Low-cost insulating rubber cable material and preparation technology thereof
A kind of insulating rubber and preparation technology, which is applied in the direction of insulated cables, insulators, insulated conductors, etc., can solve the problems of low elongation at break, elongation at break easily, narrow process range, etc., achieve high physical and mechanical properties, improve relative Capacitance, the effect of overcoming the difficulty of placing glue
- Summary
- Abstract
- Description
- Claims
- Application Information
AI Technical Summary
Problems solved by technology
Method used
Image
Examples
Embodiment 1
[0050] Example 1. A low-cost insulating rubber cable material. The formula of each component of the material is: chlorinated polyethylene (CPE) 12 kg, ethylene-octene copolymer elastomer (POE) 19 kg, 800# paraffin-based rubber oil 5 kg, 0.8 kg of activated magnesium oxide, 1.5 kg of zinc oxide, 5 kg of superfine talc powder, 0.5 kg of environmental stabilizer, 1.5 kg of microcrystalline wax, 0.8 kg of titanium dioxide, 25 kg of modified calcined clay, 4,4′ double (α,α dimethylbenzyl) diphenylamine 0.6 kg, dicumyl peroxide 1.5 kg, triallyl cyanurate 1.2 kg.
[0051] The mass fraction of the octene monomer in the above-mentioned ethylene-octene copolymer elastomer exceeds 20%.
[0052] Preparation method: first mix chlorinated polyethylene (CPE) and ethylene-octene copolymer elastomer (POE) in an internal mixer at 90~110°C for 4-5 minutes according to weight percentage, and mix the two materials evenly; 800# Paraffin-based rubber oil, active magnesium oxide, active zinc oxide, ...
Embodiment 2
[0056] Example 2. A low-cost insulating rubber cable material. The formula of each component of the material is: chlorinated polyethylene (CPE) 12 kg, ethylene-octene copolymer elastomer (POE) 19 kg, 800# paraffin-based rubber oil 7 kg, 0.8 kg of activated magnesium oxide, 1.5 kg of zinc oxide, 7 kg of superfine talc powder, 0.5 kg of environmental stabilizer, 1.5 kg of microcrystalline wax, 0.8 kg of titanium dioxide, 30 kg of modified calcined clay, 4,4' double (α,α dimethylbenzyl) diphenylamine 0.6 kg, dicumyl peroxide 1.5 kg, triallyl cyanurate 1.2 kg.
[0057] The mass fraction of the octene monomer in the above-mentioned ethylene-octene copolymer elastomer exceeds 20%.
[0058] The preparation method is the same as in Example 1.
[0059] The performance testing data of the low-cost insulating rubber cable material prepared in this example are as follows:
[0060]
[0061] Aging condition: 135±1℃×168 hours.
Embodiment 3
[0062] Example 3. A low-cost insulating rubber cable material. The formula of each component of the material is: chlorinated polyethylene (CPE) 14 kg, ethylene-octene copolymer elastomer (POE) 19 kg, 800# paraffin-based rubber oil 5 kg, 0.8 kg of activated magnesium oxide, 1.0 kg of zinc oxide, 5 kg of superfine talc powder, 0.5 kg of environmental stabilizer, 2 kg of microcrystalline wax, 0.8 kg of titanium dioxide, 25 kg of modified calcined clay, 4,4′ of anti-aging agent 0.5 kg of bis(α,α dimethylbenzyl) diphenylamine, 1.5 kg of vulcanizing agent dicumyl peroxide, and 1.2 kg of vulcanizing aid triallyl cyanurate.
[0063] The mass fraction of the octene monomer in the above-mentioned ethylene-octene copolymer elastomer exceeds 20%.
[0064] The performance test data of the low-cost insulating rubber cable material prepared in this example are as follows:
[0065]
[0066] Aging condition: 135±1℃×168 hours.
[0067] To sum up, the low-cost insulating rubber cable materi...
PUM
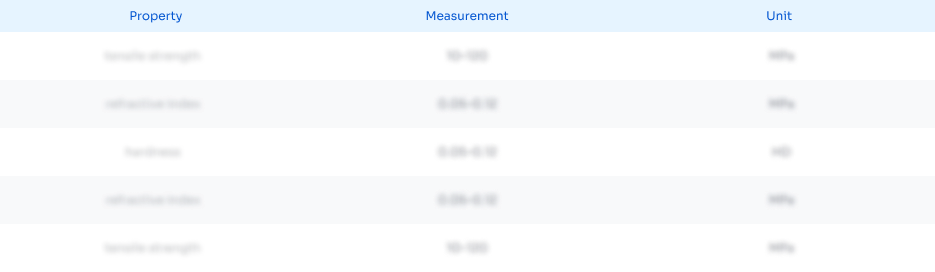
Abstract
Description
Claims
Application Information

- R&D
- Intellectual Property
- Life Sciences
- Materials
- Tech Scout
- Unparalleled Data Quality
- Higher Quality Content
- 60% Fewer Hallucinations
Browse by: Latest US Patents, China's latest patents, Technical Efficacy Thesaurus, Application Domain, Technology Topic, Popular Technical Reports.
© 2025 PatSnap. All rights reserved.Legal|Privacy policy|Modern Slavery Act Transparency Statement|Sitemap|About US| Contact US: help@patsnap.com