Processing method for preparing liquid fuel by performing sludge liquefaction
A process method and liquid fuel technology, applied in the direction of liquid carbon-containing fuels, chemical instruments and methods, fuels, etc., can solve the problems of unspecified water utilization, high heteroatom content in oil products, and adverse environmental effects, etc., to achieve As well as significant environmental and social benefits, excellent product oil quality, and the effect of promoting sludge liquefaction
- Summary
- Abstract
- Description
- Claims
- Application Information
AI Technical Summary
Problems solved by technology
Method used
Image
Examples
Embodiment 1
[0035] Accurately weigh 100g of sludge raw material and 1g of ferrous sulfide catalyst, mix uniformly to form a slurry, add it to the tank reactor, and fill it with sludge raw material (dry basis) mass volume ratio (kg / m 3 ) to 1:2 carbon monoxide gas, raise the reactor temperature to 300°C, and react under this condition for 30 minutes. After the reaction is completed, cool down rapidly, collect the gas and materials in the kettle, and obtain light oil, medium oil, heavy oil, non-condensable gas, water and residue after materials are separated by high temperature, low temperature, solid-liquid, oil-water and distillation.
Embodiment 2
[0037] Accurately take by weighing 100g sludge raw material, 20g embodiment 1 gained aqueous phase and 1g ferrous sulfide catalyst, mix uniformly to form slurry, join in the tank reactor, fill with sludge raw material (dry basis) mass volume ratio ( kg / m 3 ) to 1:2 carbon monoxide gas, raise the reactor temperature to 340°C, and react under this condition for 30min. After the reaction is completed, cool down rapidly, collect the gas and materials in the kettle, and obtain light oil, medium oil, heavy oil, non-condensable gas, water and residue after materials are separated by high temperature, low temperature, solid-liquid, oil-water and distillation.
Embodiment 3
[0039] Accurately weigh 100g of sludge raw material, 20g of wood vinegar and 1g of sodium carbonate catalyst, mix uniformly to form a slurry, add it to the tank reactor, and fill it with sludge raw material (dry basis) mass volume ratio (kg / m3) 1:2 syngas (H 2 :CO=1:1), raise the temperature of the reactor to 360°C, and react under this condition for 30min. After the reaction, cool down rapidly, collect the gas and materials in the kettle, and obtain light oil, medium oil, heavy oil, non-condensable gas, water and residue after high-temperature separation, low-temperature separation, solid-liquid separation, oil-water separation and distillation.
PUM
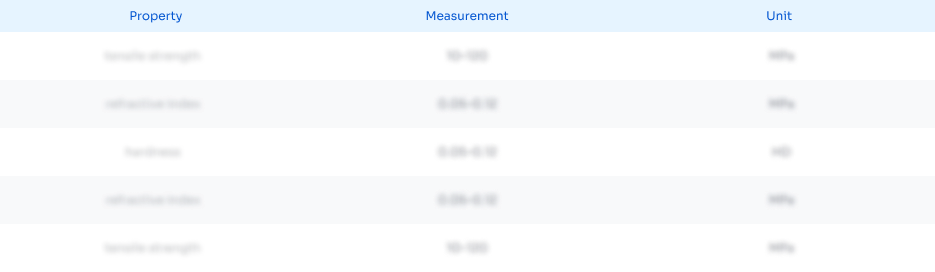
Abstract
Description
Claims
Application Information

- R&D
- Intellectual Property
- Life Sciences
- Materials
- Tech Scout
- Unparalleled Data Quality
- Higher Quality Content
- 60% Fewer Hallucinations
Browse by: Latest US Patents, China's latest patents, Technical Efficacy Thesaurus, Application Domain, Technology Topic, Popular Technical Reports.
© 2025 PatSnap. All rights reserved.Legal|Privacy policy|Modern Slavery Act Transparency Statement|Sitemap|About US| Contact US: help@patsnap.com