Refractory fettling material
A furnace charging and refractory technology, applied in the field of charging charging, can solve problems such as unfavorable large-area flow charging, damage to the health of employees, long sintering time, etc., to improve the sintering strength and adhesion, reduce the consumption of refractory materials, and reduce the sintering time. short effect
- Summary
- Abstract
- Description
- Claims
- Application Information
AI Technical Summary
Problems solved by technology
Method used
Image
Examples
Embodiment 1
[0031] Take magnesia: aggregate 60Kg, fine powder: 2Kg; liquid pitch: 5Kg; sodium hexametaphosphate: 1Kg; caprolactam 1Kg; potassium nitrate 5Kg, iron oxide 10Kg, and calcium phosphate 10Kg. Put the magnesia aggregate into the mixer, heat it to 80oC, stir for 10 minutes, add liquid asphalt, stir evenly, then add other raw materials, stir for 5 minutes, and then discharge the material evenly, the thickness does not exceed 20cm, and then crush it after cooling No more than 15cm. Inspection and packaging to get the finished product.
Embodiment 2
[0033] Take magnesia: aggregate 80Kg, fine powder: 10Kg; liquid pitch: 10Kg; sodium hexametaphosphate: 5Kg; caprolactam 4Kg; potassium nitrate 10Kg, iron oxide 20Kg, and calcium phosphate 30Kg. Put the magnesia aggregate into the mixer, heat it to 80oC, stir for 10 minutes, add liquid asphalt, stir evenly, then add other raw materials, stir for 5 minutes, and then discharge the material evenly, the thickness does not exceed 20cm, and then crush it after cooling No more than 15cm. Inspection and packaging to get the finished product.
Embodiment 3
[0035] Take magnesia: aggregate 75Kg, fine powder: 10Kg; liquid pitch: 7Kg; sodium hexametaphosphate: 3Kg; caprolactam 2Kg; smoke suppressant: potassium nitrate 10Kg, iron oxide 20Kg, and calcium phosphate 25Kg. Put the magnesia aggregate into the mixer, heat it to 80oC, stir for 10 minutes, add liquid asphalt, stir evenly, then add other raw materials, stir for 5 minutes, and then discharge the material evenly, the thickness does not exceed 20cm, and then crush it after cooling No more than 15cm. Inspection and packaging to get the finished product.
PUM
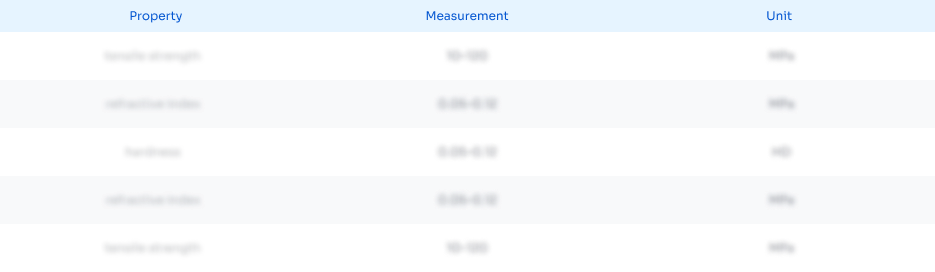
Abstract
Description
Claims
Application Information

- R&D Engineer
- R&D Manager
- IP Professional
- Industry Leading Data Capabilities
- Powerful AI technology
- Patent DNA Extraction
Browse by: Latest US Patents, China's latest patents, Technical Efficacy Thesaurus, Application Domain, Technology Topic, Popular Technical Reports.
© 2024 PatSnap. All rights reserved.Legal|Privacy policy|Modern Slavery Act Transparency Statement|Sitemap|About US| Contact US: help@patsnap.com