brake pads
A technology of brake pads and friction materials, applied in the field of brake pads, can solve problems such as non-wear resistance, harsh noise, hidden dangers, etc., and achieve the effects of good thermal conductivity, good heat dissipation performance, and improved wear resistance
- Summary
- Abstract
- Description
- Claims
- Application Information
AI Technical Summary
Problems solved by technology
Method used
Image
Examples
Embodiment 1
[0022] The preparation method of the brake pad is obtained according to the conventional preparation method. The process is: raw material mixing - raw material kneading - kneading - pressing - vulcanization, curing - grinding - finished product, the specific process is as follows:
[0023] (1) Mixing of raw materials: According to the formula ratio, graphite (chemically treated graphite), bauxite, feldspar powder, fluorite powder, and silicon carbide are mixed evenly;
[0024] (2) Kneading of raw materials: adding the remaining raw materials of the formula ratio to the mixture of step (1) and kneading;
[0025] (5) Mixing: Mix the above-mentioned kneaded raw materials at a temperature of 250-350°C for 10-50 minutes;
[0026] (6) The kneaded mixture obtained in step (3) is hot-pressed in a mould, and the control pressure is 50-100MPa (500-1000kg / cm 2 ), the hot pressing time is 4 to 6 minutes;
[0027] (4) Vulcanize the press-molded article in step (4) at a temperature of 150...
PUM
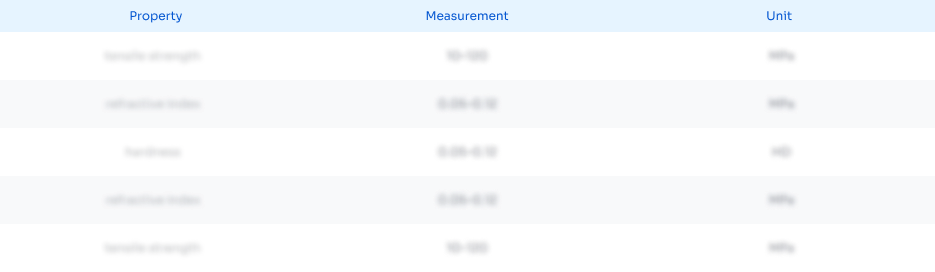
Abstract
Description
Claims
Application Information

- R&D
- Intellectual Property
- Life Sciences
- Materials
- Tech Scout
- Unparalleled Data Quality
- Higher Quality Content
- 60% Fewer Hallucinations
Browse by: Latest US Patents, China's latest patents, Technical Efficacy Thesaurus, Application Domain, Technology Topic, Popular Technical Reports.
© 2025 PatSnap. All rights reserved.Legal|Privacy policy|Modern Slavery Act Transparency Statement|Sitemap|About US| Contact US: help@patsnap.com