Steel-based hydrogen permeation-resistant composite coating and preparation method for same
A composite coating and hydrogen-repelling technology, which is applied in coatings, metal material coating processes, superimposed layer plating, etc., can solve the problems of poor hydrogen resistance and penetration performance, and achieve improved bonding strength, high reduction factor, and thermal Good cycle performance
- Summary
- Abstract
- Description
- Claims
- Application Information
AI Technical Summary
Problems solved by technology
Method used
Image
Examples
Embodiment 1
[0025] Eurofer low-activity martensitic stainless steel sheets were polished and ultrasonically cleaned and then placed in a quartz tubular atmosphere furnace in a water-carrying argon atmosphere at 10 -20 Pa oxygen partial pressure, oxidation at 700°C for 5h to obtain an oxide coating containing chromium oxide. It is then placed in a quartz tube atmosphere furnace to deposit an alumina coating on top of the thermally grown oxide coating using metal-organic chemical vapor deposition. figure 2 SEM photographs of the cross-section and surface of the hydrogen permeation barrier composite coating. in, figure 2 (a) is the cross-sectional electron micrograph of the hydrogen permeable composite coating, such as figure 2 As shown in (a), in the cross-sectional morphology of the hydrogen permeable composite coating, from bottom to top, there are stainless steel substrate, thermally grown oxide coating and alumina coating. figure 2 (b) is the scanning electron micrograph of the s...
Embodiment 2
[0027] F82H low-activity martensitic stainless steel was polished and ultrasonically cleaned and then placed in a quartz tube atmosphere furnace. -20 Pa oxygen partial pressure, oxidized at 900°C for 5h to obtain an oxide coating containing chromium oxide. An alumina coating was then prepared on the thermally grown oxide coating using a sol-gel method. image 3 It is the EDS energy spectrum element depth distribution of the composite coating, and the results show that the composite coating from the outside to the inside is alumina and thermal growth oxide coating respectively. image 3 (b) is the hydrogen permeation resistance curve of the composite coating on F82H stainless steel, and its hydrogen permeation reduction factor is 910 at 400 °C.
PUM
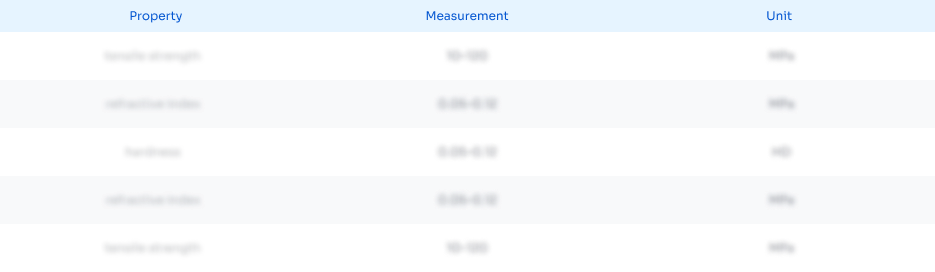
Abstract
Description
Claims
Application Information

- R&D Engineer
- R&D Manager
- IP Professional
- Industry Leading Data Capabilities
- Powerful AI technology
- Patent DNA Extraction
Browse by: Latest US Patents, China's latest patents, Technical Efficacy Thesaurus, Application Domain, Technology Topic, Popular Technical Reports.
© 2024 PatSnap. All rights reserved.Legal|Privacy policy|Modern Slavery Act Transparency Statement|Sitemap|About US| Contact US: help@patsnap.com