Method for compositing iron oxide and graphene by virtue of hydrothermal process
A technology of ferric chloride hexahydrate and graphene, which is applied in the fields of graphene, energy wastewater treatment, light water/sewage treatment, etc., can solve the problems of unremarkable photocatalytic performance, high photogenerated electron-hole recombination rate, and photon quantum efficiency. Low-level problems, to achieve high industrial production value, high utilization rate, and good dispersion
- Summary
- Abstract
- Description
- Claims
- Application Information
AI Technical Summary
Problems solved by technology
Method used
Examples
Embodiment 1
[0023] 1) Weigh 692 mg of ferric chloride hexahydrate and 20 mg of graphene oxide, and dissolve them in 150 mL of deionized water.
[0024] 2) Sonicate the above solution for 1 h.
[0025] 3) Put in the magnetic sub, magnetic stirring for 2h.
[0026] 4) Pour the stirred solution into a high-pressure reactor, put it into an electric heating constant temperature drying oven, and react at a temperature of 200°C for 12 hours.
[0027] 5) After centrifugal washing and vacuum drying, the composite of iron oxide and graphene can be obtained; the mass ratio of iron oxide and graphene in the obtained composite is 16:1, and the iron oxide presents an oblique hexagonal shape with a particle size of about 100nm , which are uniformly dispersed and attached in graphene sheets.
Embodiment 2
[0029] 1) Weigh 346 mg of ferric chloride hexahydrate, 20 mg of graphene oxide, and 10 mg of ammonium dihydrogen phosphate, and dissolve them in 150 mL of deionized water.
[0030] 2) Sonicate the above solution for 1 h.
[0031] 3) Put in the magnetic sub, magnetic stirring for 2h.
[0032] 4) Pour the stirred solution into a high-pressure reactor, put it into an electric heating constant temperature drying oven, and react at a temperature of 200°C for 12 hours.
[0033] 5) After centrifugal washing and vacuum drying, the composite of iron oxide and graphene can be obtained; the mass ratio of iron oxide and graphene in the obtained composite is 8:1, and the iron oxide is in the shape of rice grains with a particle size of about 100nm. Uniformly dispersed and attached to graphene sheets.
Embodiment 3
[0035] 1) Weigh 346 mg of ferric chloride hexahydrate, 20 mg of graphene oxide, and 100 mg of sodium hydroxide, and dissolve them in 150 mL of deionized water.
[0036] 2) Sonicate the above solution for 1 h.
[0037] 3) Put in the magnetic sub, magnetic stirring for 2h.
[0038] 4) Pour the stirred solution into a high-pressure reactor, put it into an electric heating constant temperature drying oven, and react at a temperature of 200°C for 12 hours.
[0039] 5) The composite of iron oxide and graphene can be obtained by centrifugal washing and vacuum drying; the mass ratio of iron oxide and graphene in the obtained composite is 8:1, and the iron oxide is in the shape of a strip with a length of about 150nm, which is uniform dispersed and attached to graphene sheets.
PUM
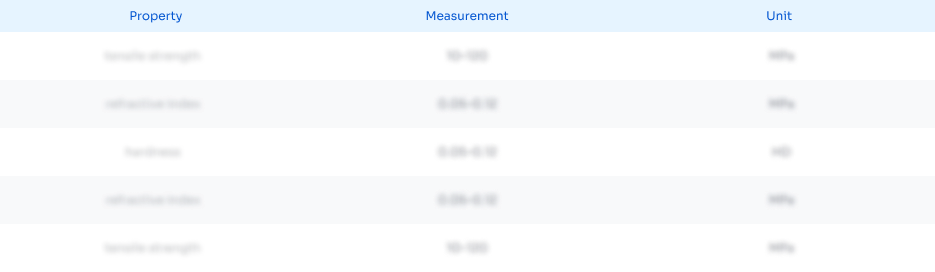
Abstract
Description
Claims
Application Information

- Generate Ideas
- Intellectual Property
- Life Sciences
- Materials
- Tech Scout
- Unparalleled Data Quality
- Higher Quality Content
- 60% Fewer Hallucinations
Browse by: Latest US Patents, China's latest patents, Technical Efficacy Thesaurus, Application Domain, Technology Topic, Popular Technical Reports.
© 2025 PatSnap. All rights reserved.Legal|Privacy policy|Modern Slavery Act Transparency Statement|Sitemap|About US| Contact US: help@patsnap.com