Graphite carbon sleeve gradient anti-oxidation coating and preparation method thereof
A gradient coating and graphite carbon technology, which is applied in the field of preparation of graphite anti-oxidation composite coatings, can solve the problems of ineffective formation of gradient coatings, no specific data given, low oxidation resistance temperature, etc., and achieve graphite carbon coatings The gradient anti-oxidation coating is uniform and dense, the impregnation efficiency is improved, and the bonding strength is good
- Summary
- Abstract
- Description
- Claims
- Application Information
AI Technical Summary
Problems solved by technology
Method used
Image
Examples
Embodiment 1
[0031] 1) Pretreatment of the graphite carbon sleeve: surface grinding and polishing of the graphite carbon sleeve, then cleaning, and drying in an oven;
[0032] 2) Take aluminum-containing polycarbosilane (PACS), dissolve it in xylene, heat and stir at 70°C to prepare a 40wt.% PACS xylene solution;
[0033] 3) Place the graphite sample block in the dipping tank, vacuumize it to -0.1MPa, inject the above-mentioned solution with a concentration of 40wt.% into the tank, keep the vacuum state and soak for 5 minutes, then apply a high pressure of 2MPa and soak for 2 hours, then from the dipping Take out the graphite carbon sleeve from the tank and dry it at 200°C for 4 hours;
[0034] 4) Put the dried graphite carbon jacket into the atmosphere furnace, pass in argon as a protective gas, then control the temperature rise rate of the atmosphere furnace to 0.1°C / min to 650°C for 2 hours, and then set the temperature at 2°C / min Heat up to 1400°C for 2 hours, then cool down to room t...
Embodiment 2
[0036] The pretreatment of graphite carbon sleeve and the preparation of impregnation solution are the same as in Example 1, and the impregnation, drying, high-temperature treatment, vacuum degree, and impregnation pressure (2MPa) are also the same; the concentration of impregnation solution is changed to: 60wt.%, the number of times of impregnation and cracking Change to 3 times, and the 3 times of dipping and cracking processes are all corresponding to Example 1; after 3 dips and cracks, the SiC gradient protective coating of the graphite carbon sleeve is obtained, that is, the graphite carbon sleeve anti-oxidation gradient coating. The prepared gradient coating can protect the graphite material in static air at 1100°C for 1000 hours, has an oxidation weight loss of 0.52wt.%, and can withstand 100 thermal shocks at 1100°C without falling off.
Embodiment 3
[0038] The pretreatment of graphite carbon sleeve and the preparation of impregnation solution are the same as in Example 1, and the impregnation, drying, high-temperature treatment and vacuum degree are also the same; the concentration of the impregnation solution is changed to 60wt.%, the impregnation pressure is changed to 5MPa, and the number of times of impregnation and cracking is changed to 3 times, and the 3 times of immersion and cracking processes are all corresponding to Example 1; after 3 times of immersion and cracking, the SiC gradient protective coating of the graphite carbon sleeve is obtained. The prepared gradient coating can protect the graphite material in static air at 1100°C for 1000 hours, has an oxidation weight loss of 0.50wt.%, and is resistant to thermal shocks at 1100°C for 100 times without falling off.
[0039] The resulting graphitic carbon sleeve (ARLX'TRA type) X-ray diffractometer analysis sample with SiC gradient protective coating, that is, g...
PUM
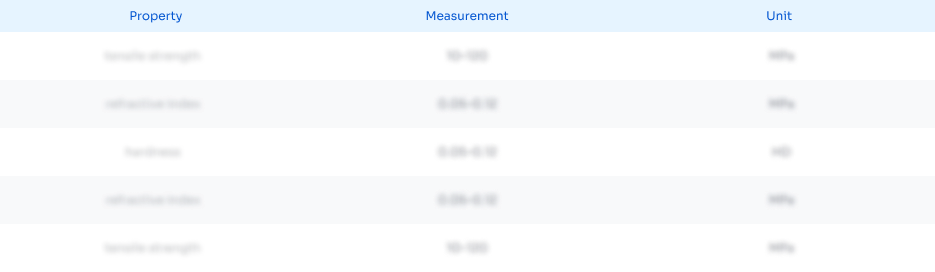
Abstract
Description
Claims
Application Information

- R&D
- Intellectual Property
- Life Sciences
- Materials
- Tech Scout
- Unparalleled Data Quality
- Higher Quality Content
- 60% Fewer Hallucinations
Browse by: Latest US Patents, China's latest patents, Technical Efficacy Thesaurus, Application Domain, Technology Topic, Popular Technical Reports.
© 2025 PatSnap. All rights reserved.Legal|Privacy policy|Modern Slavery Act Transparency Statement|Sitemap|About US| Contact US: help@patsnap.com