Method for continuous gas phase synthesis of oxamide
A gas-phase synthesis and oxamide technology, which is applied in the preparation of carboxylic acid amide, chemical instruments and methods, and the preparation of organic compounds, can solve the problems of unreachable industrial production, long reaction time, and high toxicity of hydrocyanic acid, etc., and eliminate Harm to the environment and human health, continuous and stable industrial production, and the effect of high conversion rate of ammonia decomposition
- Summary
- Abstract
- Description
- Claims
- Application Information
AI Technical Summary
Problems solved by technology
Method used
Image
Examples
Embodiment 1
[0027] A method for continuous gas-phase synthesis of oxamide, the steps are as follows: (1) Dimethyl oxalate is heated to 170°C by a steam heater and a heat-conducting oil heater to be vaporized, and then enters the gas-phase reactor from the upper part of the gas-phase reactor through a tangential direction, The liquid ammonia is vaporized by the evaporator and the buffer tank and enters the gas distributor, and then enters the gas phase reactor from the bottom of the gas phase reactor. The two undergo ammonolysis reaction in the gas phase reactor. The molar ratio of ammonia gas to dimethyl oxalate 2.1︰1, the reaction temperature is 165°C, the reaction pressure is 1MPa, and the reaction residence time is 5min; (2) The powdery oxamide generated by the ammonolysis reaction, part of the excess ammonia in the reaction and the by-product methanol vapor are passed through the cyclone The separator and circulating gas filter realize the separation of the gas-solid phase, and the pow...
Embodiment 2
[0029] A method for continuous gas-phase synthesis of oxamide, the steps are as follows: (1) Dimethyl oxalate is heated to 170°C by a steam heater and a heat-conducting oil heater to be vaporized, and then enters the gas-phase reactor from the upper part of the gas-phase reactor through a tangential direction, The liquid ammonia is vaporized by the evaporator and the buffer tank and enters the gas distributor, and then enters the gas phase reactor from the bottom of the gas phase reactor. The two undergo ammonolysis reaction in the gas phase reactor. The molar ratio of ammonia gas to dimethyl oxalate 2.3︰1, the reaction temperature is 175°C, the reaction pressure is 1.3MPa, and the reaction residence time is 15min; The cyclone separator and circulating gas filter realize the separation of the gas-solid phase, and the powdery oxamide is collected from the bottom of the cyclone separator, and the purity of the oxamide product analyzed by liquid chromatography is 99.2%; (3) the se...
Embodiment 3
[0031]A method for continuous gas-phase synthesis of oxamide, the steps are as follows: (1) Diethyl oxalate is heated to 185°C by a steam heater and a heat-conducting oil heater to be vaporized, and then enters the gas-phase reactor from the upper part of the gas-phase reactor through a tangential direction, The liquid ammonia is vaporized by the evaporator and the buffer tank and enters the gas distributor, and then enters the gas phase reactor from the bottom of the gas phase reactor. The two undergo ammonolysis reaction in the gas phase reactor. The molar ratio of ammonia gas to diethyl oxalate 2.5︰1, the reaction temperature is 185°C, the reaction pressure is 1.5MPa, and the reaction residence time is 30min; The cyclone separator and circulating gas filter realize the separation of the gas-solid phase, and the powdery oxamide is collected from the bottom of the cyclone separator, and the purity of the oxamide product analyzed by liquid chromatography is 99.0%; (3) the separ...
PUM
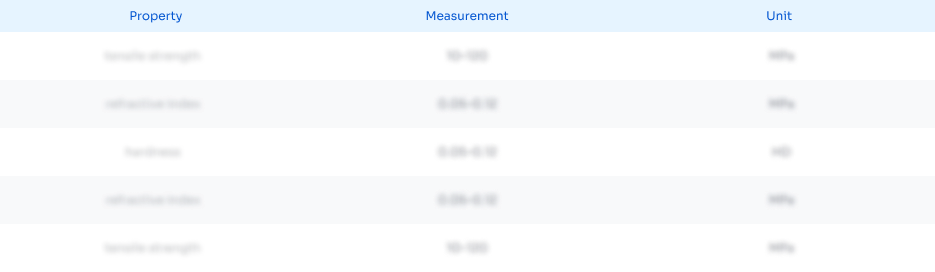
Abstract
Description
Claims
Application Information

- R&D Engineer
- R&D Manager
- IP Professional
- Industry Leading Data Capabilities
- Powerful AI technology
- Patent DNA Extraction
Browse by: Latest US Patents, China's latest patents, Technical Efficacy Thesaurus, Application Domain, Technology Topic, Popular Technical Reports.
© 2024 PatSnap. All rights reserved.Legal|Privacy policy|Modern Slavery Act Transparency Statement|Sitemap|About US| Contact US: help@patsnap.com