Method for producing high-purity lithium carbonate by using lithium concentrate
A high-purity lithium carbonate and lithium concentrate technology, applied in chemical instruments and methods, lithium compounds, alkali metal compounds, etc., can solve the problem of high steam consumption, high consumption of sodium carbonate, large amount of lithium hydroxide, large amount of waste water, etc. problems, to achieve the effect of saving steam energy consumption, simple process and high recovery rate
- Summary
- Abstract
- Description
- Claims
- Application Information
AI Technical Summary
Problems solved by technology
Method used
Examples
Embodiment 1
[0024] Take 2 tons of lithium concentrate with a lithium oxide content of 6%. First, it is calcined at 1000°C in a rotary kiln and transformed into a baked material. The baked material is cooled to 145°C by a cooler and then ball milled to a particle size of 95% by a ball mill. less than 80 mesh, then mix the baked material with 500 kg of concentrated sulfuric acid through a screw conveyor, and heat up to 220°C for 30 minutes to obtain acid clinker. Control the residual sulfuric acid content of acid clinker to 3%, and then adjust Add 2.4 tons of slag washing water and 0.8 tons of thermal analysis mother liquor while stirring in the slurry tank, and add 2500 kg of acid clinker to make slurry to obtain slurry. The slurry is neutralized with calcium carbonate powder to pH = 5, and then purified with purification solution Filter the residue to adjust the pH of the slurry to 6.5, then filter and wash with a filter to obtain lithium sulfate leaching solution and slag washing water, a...
Embodiment 2
[0026] Take 2 tons of lithium concentrate with a lithium oxide content of 6%. First, it is calcined at 1150°C in a rotary kiln and transformed into a baked material. When the baked material is cooled to 120°C by a cooler, it is ball-milled to a particle size of 95% by a ball mill. less than 80 mesh, then mix the baked material with 600 kg of concentrated sulfuric acid through a screw conveyor, and heat up to 280°C for 20 minutes to obtain acid clinker. Control the residual sulfuric acid content of acid clinker to 6%, and then adjust Add 1.6 tons of slag washing water and 1.6 tons of thermal analysis mother liquor while stirring in the slurry tank and add 2500 kg of acid clinker to make slurry to obtain slurry. The slurry is neutralized with calcium carbonate powder to pH = 6, and then purified with purification solution Filter the residue to adjust the pH of the slurry to 8, then filter and wash with a filter to obtain lithium sulfate leachate and slag washing water, add ma...
Embodiment 3
[0028] Take 2 tons of lithium concentrate with a lithium oxide content of 6%. First, it is calcined in a rotary kiln at 1100°C and transformed into a baked material. When the baked material is cooled to 100°C by a cooler, it is ball-milled to a particle size of 95% by a ball mill. less than 80 mesh, then mix the baked material with 550 kg of concentrated sulfuric acid through a screw conveyor, and heat up to 250°C for 25 minutes to obtain acid clinker. Control the residual sulfuric acid content of acid clinker to 4%, and then adjust Add 2 tons of slag washing water and 1.2 tons of thermal analysis mother liquor in the slurry tank while adding 2500% acid clinker for slurry adjustment to obtain slurry adjustment. The slurry adjustment solution is neutralized with calcium carbonate powder to pH = 5.5, and then filtered with purification liquid Adjust the pH of the slurry to 7, then filter and wash with a filter to obtain lithium sulfate leaching solution and slag washing water...
PUM
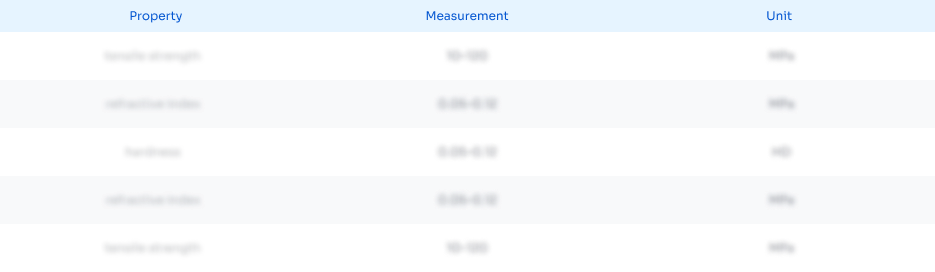
Abstract
Description
Claims
Application Information

- R&D
- Intellectual Property
- Life Sciences
- Materials
- Tech Scout
- Unparalleled Data Quality
- Higher Quality Content
- 60% Fewer Hallucinations
Browse by: Latest US Patents, China's latest patents, Technical Efficacy Thesaurus, Application Domain, Technology Topic, Popular Technical Reports.
© 2025 PatSnap. All rights reserved.Legal|Privacy policy|Modern Slavery Act Transparency Statement|Sitemap|About US| Contact US: help@patsnap.com