Sand carving processing method of precision screen printing plate
A processing method and screen technology, applied in the directions of printing plates, printing plate preparation, printing, etc., can solve the problems of pinhole leakage, poor image restoration, and shortened screen printing life, so as to reduce scattering and reflection phenomena, improve The effect of transferring amount and increasing adhesion
- Summary
- Abstract
- Description
- Claims
- Application Information
AI Technical Summary
Problems solved by technology
Method used
Examples
Embodiment 1
[0016] The invention provides a precision screen sand engraving processing method, comprising the steps of:
[0017] 1. Stretching net: Paste the metal wire mesh on the screen frame tightly to form a screen version. The metal wire mesh is suitable for any weaving mesh, any weaving method, and any metal material with any profile characteristics. It is stainless steel wire mesh, Stainless steel sheet, electroformed mesh, alloy wire mesh and other metal mesh yarns;
[0018] 2. Sand carving treatment:
[0019] (1) Put the stretched wire mesh into the sand engraving equipment, add 1200 mesh corundum into the sand engraving equipment, and cover the non-sandblasting area of the screen with a cover cloth;
[0020] (2) The pressure of the sand engraving equipment is set to 0.35 MPa, the emery is sprayed out, and the surface of the wire mesh of the screen is sprayed for 60 seconds to obtain a sand engraved screen;
[0021] 3. Degreasing: Degrease the sand-cut screen to remove ...
Embodiment 2
[0026] The present invention provides a precision screen sand engraving processing method, the rest of the steps are similar to Embodiment 1, and the sand engraving processing steps are:
[0027] (1) Put the stretched wire mesh into the sand engraving equipment, add 600 mesh silica particles into the sand engraving equipment, and cover the non-sandblasting area of the screen with a plastic film;
[0028] (2) The pressure of the sand engraving equipment is set to 0.25 MPa, the silicon dioxide particles are sprayed out, and the surface of the wire mesh of the screen is sprayed for 114 seconds to obtain a sand engraved mesh. Version.
[0029] The precision screen sand engraving treatment method disclosed by the present invention can roughen the surface of the metal screen, increase the adhesion of the screen surface, and ensure better contact between the screen and the photosensitive layer in the subsequent coating process. The surface of the screen is sand-cut to form uniform...
PUM
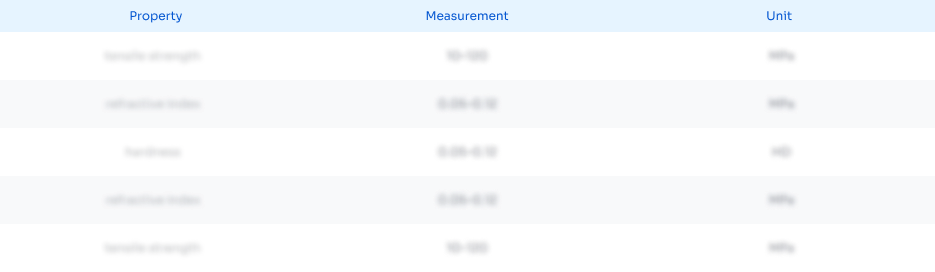
Abstract
Description
Claims
Application Information

- Generate Ideas
- Intellectual Property
- Life Sciences
- Materials
- Tech Scout
- Unparalleled Data Quality
- Higher Quality Content
- 60% Fewer Hallucinations
Browse by: Latest US Patents, China's latest patents, Technical Efficacy Thesaurus, Application Domain, Technology Topic, Popular Technical Reports.
© 2025 PatSnap. All rights reserved.Legal|Privacy policy|Modern Slavery Act Transparency Statement|Sitemap|About US| Contact US: help@patsnap.com