Method for manufacturing glass ceramic plate used for architectural decoration by utilizing coal gangue
A technology for glass-ceramic and architectural decoration, which is applied in the field of preparing glass-ceramic plates for building decoration, can solve the problems of high unit price of oxide colorants, high proportion of oxide colorants, and high cost of chemical raw materials, and achieves easy quality control. , The effect of reducing the stockpile, strong stability and controllability
- Summary
- Abstract
- Description
- Claims
- Application Information
AI Technical Summary
Problems solved by technology
Method used
Image
Examples
Embodiment 1
[0023] The glass formula is made by weighing and mixing. The composition of the glass formula is calculated in parts by weight: 60 parts of coal gangue after pretreatment (the coal gangue is crushed to below 40 mesh and pre-homogenized), 18 parts of quartz sand, and 13 parts of calcite. 2.5 parts of sodium carbonate, 2 parts of zinc oxide, 4.3 parts of barium carbonate, 0.2 parts of dicobalt trioxide
[0024] Put the above-mentioned glass formulation in a mullite crucible, melt it in a box-type electric furnace at a temperature of 1470°C for 2.5 hours, and keep it warm for 4 hours. After the heat preservation is completed, pour the glass liquid into water to become glass pellets; after drying , Sieve the glass frit with particle size between 2-5mm.
[0025] 400 grams of glass granules were spread in a batch in a refractory mold with a size of 300×250 mm and crystallized in a box-type electric furnace, and the crystallization temperature was 1050° C. Keep warm at the crystalli...
Embodiment 2
[0027] The glass formula is made by weighing and mixing. The composition of the glass formula is calculated in parts by weight: 50 parts of coal gangue after pretreatment (the coal gangue is crushed to below 40 mesh and pre-homogenized), 25 parts of quartz sand, and 14 parts of calcite. 3 parts of sodium carbonate, 2.9 parts of zinc oxide, 5 parts of barium carbonate, 1 part of borax, and 0.1 part of nickelous oxide.
[0028] Melt the above-mentioned glass formula material in a glass tank kiln with a temperature of 1470°C for 2.5 hours, and keep it warm for 4 hours. After the heat preservation is completed, the glass liquid is directly poured into water to become glass granules; after drying and sieving, the particle size is 2- Frit between 5mm.
[0029] 400 grams of glass granules are tiled in a refractory mold with a size of 300×250 mm and crystallized in a box-type electric furnace, and the crystallization temperature is 1050° C. Keep warm at the crystallization temperatur...
Embodiment 3
[0031] The glass formula is made by weighing and mixing. The composition of the glass formula is calculated in parts by weight: 50 parts of coal gangue after pretreatment (the coal gangue is crushed to below 40 mesh and pre-homogenized), 24 parts of quartz sand, and 13 parts of calcite. 3 parts of sodium carbonate, 3 parts of zinc oxide, 5 parts of barium carbonate, 1.5 parts of borax, and 0.5 parts of copper oxide.
[0032] Melt the above-mentioned glass formula material in a glass tank kiln with a temperature of 1470°C for 2.5 hours, and keep it warm for 4 hours. After the heat preservation is completed, the glass liquid is directly poured into water to become glass granules; after drying and sieving, the particle size is 2- Frit between 5mm.
[0033] 400 grams of glass granules are tiled in a refractory mold with a size of 300×250 mm and crystallized in a box-type electric furnace, and the crystallization temperature is 1050° C. Keep warm at the crystallization temperature...
PUM
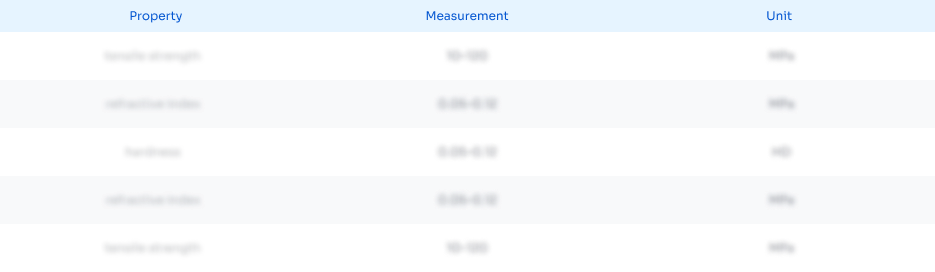
Abstract
Description
Claims
Application Information

- R&D
- Intellectual Property
- Life Sciences
- Materials
- Tech Scout
- Unparalleled Data Quality
- Higher Quality Content
- 60% Fewer Hallucinations
Browse by: Latest US Patents, China's latest patents, Technical Efficacy Thesaurus, Application Domain, Technology Topic, Popular Technical Reports.
© 2025 PatSnap. All rights reserved.Legal|Privacy policy|Modern Slavery Act Transparency Statement|Sitemap|About US| Contact US: help@patsnap.com