Heavy rear earth adhering method of sintered NdFeB magnet
A heavy rare earth and magnet technology, applied in the direction of magnetic objects, magnetic materials, inorganic materials, etc., can solve the problems of difficult control of coating thickness, difficulty in mass production, and low production efficiency.
- Summary
- Abstract
- Description
- Claims
- Application Information
AI Technical Summary
Problems solved by technology
Method used
Image
Examples
Embodiment 1
[0022] (1) Formulated as an organic solvent of dysprosium salt
[0023] Take a certain amount of Dy(NO 3 )·6H 2 O and anhydrous citric acid are dissolved in dichloromethane organic solution, and the dissolved concentrations are 2.5mol / L and 2.6mol / L, respectively.
[0024] (2) Use graphite with a smooth surface as the anode and NdFeB magnet as the cathode, place it in the above-mentioned prepared dysprosium salt organic solution, and pass a direct current with a current density of 0.05A / cm 2 . Duration 10min. The temperature is 30°C. Take the NdFeB magnet coated with a dysprosium metal layer on the surface from the solution; place the air-dried magnet in a vacuum heat treatment furnace, and perform primary tempering at 850°C for 10h in an Ar atmosphere, and secondary tempering at 500°C for 2h .
Embodiment 2
[0026] (1) Preparation of terbium salt organic solvent
[0027] Take a certain amount of Tb (NO 3 )·6H 2 O and anhydrous citric acid are dissolved in the formamide organic solution, and the dissolved concentrations are 0.08mol / L and 0.09mol / L, respectively.
[0028] (2) Use graphite with a smooth surface as the anode and NdFeB magnet as the cathode, place it in the above-prepared dysprosium salt organic solution, and pass a direct current with a current density of 20A / cm 2 . Duration 5min. The temperature is 30°C. Take the NdFeB magnet coated with dysprosium metal film on the surface from the solution; place the air-dried magnet in a vacuum heat treatment furnace, and perform primary tempering at 900°C for 3h in an Ar atmosphere, and secondary tempering at 500°C for 1h .
PUM
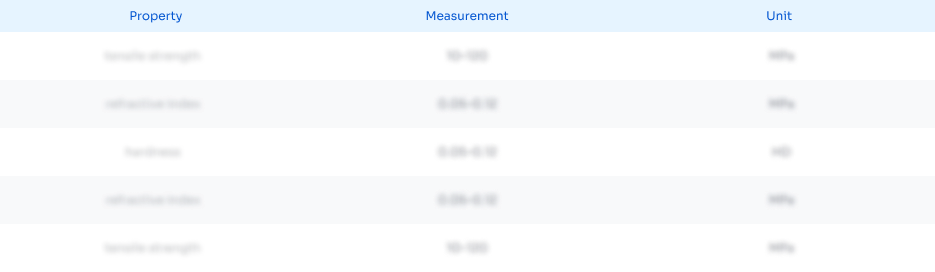
Abstract
Description
Claims
Application Information

- R&D
- Intellectual Property
- Life Sciences
- Materials
- Tech Scout
- Unparalleled Data Quality
- Higher Quality Content
- 60% Fewer Hallucinations
Browse by: Latest US Patents, China's latest patents, Technical Efficacy Thesaurus, Application Domain, Technology Topic, Popular Technical Reports.
© 2025 PatSnap. All rights reserved.Legal|Privacy policy|Modern Slavery Act Transparency Statement|Sitemap|About US| Contact US: help@patsnap.com