Aluminum-alloy electrophoretic wood-grain profile and process for preparing same
A preparation process, aluminum alloy technology, applied in electrophoretic plating, electrolytic coating, anodizing and other directions, can solve the problems of incomplete transfer, affect the appearance quality, poor gloss, etc., achieve completely clear transfer, and avoid appearance defects , the effect of strong adhesion
- Summary
- Abstract
- Description
- Claims
- Application Information
AI Technical Summary
Problems solved by technology
Method used
Examples
Embodiment 1
[0014] An aluminum alloy electrophoretic wood grain profile and a preparation process thereof, comprising the following steps:
[0015] S1: Manufacture of refining modifier: melting, refining, degassing, slag removal, mixing the mixed rare earth ingot, AlTiB alloy and pure aluminum ingot in a resistance crucible furnace, and casting to produce a refining modifier;
[0016] S2: Melting aluminum alloy: Add Mg, Si, Fe alloy elements, refining modifier and aluminum to the casting energy-saving furnace to ensure that the alloy mass percentage is 0.5%Mg, 0.4%Si, 0.04%Re, 0.01%Ti, 0.002%B , 0.13% Fe, heated for smelting, wherein the smelting temperature is 900°C;
[0017] S3: Making profiles: cast the melt into ingots, homogenize at 560°C for 6 hours, and then extrude into aluminum alloy profiles at 430°C;
[0018] S4: Anodizing: place the aluminum alloy profile in a sulfuric acid solution with a temperature of 25°C and a concentration of 150g / L for 40 minutes, and the anodizing pow...
Embodiment 2
[0021] An aluminum alloy electrophoretic wood grain profile and a preparation process thereof, comprising the following steps:
[0022] S1: Manufacture of refining modifier: melting, refining, degassing, slag removal, mixing the mixed rare earth ingot, AlTiB alloy and pure aluminum ingot in a resistance crucible furnace, and casting to produce a refining modifier;
[0023] S2: Melting aluminum alloy: Add Mg, Si, Fe alloy elements, refining modifier and aluminum to the casting energy-saving furnace to ensure that the alloy mass percentage is 0.54%Mg, 0.44%Si, 0.08%Re, 0.02%Ti, 0.004%B , 0.2% Fe, heated for smelting, wherein the smelting temperature is 1000°C;
[0024] S3: Making profiles: cast the melt into ingots, homogenize at 560°C for 6 hours, and then extrude into aluminum alloy profiles at 450°C;
[0025] S4: Anodizing: place the aluminum alloy profile in a sulfuric acid solution with a temperature of 25°C and a concentration of 150g / L for 40 minutes, and the anodizing p...
Embodiment 3
[0028] An aluminum alloy electrophoretic wood grain profile and a preparation process thereof, comprising the following steps:
[0029] S1: Manufacture of refining modifier: melting, refining, degassing, slag removal, mixing the mixed rare earth ingot, AlTiB alloy and pure aluminum ingot in a resistance crucible furnace, and casting to produce a refining modifier;
[0030] S2: Melting aluminum alloy: Add Mg, Si, Fe alloy elements, refining modifier and aluminum to the casting energy-saving furnace to ensure that the alloy mass percentage is 0.52%Mg, 0.42%Si, 0.06%Re, 0.015%Ti, 0.003%B , 0.16% Fe, heated for smelting, wherein the smelting temperature is 950°C;
[0031] S3: Making profiles: cast the melt into ingots, homogenize at 560°C for 6 hours, and then extrude into aluminum alloy profiles at 440°C;
[0032] S4: Anodizing: place the aluminum alloy profile in a sulfuric acid solution with a temperature of 25°C and a concentration of 150g / L for 40 minutes, and the anodizing ...
PUM
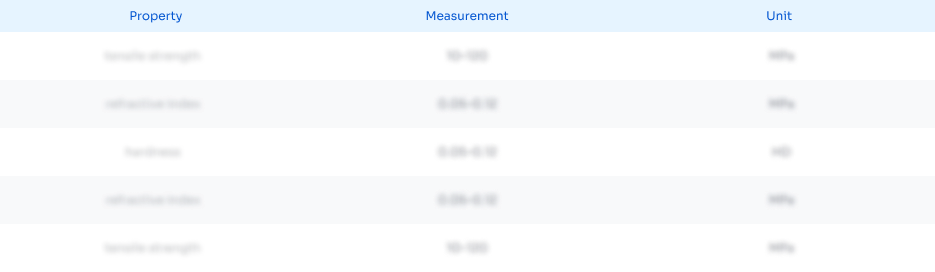
Abstract
Description
Claims
Application Information

- R&D
- Intellectual Property
- Life Sciences
- Materials
- Tech Scout
- Unparalleled Data Quality
- Higher Quality Content
- 60% Fewer Hallucinations
Browse by: Latest US Patents, China's latest patents, Technical Efficacy Thesaurus, Application Domain, Technology Topic, Popular Technical Reports.
© 2025 PatSnap. All rights reserved.Legal|Privacy policy|Modern Slavery Act Transparency Statement|Sitemap|About US| Contact US: help@patsnap.com