Method for extracting aluminum oxides from aluminum-containing waste residues
An alumina and aluminum waste slag technology, applied in the removal of alumina/aluminum hydroxide, solid waste, etc., can solve the problems of difficult operation, limited utilization, fly ash pollution, etc., and achieve efficient resource utilization methods and products. The effect of high purity and low iron content
- Summary
- Abstract
- Description
- Claims
- Application Information
AI Technical Summary
Problems solved by technology
Method used
Examples
Embodiment 1
[0020] (1) Ingredients: Take 100g of coal gangue with an alumina content of 22.9%, a silica content of 41.1%, and add 175g of red coal gangue with an alumina content of 23.4%, a silica content of 19.1%, and a sodium oxide content of 9.4%. Mud and 38g sodium carbonate, mix thoroughly, the molar ratio of Na, Al, Si in the ingredients is about 1:1:1;
[0021] (2) Sintering: Sinter the ingredients at 800°C to obtain 261g of sintered clinker;
[0022] (3) Acid leaching: 850ml of hydrochloric acid solution with a mass concentration of 21% was reacted with sintered clinker at 100°C, solid-liquid separation, washing, and fixed volume to obtain 1200ml of aluminum salt solution containing aluminum chloride;
[0023] (4) Concentrated crystallization: Concentrate the aluminum salt solution until white crystals are precipitated to obtain 487ml of concentrated solution, then add 1220ml of concentrated hydrochloric acid with a mass concentration of 36% to the concentrated solution, stir, let...
Embodiment 2
[0026] (1) Ingredients: Take 100g of coal-fired fly ash with an alumina content of 35.3%, a silica content of 50.9%, and add 110g of an alumina content of 23.4%, a silica content of 19.1%, and a sodium oxide content of 9.4%. The red mud and 52g of sodium carbonate are fully mixed, and the molar ratio of Na, Al, and Si in the ingredients is about 1.1:1:1;
[0027] (2) Sintering: Sinter the ingredients at 850°C to obtain 232g of sintered clinker;
[0028] (3) Acid leaching: 900ml of hydrochloric acid solution with a mass concentration of 19% was reacted with sintered clinker at 100°C, solid-liquid separation, washing, and fixed volume to obtain 1200ml of aluminum salt solution containing aluminum chloride;
[0029] (4) Concentrated crystallization: Concentrate the aluminum salt solution until white crystals are precipitated to obtain 476ml of concentrated solution, then add 1200ml of concentrated hydrochloric acid with a mass concentration of 36% to the concentrated solution, st...
Embodiment 3
[0032] (1) Ingredients: Take 100g of boiler slag with an alumina content of 32.7%, a silica content of 45.3%, and add 80g of red slag with an alumina content of 23.4%, a silica content of 19.1%, and a sodium oxide content of 9.4%. Mud and 35g sodium carbonate, mix thoroughly, the molar ratio of Na, Al, Si in the ingredients is about 0.9:1:1;
[0033] (2) Sintering: Sinter the ingredients at 900°C to obtain 193g of sintered clinker;
[0034] (3) Acid leaching: 800ml of hydrochloric acid solution with a mass concentration of 22% was reacted with sintered clinker at 100°C, solid-liquid separation, washing, and fixed volume to obtain 1200ml of aluminum salt solution containing aluminum chloride;
[0035] (4) Concentrated crystallization: Concentrate the aluminum salt solution until white crystals are precipitated to obtain 459ml of concentrated solution, then add 1100ml of concentrated hydrochloric acid with a mass concentration of 34% to the concentrated solution, stir, let stand...
PUM
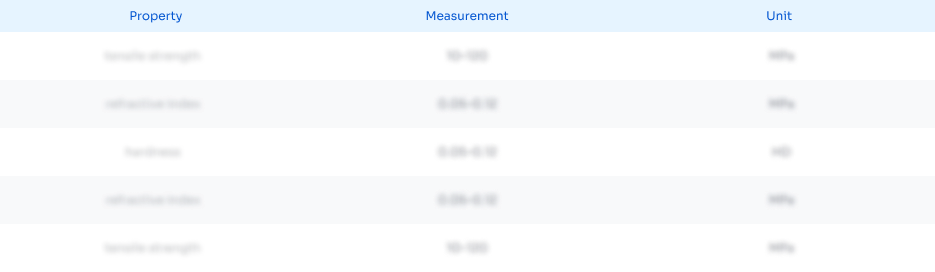
Abstract
Description
Claims
Application Information

- R&D
- Intellectual Property
- Life Sciences
- Materials
- Tech Scout
- Unparalleled Data Quality
- Higher Quality Content
- 60% Fewer Hallucinations
Browse by: Latest US Patents, China's latest patents, Technical Efficacy Thesaurus, Application Domain, Technology Topic, Popular Technical Reports.
© 2025 PatSnap. All rights reserved.Legal|Privacy policy|Modern Slavery Act Transparency Statement|Sitemap|About US| Contact US: help@patsnap.com