Roughness-controllable polishing method for stereolithographic resin prototype models
A technology of light curing and roughness, applied in polishing compositions containing abrasives, etc., can solve the problems of long processing cycle, high labor intensity, low efficiency, etc., and achieve the effect of improving surface accuracy
- Summary
- Abstract
- Description
- Claims
- Application Information
AI Technical Summary
Problems solved by technology
Method used
Image
Examples
Embodiment 1
[0028] A method for polishing a light-cured molding resin prototype with controllable roughness, specifically comprising the following operations:
[0029] (1) Use a light-curing molding machine to make a light-curing molding resin prototype;
[0030] (2) Preparation of chemical corrosion abrasive flow fluid by dispersion method:
[0031] Firstly, 12% PH regulator, 12% alcohol and deionized water are prepared as a mixed liquid, wherein the PH regulator is potassium hydroxide, and the alcohol is methanol; when adding abrasive grains, the dispersion method is used, and the abrasive powder is mixed by mechanical stirring and ultrasonic vibration. Directly disperse into water to prepare abrasive corrosion abrasive flow fluid: (a) abrasive particles are wetted in the mixed liquid; (b) aggregates are opened into independent primary particles or relatively small particles under the action of mechanical stirring force and ultrasonic vibration. Small aggregates; (c) Add 0.3% to 0.6% o...
Embodiment 2
[0036] A method for polishing a light-cured molding resin prototype with controllable roughness, specifically comprising the following operations:
[0037] (1) Use a light-curing molding machine to make a light-curing molding resin prototype;
[0038] (2) Preparation of chemical corrosion abrasive flow fluid by dispersion method:
[0039] Firstly, 13.5% PH regulator, 15% alcohol and deionized water are prepared as a mixed liquid, wherein the PH regulator is sodium hydroxide, and the alcohol is ethanol; when adding abrasive grains, the dispersion method is used, and the abrasive powder is mixed by mechanical stirring and ultrasonic vibration. Directly disperse into water to prepare abrasive corrosion abrasive flow fluid: (a) abrasive particles are wetted in the mixed liquid; (b) aggregates are opened into independent primary particles or relatively small particles under the action of mechanical stirring force and ultrasonic vibration. Small aggregates; (c) Add 0.5% to 0.6% sod...
Embodiment 3
[0044] A method for polishing a light-cured molding resin prototype with controllable roughness, specifically comprising the following operations:
[0045] (1) Use a light-curing molding machine to make a light-curing molding resin prototype;
[0046] (2) Preparation of chemical corrosion abrasive flow fluid by dispersion method:
[0047] Firstly, 15% of PH adjuster, 13.5% of alcohol and deionized water are prepared as a mixed liquid, wherein the pH adjuster is sodium hydroxide, and the alcohol is ethylene glycol; when adding abrasive grains, the dispersion method is adopted, and the mixture is mixed by mechanical stirring and ultrasonic vibration. Abrasive powder is directly dispersed into water to prepare abrasive corrosion abrasive flow fluid: (a) abrasive particles are wetted in the mixed liquid; (b) agglomerates are broken into independent primary particles under the action of mechanical stirring force and ultrasonic vibration Or smaller aggregates; (c) Add 0.5% to 0.6% ...
PUM
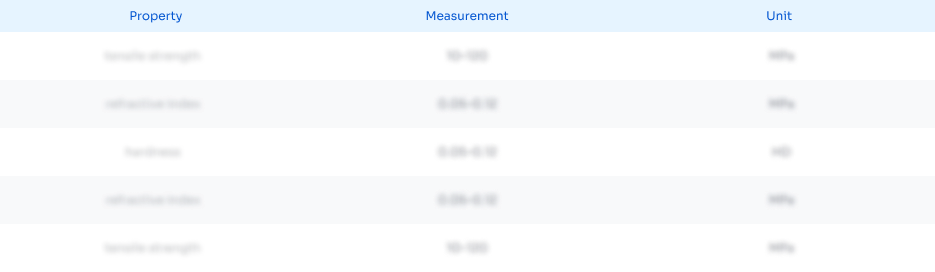
Abstract
Description
Claims
Application Information

- R&D
- Intellectual Property
- Life Sciences
- Materials
- Tech Scout
- Unparalleled Data Quality
- Higher Quality Content
- 60% Fewer Hallucinations
Browse by: Latest US Patents, China's latest patents, Technical Efficacy Thesaurus, Application Domain, Technology Topic, Popular Technical Reports.
© 2025 PatSnap. All rights reserved.Legal|Privacy policy|Modern Slavery Act Transparency Statement|Sitemap|About US| Contact US: help@patsnap.com