Novel hot extrusion tee joint forming process
A molding process and extrusion molding technology, applied in metal rolling and other directions, can solve the problems of complex manufacturing procedures, waste of time, waste of resources, etc., and achieve the effects of shortening the production cycle, saving fuel resources, and saving repeated heating.
- Summary
- Abstract
- Description
- Claims
- Application Information
AI Technical Summary
Problems solved by technology
Method used
Image
Examples
Embodiment Construction
[0037] In order to make the technical problems, technical solutions and beneficial effects solved by the present invention clearer, the present invention will be further described in detail below in conjunction with the accompanying drawings and embodiments. It should be understood that the specific embodiments described here are only used to explain the present invention, not to limit the present invention.
[0038] Such as figure 2 A new type of hot extrusion tee forming process shown includes the following steps:
[0039] The first step, steel plate rolling: roll the sheet steel plate into a shaped steel plate with a designed thickness, and the shaped steel plate is divided into three areas arranged in parallel: the end area, the middle area and the tail area according to the thickness, wherein the end area The wall thickness of the region and the tail region is the same; the wall thickness of the middle region is greater than the wall thickness of the end region and the ...
PUM
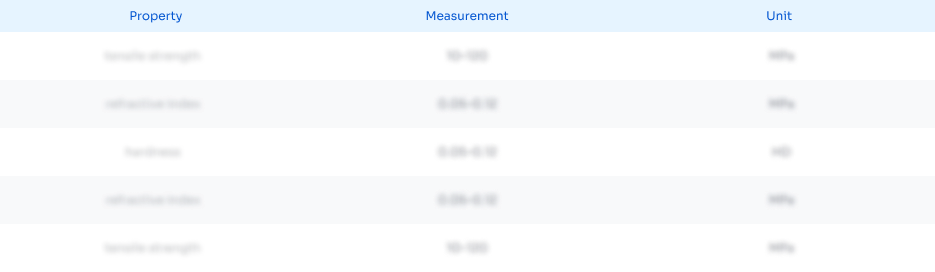
Abstract
Description
Claims
Application Information

- R&D Engineer
- R&D Manager
- IP Professional
- Industry Leading Data Capabilities
- Powerful AI technology
- Patent DNA Extraction
Browse by: Latest US Patents, China's latest patents, Technical Efficacy Thesaurus, Application Domain, Technology Topic, Popular Technical Reports.
© 2024 PatSnap. All rights reserved.Legal|Privacy policy|Modern Slavery Act Transparency Statement|Sitemap|About US| Contact US: help@patsnap.com