Method for producing aluminum oxide by sintering process
A kind of technology of alumina and sintering method, which is applied in the direction of alumina/hydroxide, etc., can solve the problems of unfavorable alumina production cost, enhance market competitiveness, lime highlighting, etc., and achieve the effect of high cost, convenient transportation and less impurities
- Summary
- Abstract
- Description
- Claims
- Application Information
AI Technical Summary
Problems solved by technology
Method used
Examples
Embodiment 1
[0016] 1. Grind calcium carbide slag with a moisture content of 15% and an effective calcium oxide content of 75% with bauxite, anthracite, and alkali powder respectively, and pass through a 100# sieve after grinding.
[0017] 2. Fully mix the ground carbide slag, bauxite, anthracite and alkali powder according to the determined alkali ratio and calcium ratio.
[0018] 3. After the qualified raw meal is sintered at 1180-1220°C for 40 minutes, it is cooled naturally. The cooled clinker is ground and passed through a 60# sieve.
[0019] 4. Grind the clinker according to the determined Al 2 o 3 The dissolution rate was added to the adjustment liquid, stirred and dissolved at 85°C for 30 minutes, and then separated by solid-liquid sedimentation to obtain crude liquid and red mud respectively.
[0020] 5. Add calcium carbide slag milk with solid content ≥ 210g / l and available calcium oxide ≥ 150g / l to the primary desiliconization solution according to the effective calcium oxide...
Embodiment 2
[0022] 1. Grind calcium carbide slag with a moisture content of 15% and an effective calcium oxide content of 65% with bauxite, anthracite, and alkali powder respectively, and pass through a 100# sieve after grinding.
[0023] 2. Fully mix the ground carbide slag, bauxite, anthracite and alkali powder according to the determined alkali ratio and calcium ratio.
[0024] 3. After the qualified raw meal is sintered at 1180-1220°C for 40 minutes, it is cooled naturally. The cooled clinker is ground and passed through a 60# sieve.
[0025] 4. Grind the clinker according to the determined Al 2 o 3 The dissolution rate was added to the adjustment liquid, stirred and dissolved at 85°C for 30 minutes, and then separated by solid-liquid sedimentation to obtain crude liquid and red mud respectively.
[0026] 5. Add calcium carbide slag milk with solid content ≥ 210g / l and available calcium oxide ≥ 150g / l to the primary desiliconization solution according to the effective calcium oxide...
Embodiment 3
[0028] 1. Grind calcium carbide slag with a moisture content of 40% and an effective calcium oxide content of 65% with bauxite, anthracite, and alkali powder respectively, and pass through a 100# sieve after grinding.
[0029] 2. Fully mix the ground carbide slag, bauxite, anthracite and alkali powder according to the determined alkali ratio and calcium ratio.
[0030] 3. After the qualified raw meal is sintered at 1180-1220°C for 40 minutes, it is cooled naturally. The cooled clinker is ground and passed through a 60# sieve.
[0031] 4. Grind the clinker according to the determined Al 2 o 3 The dissolution rate was added to the adjustment liquid, stirred and dissolved at 85°C for 30 minutes, and then separated by solid-liquid sedimentation to obtain crude liquid and red mud respectively.
[0032] 5. Add calcium carbide slag milk with solid content ≥ 210g / l and available calcium oxide ≥ 150g / l to the primary desiliconization solution according to the effective calcium oxide...
PUM
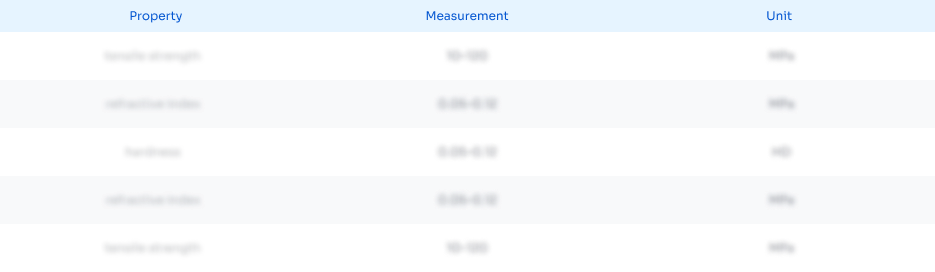
Abstract
Description
Claims
Application Information

- R&D
- Intellectual Property
- Life Sciences
- Materials
- Tech Scout
- Unparalleled Data Quality
- Higher Quality Content
- 60% Fewer Hallucinations
Browse by: Latest US Patents, China's latest patents, Technical Efficacy Thesaurus, Application Domain, Technology Topic, Popular Technical Reports.
© 2025 PatSnap. All rights reserved.Legal|Privacy policy|Modern Slavery Act Transparency Statement|Sitemap|About US| Contact US: help@patsnap.com