali, refining agent and hydrogen peroxide, and dehydrate and shape it;
[0031] 2) Paste printing: Prepare printing paste, pigment printing paste and sulfur dye printing paste, the viscosity is controlled at 45000Pa·S, flat screen printing machine printing, drying at 105°C;
[0032] The pigment printing paste is prepared by 16 parts by mass of dye paste, 35 parts by mass of water-based polyurethane adhesive, 50 parts by mass of emulsified paste, and 9 parts by mass of urea;
[0033] The sulfur dye printing paste is prepared by 8 parts by mass of sulfur dye, 30 parts by mass of sodium formaldehyde sulfoxylate dihydrate, 35 parts by mass of etherified starch paste, 14 parts by mass of soda ash, 9 parts by mass of glycerin, and 18 parts by mass of warm water;
[0034] 3) Steaming: temperature 92°C, 25 minutes;
[0035] 4) Water washing: use...
Embodiment 3
[0040] A printing and dyeing process for denim, comprising the steps of:
[0041] 1) Pre-treatment gray cloth: treat the gray cloth with alkali, refining agent and hydrogen peroxide, and dehydrate and shape it;
[0042] 2) Paste printing: Prepare printing paste, pigment printing paste and sulfur dye printing paste, the viscosity is controlled at 43000Pa·S, printed on flat screen printing machine, and dried at 103°C;
[0043] The pigment printing paste is prepared by 15 parts by mass of dye paste, 32 parts by mass of water-based polyurethane adhesive, 48 parts by mass of emulsified pulp, and 7.9 parts by mass of urea;
[0044] The sulfur dye printing paste is prepared by 7.8 parts by mass of sulfur dye, 28 parts by mass of sodium formaldehyde sulfoxylate dihydrate, 33 parts by mass of etherified starch paste, 13 parts by mass of soda ash, 8.9 parts by mass of glycerin, and 17 parts by mass of warm water;
[0045] 3) Steaming: temperature 91°C, 23 minutes;
[0046] 4) Water wa...
PUM
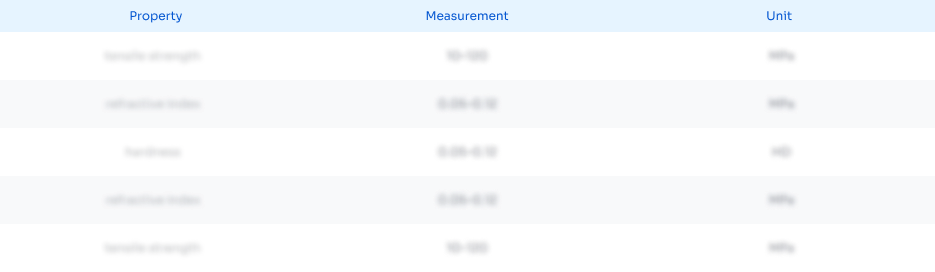
Abstract
Description
Claims
Application Information

- R&D
- Intellectual Property
- Life Sciences
- Materials
- Tech Scout
- Unparalleled Data Quality
- Higher Quality Content
- 60% Fewer Hallucinations
Browse by: Latest US Patents, China's latest patents, Technical Efficacy Thesaurus, Application Domain, Technology Topic, Popular Technical Reports.
© 2025 PatSnap. All rights reserved.Legal|Privacy policy|Modern Slavery Act Transparency Statement|Sitemap|About US| Contact US: help@patsnap.com