Composite modified asphalt and preparation method thereof
A composite modified asphalt, modified technology, applied in building components, building insulation materials, construction, etc., can solve the problems of poor compatibility between epoxy resin and asphalt materials, poor low-temperature bending performance, poor flexibility, etc., and achieve excellent low-temperature Flexibility, good high temperature and low temperature performance, and strong fatigue resistance
- Summary
- Abstract
- Description
- Claims
- Application Information
AI Technical Summary
Problems solved by technology
Method used
Image
Examples
Embodiment 1
[0027] Add 40kg polyether diol (molecular weight 1000) into the reaction kettle, the temperature in the kettle is 100-130℃, vacuumize and dehydrate for 2-3 hours, then add 0.2kg triethylenediamine catalyst and 240kg bisphenol A epoxy resin (E51 ), the temperature is 100-150°C, after 1-2 hours of reaction, the temperature is lowered to 70-90°C, and then 110kg of toluene diisocyanate is added to react for 2-3 hours to obtain a polyurethane-modified epoxy resin; the polyurethane-modified epoxy resin and 70kg of naphthalene oil, 60kg of dioctyl phthalate (DOP), and 450kg of road petroleum asphalt (70#) were mixed and stirred evenly at a temperature of 120°C as component A; 70kg of modified aromatic amine curing agent (0421 ) was added to component A, and stirred evenly to obtain polyurethane epoxy resin composite modified asphalt 1#.
Embodiment 2
[0029] Add 40kg of polyethylene glycol (molecular weight 400) into the reaction kettle, the temperature in the kettle is 100-130°C, vacuumize and dehydrate for 2-3 hours, then add 0.2kg of triethanolamine catalyst and 240kg of bisphenol F epoxy resin (B30-5) , the temperature is 100-150 ° C, after 1-2 hours of reaction, the temperature is lowered to 70-90 ° C, and then 110 kg of polymethylene polyphenyl polyisocyanate is added to react for 2-3 hours to obtain a polyurethane modified epoxy resin; 70kg naphthalene oil, 60kg dibutyl phthalate (DBP), 450kg road petroleum asphalt (90#) mixed with 70kg naphthalene oil, 450kg road petroleum asphalt (90#) at a temperature of 120 ℃ and then used as component A; 70kg modified aromatic amine The B component of the curing agent (0422) was added to the A component, and stirred evenly to obtain the polyurethane epoxy resin composite modified asphalt 2#.
Embodiment 3
[0031]Add 40kg of polyethylene glycol (molecular weight 400) into the reaction kettle, the temperature in the kettle is 100-130°C, vacuumize and dehydrate for 2-3 hours, then add 0.2kg of triethanolamine catalyst and 120kg of bisphenol F epoxy resin (B30-5) 120kg bisphenol A type epoxy resin (E51), temperature 100~150℃, after 1~2h of reaction, lower the temperature to 70~90℃, then add 110kg toluene diisocyanate and react for 2~3h to obtain polyurethane modified ring Oxygen resin; mix polyurethane modified epoxy resin with 70kg naphthalene oil, 30g dibutyl phthalate (DBP), 30g dioctyl phthalate (DOP), 450kg road petroleum asphalt (110#) at 120°C After mixing and stirring at a temperature of 100°F, it was used as component A; 70kg of component B of the modified aromatic amine curing agent (605B) was added to component A, and stirred evenly to obtain polyurethane epoxy resin composite modified asphalt 3#.
PUM
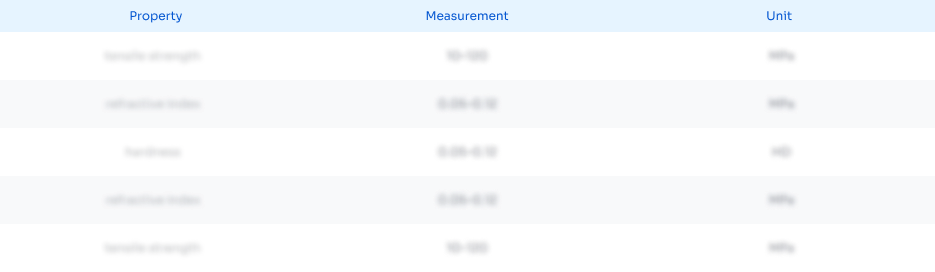
Abstract
Description
Claims
Application Information

- R&D
- Intellectual Property
- Life Sciences
- Materials
- Tech Scout
- Unparalleled Data Quality
- Higher Quality Content
- 60% Fewer Hallucinations
Browse by: Latest US Patents, China's latest patents, Technical Efficacy Thesaurus, Application Domain, Technology Topic, Popular Technical Reports.
© 2025 PatSnap. All rights reserved.Legal|Privacy policy|Modern Slavery Act Transparency Statement|Sitemap|About US| Contact US: help@patsnap.com