Nano-ceramic composite spraying powder and preparation method for same
A technology of nano-ceramics and spraying powder, which is applied in the direction of coating, fusion spraying, lighting and heating equipment, etc. It can solve the problems of lack of strengthening coating, poor uniformity of mixed substances, and poor thermal conductivity, etc., to prevent high temperature Oxidation, the effect of preventing the growth of nanocrystal grains
- Summary
- Abstract
- Description
- Claims
- Application Information
AI Technical Summary
Problems solved by technology
Method used
Examples
Embodiment Construction
[0017] The composition and weight percent of the nano-ceramic composite spray powder of the present invention are:
[0018] Metal alloy MCrAlTaY 65%~90%;
[0019] Nano-alumina and / or nano-yttrium oxide 5% to 30%;
[0020] Nano titanium diboride 5%~15%;
[0021] In the metal alloy MCrAlTaY, M is metal nickel Ni, metal cobalt Co or metal nickel-cobalt alloy, wherein the weight percentage is: M 50%-80%, Cr 12%-28%, Al 5%-12%, Ta 0.2% to 8%, Y 0.1% to 1.2%, metal alloy MCrAlTaY and nano-alumina and / or nano-yttrium oxide constitute alloy oxide ceramic composite powder, and nano-titanium diboride is nano-cermet powder.
[0022] Furthermore, the particle size of the alloy oxide ceramic composite powder particles is -40 μm to +10 μm.
[0023] Further, the particle size of the above-mentioned nano-cermet powder is less than 100 nm. Preferably 10-60nm.
[0024] In the nano-ceramic composite spraying powder, the high-temperature-resistant metal alloy MCrAlTaY not only has good high-...
PUM
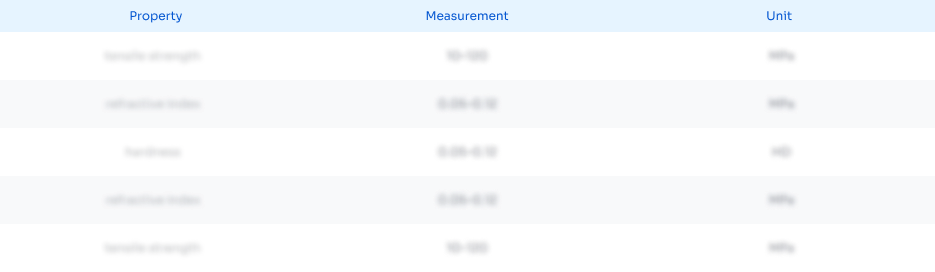
Abstract
Description
Claims
Application Information

- R&D Engineer
- R&D Manager
- IP Professional
- Industry Leading Data Capabilities
- Powerful AI technology
- Patent DNA Extraction
Browse by: Latest US Patents, China's latest patents, Technical Efficacy Thesaurus, Application Domain, Technology Topic, Popular Technical Reports.
© 2024 PatSnap. All rights reserved.Legal|Privacy policy|Modern Slavery Act Transparency Statement|Sitemap|About US| Contact US: help@patsnap.com