Method for preparing corrosion-resistant antibacterial polyurea composite coating
A composite coating and nano-composite coating technology, applied in the fields of botanical equipment and methods, coatings, anti-corrosion coatings, etc., can solve the problems of weakening the service life of coatings, transfer of heavy metal ions, and fragile mesoporous materials. The effect of extending service life, improving hardness and abrasion resistance, and improving antibacterial ability
- Summary
- Abstract
- Description
- Claims
- Application Information
AI Technical Summary
Problems solved by technology
Method used
Examples
Embodiment 1
[0019] Preparation of component A: Put 450g of polyoxypropylene ether polyol (average functionality fn=3, relative average molecular weight Wn=5000) into the reactor, heat it up to 100°C, dehydrate under reduced pressure for 1 hour, then cool down to 78°C, Add 550g of diphenylmethane diisocyanate (MDI 100, purity greater than 98%), keep the temperature at 80°C, and react for 2h. This results in an isocyanate-terminated prepolymer, Part A.
[0020] Among them, isocyanates include PAPI (multiple tetramethyl polyphenyl polyisocyanate), liquefied MDI (diphenylmethane diisocyanate), HDI (hexamethylene diisocyanate), IPDI (isophorone diisocyanate) and terminal isocyanate prepolymer.
[0021] Preparation of antibacterial nanopowder: Add 500ml 0.1mol / l CuCl to 100ml HCl (6mol / L) solution 2 Solution and 0.055 mol of copper powder, heated and stirred until the copper powder in the solution reacted completely, cooled to 25°C, adjusted the pH value of the solution to 2.5 with NaOH, adde...
Embodiment 2
[0025] Preparation of component A: Put 450g of polyoxypropylene ether polyol (average functionality fn=3, relative average molecular weight Wn=5000) into the reactor, heat it up to 95°C, dehydrate under reduced pressure for 1.5h, and then cool down to 80°C Next, add 550 g of isophorone diisocyanate (IPDI), keep the temperature at 75° C., and react for 3 hours. This results in an isocyanate-terminated prepolymer, the A component.
[0026] Add 500ml 0.5mol / l CuCl to 100ml HCl (6mol / L) solution 2 solution and 0.25 mol of copper powder, heated and stirred until the copper powder in the solution reacted completely, cooled to 25°C, adjusted the pH value of the solution to 2 with NaOH, added 10 g of surfactant (polyethylene glycol 400), and dissolved in ice water Add 100 ml of 0.5 mol / L NaSCN solution drop by drop under the condition of cooling and constant stirring (dropping speed is 30 drops per minute), after aging, washing, filtering and constant temperature drying at 110°C, nan...
Embodiment 3
[0030] Preparation of component A: Put 350g of polyoxypropylene ether polyol (average functionality fn=3, relative average molecular weight Wn=5000) into the reactor, heat it up to 97°C, dehydrate under reduced pressure for 1.2h, and then cool down to 50°C , add 650g of hexamethylene diisocyanate (HDI), keep the temperature at 85°C, and react for 2.5h. This results in an isocyanate-terminated prepolymer, the A component.
[0031] Add 500ml 0.25mol / l CuCl to 100ml HCl (6mol / L) solution 2 solution and 0.125 mol of copper powder, heated and stirred until the copper powder in the solution reacted completely, cooled to 25°C, adjusted the pH value of the solution to 3 with NaOH, added 8 g of surfactant (polyethylene glycol 400), and dissolved in ice water Add 100 ml of 0.5 mol / L NaSCN solution drop by drop under the condition of cooling and constant stirring (dropping speed is 30 drops per minute), after aging, washing, filtering and constant temperature drying at 110°C, nanometer ...
PUM
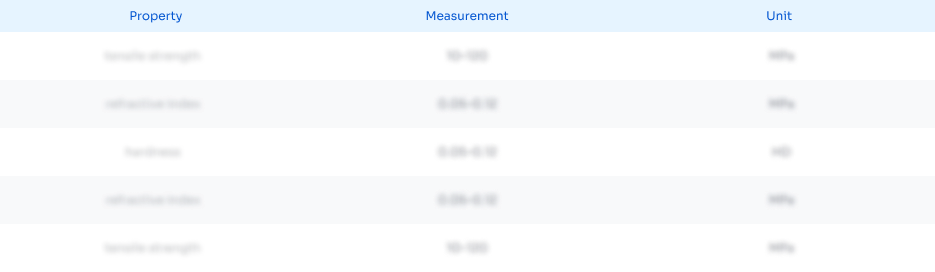
Abstract
Description
Claims
Application Information

- Generate Ideas
- Intellectual Property
- Life Sciences
- Materials
- Tech Scout
- Unparalleled Data Quality
- Higher Quality Content
- 60% Fewer Hallucinations
Browse by: Latest US Patents, China's latest patents, Technical Efficacy Thesaurus, Application Domain, Technology Topic, Popular Technical Reports.
© 2025 PatSnap. All rights reserved.Legal|Privacy policy|Modern Slavery Act Transparency Statement|Sitemap|About US| Contact US: help@patsnap.com