Microwave dielectric ceramic material with medium and high dielectric constants and preparation method thereof
A microwave dielectric ceramic and high dielectric constant technology, applied in the field of dielectric ceramic materials, can solve the problems of inability to meet industrial needs, low resonance frequency quality factor, environmental hazards, etc., achieve stable temperature coefficient, good compactness of finished products, easy obtained effect
- Summary
- Abstract
- Description
- Claims
- Application Information
AI Technical Summary
Problems solved by technology
Method used
Image
Examples
Embodiment 1
[0036] 1) CaCO 3 、TiO 2 Mix at a molar ratio of 1:1, use absolute ethanol as a solvent, and undergo wet ball milling for 4 hours to obtain sample A;
[0037] CaCO 3 , Nb 2 o 5 , Fe 3 o 4 Mixed at a molar ratio of 50:12.5:8.3, using absolute ethanol as a solvent, and subjected to wet ball milling for 4 hours, to obtain sample B; wherein, CaCO 3 、TiO 2 , Nb 2 o 5 and Fe 3 o 4 The purity is greater than 99%;
[0038] 2) Dry sample A and sample B respectively at 80°C, and then pre-fire in air atmosphere at 1100°C for 2 hours to obtain powder A and powder B;
[0039] 3) The powder A and the powder B were wet ball milled for 5 hours and dried to obtain the dried powder A and the dried powder B, and the dried powder A and the dried powder B were mixed in a molar ratio of 90:10, After wet ball milling for 4 hours, mixed powder C was obtained after drying, and an aqueous polyvinyl alcohol solution with a mass concentration of 1% was added as an organic binder to the mixed ...
Embodiment 2
[0043] 1) CaCO 3 、TiO 2 Mix at a molar ratio of 1:1, use absolute ethanol as a solvent, and undergo wet ball milling for 5 hours to obtain sample A;
[0044] CaCO 3 , Nb 2 o 5 , Fe 3 o 4 Mixed at a molar ratio of 50:12.5:8.3, using absolute ethanol as a solvent, and subjected to wet ball milling for 4 hours, to obtain sample B; wherein, CaCO 3 、TiO 2 , Nb 2 o 5 and Fe 3 o 4 The purity is greater than 99%;
[0045] 2) Dry samples A and B at 90°C respectively, and then pre-fire them in an air atmosphere at 1000°C for 5 hours to obtain powder A and powder B;
[0046] 3) The powder A and the powder B were wet ball milled for 6 hours and dried to obtain the dried powder A and the dried powder B, and the dried powder A and the dried powder B were mixed in a molar ratio of 70:30, After wet ball milling for 4 hours, mixed powder C was obtained after drying, and a polyvinyl alcohol aqueous solution with a mass concentration of 5% was added to the mixed powder C, and granul...
Embodiment 3
[0050] 1) CaCO 3 、TiO 2 Mix at a molar ratio of 1:1, use absolute ethanol as a solvent, and undergo wet ball milling for 6 hours to obtain sample A;
[0051] CaCO 3 , Nb 2 o 5 , Fe 3 o 4 Mixed at a molar ratio of 50:12.5:8.3, using absolute ethanol as a solvent, and subjected to wet ball milling for 5 hours to obtain sample B; wherein, CaCO 3 、TiO 2 , Nb 2 o 5 and Fe 3 o 4 The purity is greater than 99%;
[0052] 2) Dry sample A and sample B at 100°C respectively, and then pre-fire them in an air atmosphere at 980°C for 3 hours to obtain powder A and powder B;
[0053] 3) The powder A and the powder B were wet ball milled for 6 hours and dried to obtain the dried powder A and the dried powder B, and the dried powder A and the dried powder B were mixed in a molar ratio of 50:50, After wet ball milling for 5 hours, mixed powder C was obtained after drying, and a polyvinyl alcohol aqueous solution with a mass concentration of 3% was added to the mixed powder C, granu...
PUM
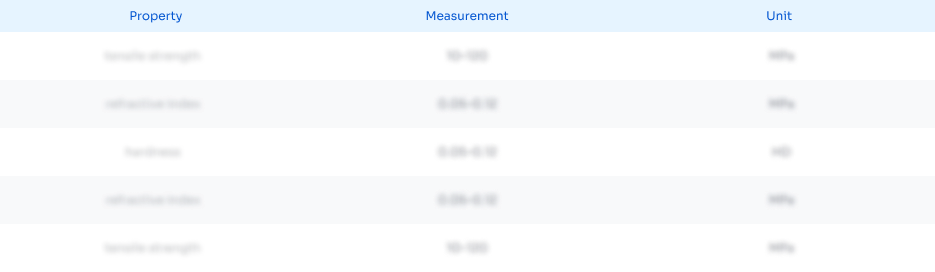
Abstract
Description
Claims
Application Information

- Generate Ideas
- Intellectual Property
- Life Sciences
- Materials
- Tech Scout
- Unparalleled Data Quality
- Higher Quality Content
- 60% Fewer Hallucinations
Browse by: Latest US Patents, China's latest patents, Technical Efficacy Thesaurus, Application Domain, Technology Topic, Popular Technical Reports.
© 2025 PatSnap. All rights reserved.Legal|Privacy policy|Modern Slavery Act Transparency Statement|Sitemap|About US| Contact US: help@patsnap.com