Magnetic plastic composite material and preparation method thereof
A technology of composite materials and magnetic plastics, applied in the direction of magnetism of inorganic materials, can solve problems such as poor corrosion resistance, insufficient magnetism, and high processing costs, and achieve the effects of easy dispersion, uniform distribution, and increased strength
- Summary
- Abstract
- Description
- Claims
- Application Information
AI Technical Summary
Problems solved by technology
Method used
Image
Examples
Embodiment 1
[0030] A magnetic plastic composite material, which is made of the following components according to the mass ratio: nylon 6 powder 5%; neodymium iron boron magnetic powder 92%; caprolactam 1%; 3-aminopropyl triethoxysilane 1%; ethylene Bisstearamide 1%.
[0031] The preparation method of the magnetic plastic composite material includes the following steps:
[0032] Step 1: Weigh the NdFeB magnetic powder according to the mass ratio, add it to a high-speed mixer and stir for 60 minutes at a speed of 1000 revolutions per minute to dry the NdFeB magnetic powder and the temperature reaches 100 degrees Celsius.
[0033] Step 2: Weigh 3-aminopropyltriethoxysilane according to the mass ratio, and spray the 3-aminopropyltriethoxysilane uniformly on the stirring neodymium iron boron magnetic powder, and stir for 30 minutes at a speed of 1400 rpm; then add the weighed ethylene bis-stearamide and continue stirring for 5 minutes, and the speed is 1400 rpm.
[0034] Step 3: Heat up the caprolact...
Embodiment 2
[0039] A magnetic plastic composite material, which is made of the following components in a mass ratio: 8% nylon 6 powder; 90% neodymium iron boron magnetic powder; 1% caprolactam; 0.5% 3-aminopropyltrimethoxysilane; ethylene double Stearamide 0.5%.
[0040] The preparation method of the magnetic plastic composite material includes the following steps:
[0041] Step 1: Weigh the NdFeB magnetic powder according to the mass ratio, add it to a high-speed mixer and stir for 60 minutes at a speed of 1000 revolutions per minute to dry the NdFeB magnetic powder and the temperature reaches 100 degrees Celsius.
[0042] Step 2: Weigh 3-aminopropyltrimethoxysilane according to the mass ratio, and spray the 3-aminopropyltrimethoxysilane uniformly on the stirring neodymium iron boron magnetic powder, and stir for 30 minutes at a speed of 1400 rpm / Min, then add the weighed ethylene bisstearyl amide and continue to stir for 5 minutes, and the rotation speed is 1400 rpm;
[0043] Step 3: Heat up ...
Embodiment 3
[0048] A magnetic plastic composite material, which is made of the following components according to the mass ratio: 4% nylon 6 powder; 94% neodymium iron boron magnetic powder; 0.5% caprolactam; 0.5% 3-aminopropyltriethoxysilane; polytetrafluoroethylene Vinyl fluoride powder 1%.
[0049] The preparation method of the magnetic plastic composite material includes the following steps:
[0050] Step 1: Weigh the NdFeB magnetic powder according to the mass ratio, add it to a high-speed mixer and stir for 60 minutes at a speed of 1000 revolutions per minute to dry the NdFeB magnetic powder and the temperature reaches 100 degrees Celsius.
[0051] Step 2: Weigh 3-aminopropyltriethoxysilane according to the mass ratio, and spray the 3-aminopropyltriethoxysilane uniformly on the stirring neodymium iron boron magnetic powder, and stir for 30 minutes at a speed of 1400 rpm, then add the weighed polytetrafluoroethylene powder and continue stirring for 10 minutes, and the rotation speed is 1400...
PUM
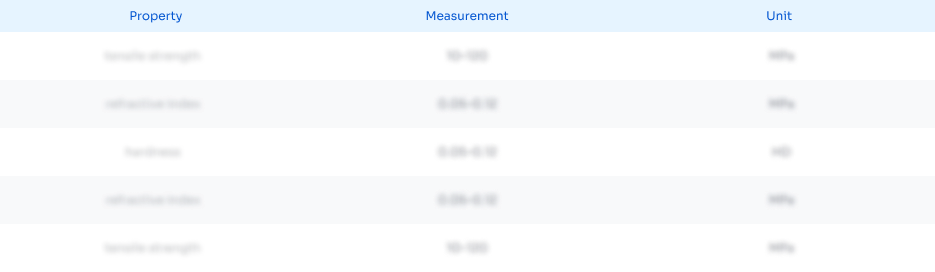
Abstract
Description
Claims
Application Information

- R&D Engineer
- R&D Manager
- IP Professional
- Industry Leading Data Capabilities
- Powerful AI technology
- Patent DNA Extraction
Browse by: Latest US Patents, China's latest patents, Technical Efficacy Thesaurus, Application Domain, Technology Topic, Popular Technical Reports.
© 2024 PatSnap. All rights reserved.Legal|Privacy policy|Modern Slavery Act Transparency Statement|Sitemap|About US| Contact US: help@patsnap.com