Vanadium-containing high-boron high-chromium wear-resistant alloy and preparation method thereof
A wear-resistant alloy and high-boron technology, applied in the field of metal wear-resistant materials, can solve the problems of increasing the production cost of high-chromium cast iron, etc., and achieve the effects of short heat treatment cycle, good impact toughness, good oxidation resistance and corrosion resistance
- Summary
- Abstract
- Description
- Claims
- Application Information
AI Technical Summary
Problems solved by technology
Method used
Image
Examples
Embodiment 1
[0036] (1) Melt scrap steel and ferrochrome in an intermediate frequency induction furnace, add nickel plate, ferrosilicon and ferromanganese after molten steel is melted;
[0037] (2) When the temperature of the molten steel rises to 1550~1600°C, add 0.1% of the molten steel mass for aluminum deoxidation, and then add ferrovanadium, ferrotitanium and ferroboron in sequence;
[0038] (3) After the composition is adjusted in front of the furnace, when the temperature reaches 1430~1480°C, pour molten steel into the sand mold;
[0039] (4) After the casting is polished and cleaned, it is subjected to stress relief treatment, heated to 350°C with the furnace, kept for 6 hours, and then air-cooled or furnace air-cooled to room temperature to obtain a vanadium-containing, high-boron, high-chromium wear-resistant alloy. The chemical composition of the alloy is shown in Table 1, and the mechanical properties and wear resistance are shown in Table 2. The wear test was carried out on a...
Embodiment 2
[0041] (1) Melt scrap steel and ferrochrome in an intermediate frequency induction furnace, add nickel plate, ferrosilicon and ferromanganese after molten steel is melted;
[0042] (2) When the temperature of the molten steel rises to 1550~1600°C, add 0.1% of the molten steel mass for aluminum deoxidation, and then add ferrovanadium, ferrotitanium and ferroboron in sequence;
[0043] (3) After the composition is adjusted in front of the furnace, when the temperature reaches 1430~1480°C, pour molten steel into the sand mold;
[0044] (4) After the casting is polished and cleaned, the casting is heated to 1050°C with the furnace, kept for 4 hours, then air-cooled to room temperature, and finally tempered at 200°C for 4 hours. The chemical composition of the alloy is shown in Table 1, the mechanical properties and wear resistance are shown in Table 2, and the wear test is the same as in Example 1.
Embodiment 3
[0046] (1) Melt scrap steel and ferrochrome in an intermediate frequency induction furnace, add nickel plate, ferrosilicon and ferromanganese after molten steel is melted;
[0047] (2) When the temperature of the molten steel rises to 1550~1600°C, add 0.1% of the molten steel mass for aluminum deoxidation, and then add ferrovanadium, ferrotitanium and ferroboron in sequence;
[0048] (3) After the composition is adjusted in front of the furnace, when the temperature reaches 1430~1480°C, pour molten steel into the sand mold;
[0049] (4) After the casting is polished and cleaned, heat the casting to 1100°C with the furnace, keep it warm for 2 hours, then air-cool to room temperature, and finally temper at 350°C for 2 hours. The chemical composition of the alloy is shown in Table 1, the mechanical properties and wear resistance are shown in Table 2, and the wear test is the same as in Example 1.
PUM
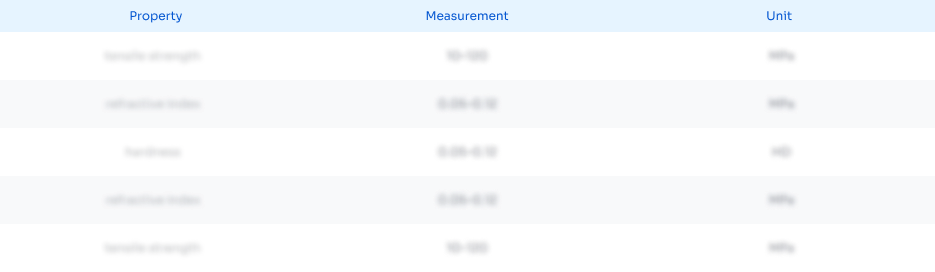
Abstract
Description
Claims
Application Information

- R&D Engineer
- R&D Manager
- IP Professional
- Industry Leading Data Capabilities
- Powerful AI technology
- Patent DNA Extraction
Browse by: Latest US Patents, China's latest patents, Technical Efficacy Thesaurus, Application Domain, Technology Topic, Popular Technical Reports.
© 2024 PatSnap. All rights reserved.Legal|Privacy policy|Modern Slavery Act Transparency Statement|Sitemap|About US| Contact US: help@patsnap.com