Production technology of fine bronzing plate with high precision and hardness
A production process, bronzing plate technology, applied in metal material coating process, liquid chemical plating, coating and other directions, can solve the problem that the combination of copper plate surface and nickel plating layer cannot be guaranteed, and the plating layer cannot completely cover the plated parts , the reduction of the bonding degree of the coating and other problems, to achieve the effect of reducing the time for plate change and plate installation, reliable and stable hot stamping quality, and high cost performance.
- Summary
- Abstract
- Description
- Claims
- Application Information
AI Technical Summary
Problems solved by technology
Method used
Image
Examples
Embodiment 1
[0035] like figure 1 As shown, a production process of high precision and hardness fine bronzing plate includes the following steps:
[0036] (1), feeding:
[0037] Use H68 type copper block, copper plate thickness: 6.8mm, Vickers hardness: H;
[0038] (2), chemical degreasing:
[0039] Use 80% sodium carbonate solution and 85% sodium silicate solution to spray and wash the incoming materials after picking and rolling, and then use AEO\TX as a 3:4 liquid generator treatment, and a second surface cleaning with sodium citrate, and finally a silicate seal;
[0040] (3), cycle washing:
[0041] Wash with circulating water of sodium hydroxide emulsion for 10 minutes, and then wash with circulating water of sodium borate solution with a concentration of 85% by volume for 15 minutes;
[0042] After circulating water washing, carry out cathode-anode combined electrolytic degreasing and secondary circulating water washing steps, the current density is 5A / dm 2 , the tempera...
Embodiment 2
[0057] like figure 1 As shown, a production process of high precision and hardness fine bronzing plate includes the following steps:
[0058] (1), feeding:
[0059] Use H68 type copper block, copper plate thickness: 6.8mm, Vickers hardness: H;
[0060] (2), chemical degreasing:
[0061] Use 80% sodium carbonate solution and 85% sodium silicate solution to spray and wash the incoming materials after picking and rolling, and then use AEO\TX as a 3:4 liquid generator treatment, and a second surface cleaning with sodium citrate, and finally a silicate seal;
[0062] (3), cycle washing:
[0063] Wash with circulating water of sodium hydroxide emulsion for 15 minutes, and then wash with circulating water of sodium borate solution with a concentration of 85% by volume for 23 minutes;
[0064] After circulating water washing, carry out cathode-anode combined electrolytic degreasing and secondary circulating water washing steps, the current density is 8A / dm 2 , the tempe...
Embodiment 3
[0079] like figure 1 As shown, a production process of high precision and hardness fine bronzing plate includes the following steps:
[0080] (1), feeding:
[0081] Use H68 type copper block, copper plate thickness: 6.8mm, Vickers hardness: H;
[0082] (2), chemical degreasing:
[0083] Use 80% sodium carbonate solution and 85% sodium silicate solution to spray and wash the incoming materials after picking and rolling, and then use AEO\TX as a 3:4 liquid generator treatment, and a second surface cleaning with sodium citrate, and finally a silicate seal;
[0084] (3), cycle washing:
[0085] Wash with circulating water of sodium hydroxide emulsion for 20 minutes, and then wash with circulating water of sodium borate solution with a concentration of 85% by volume for 30 minutes;
[0086] After circulating water washing, carry out cathode-anode combined electrolytic degreasing and secondary circulating water washing steps, the current density is 15A / dm 2 , the temp...
PUM
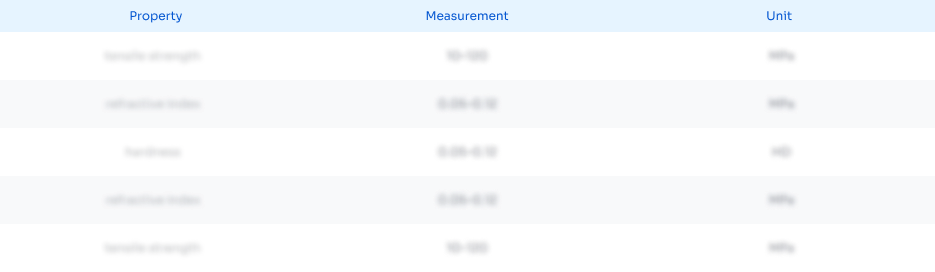
Abstract
Description
Claims
Application Information

- R&D
- Intellectual Property
- Life Sciences
- Materials
- Tech Scout
- Unparalleled Data Quality
- Higher Quality Content
- 60% Fewer Hallucinations
Browse by: Latest US Patents, China's latest patents, Technical Efficacy Thesaurus, Application Domain, Technology Topic, Popular Technical Reports.
© 2025 PatSnap. All rights reserved.Legal|Privacy policy|Modern Slavery Act Transparency Statement|Sitemap|About US| Contact US: help@patsnap.com