Preparation method of food grade polyacrylamide
A technology of polyacrylamide and acrylamide, which is applied in the field of functional polymers, can solve problems such as incomplete polymerization, high residual monomer content, and failure to meet the use requirements, so as to reduce energy consumption, green production process, and reduce raw material costs Effect
- Summary
- Abstract
- Description
- Claims
- Application Information
AI Technical Summary
Problems solved by technology
Method used
Examples
Embodiment 1
[0018] In a 500ml jar, under stirring with a glass rod, slowly add 29g of acrylic acid to 213g of 30% acrylamide aqueous solution, and slowly neutralize to PH=7 with sodium hydroxide under stirring. Add 0.8 g of cosolvent thiourea, and 0.007 g of complexing agent tetrasodium ethylenediamine tetraacetic acid; add 0.015 g of high-efficiency chain transfer agent isopropanol, and 0.2 g of azo compound azobisisobutylamidine hydrochloride. After stirring well and mixing evenly, cool down to 3°C, and start to pass in a flow rate of 60m 3 / h of high-purity nitrogen (nitrogen purity ≥ 99.99%) to remove oxygen in the system. During nitrogen flow, 0.004 g of oxidation initiator potassium persulfate and 0.0015 g of reduction initiator sodium sulfite were sequentially added. When the oxygen content of the system is less than 0.001%, seal and seal. When the reaction no longer heats up, put it into a water bath at 75° C. and heat it for 3 hours. After the heat preservation is over, take o...
Embodiment 2
[0021] In a 500ml jar, under stirring with a glass rod, slowly add 21g of acrylic acid to 213g of 30% acrylamide aqueous solution, and slowly neutralize to PH=6 with sodium bicarbonate while stirring. Add co-solvent polyethylene glycol 2001.8g, and complexing agent ethylenediaminetetraacetic acid disodium salt 0.012g; g. After stirring well and mixing evenly, cool down to 4°C, and start to pass in a flow rate of 60m 3 / h of high-purity nitrogen (nitrogen purity ≥ 99.99%) to remove oxygen in the system. During nitrogen flow, 0.006 g of an oxidation initiator dialkyl peroxide and 0.0008 g of a reduction initiator triethanolamine were sequentially added. When the oxygen content of the system is less than 0.001%, seal and seal. When the temperature of the reaction no longer rises, put it into a water bath at 80° C. and heat it for 1 hour. After the heat preservation is over, take out the colloid, add 0.32g of polyoxyethylene sorbitan monolaurate as an anti-toxic agent, dry in ...
Embodiment 3
[0024] In a 500ml jar, under stirring with a glass rod, slowly add 13g of acrylic acid to 213g of 30% acrylamide aqueous solution, and slowly neutralize to PH=8 with sodium carbonate under stirring. Add 1.8 g of cosolvent urea, and 0.012 g of complexing agent nitrilotriacetic acid sodium salt; add 0.019 g of high-efficiency chain transfer agent dodecanethiol, and 0.07 g of azo compound dimethyl azobisisobutyrate. After stirring well and mixing evenly, cool down to 5°C, and start to pass in a flow rate of 60m 3 / h of high-purity nitrogen (nitrogen purity ≥ 99.99%) to remove oxygen in the system. During nitrogen flow, 0.006 g of oxidation initiator ammonium persulfate and 0.0008 g of reduction initiator sodium bisulfite were sequentially added. When the oxygen content of the system is less than 0.001%, seal and seal. When the temperature of the reaction no longer rises, put it into a water bath at 85° C. and heat it for 2 hours. After the heat preservation is over, take out t...
PUM
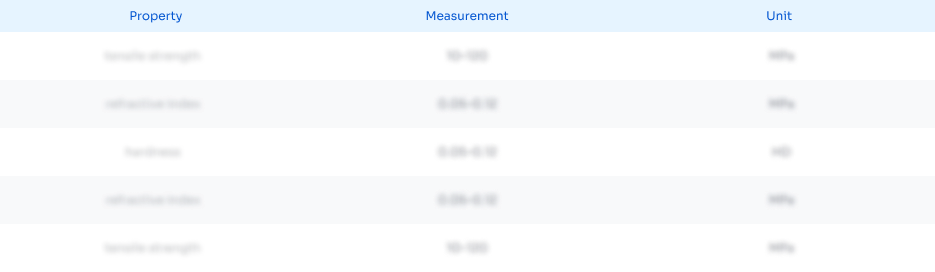
Abstract
Description
Claims
Application Information

- R&D
- Intellectual Property
- Life Sciences
- Materials
- Tech Scout
- Unparalleled Data Quality
- Higher Quality Content
- 60% Fewer Hallucinations
Browse by: Latest US Patents, China's latest patents, Technical Efficacy Thesaurus, Application Domain, Technology Topic, Popular Technical Reports.
© 2025 PatSnap. All rights reserved.Legal|Privacy policy|Modern Slavery Act Transparency Statement|Sitemap|About US| Contact US: help@patsnap.com