Preparation method of novel solvent-free antistatic antibiosis epoxy self-leveling terrace paint
A solvent-free, anti-static technology, applied in epoxy resin coatings, conductive coatings, coatings, etc., can solve problems such as increased construction problems, increased coating viscosity, and high manufacturing costs, and achieve simple construction, easy operation, and anti-static good performance effect
- Summary
- Abstract
- Description
- Claims
- Application Information
AI Technical Summary
Problems solved by technology
Method used
Examples
Embodiment 1
[0026] Prepare raw materials according to the following parts by mass: 100 parts of bisphenol A liquid epoxy resin; 30 parts of ethylene glycol diglycidyl ether; 20 parts of doped polyaniline; 3 parts of negative ion antibacterial agent; 0.3 part of defoamer, thickener 2 parts of wetting agent, 0.1 part of wetting agent and 0.2 part of dispersing agent; 1 part of self-leveling color paste; 2 parts of modified alicyclic amides; 0.2 part of drier;
[0027] Add bisphenol A type liquid epoxy resin to ethylene glycol diglycidyl ether, mix and stir evenly, and stir at a medium speed for 20 minutes to form component A;
[0028] Mix defoamer, thickener, wetting agent, dispersant, doped polyaniline, negative ion antibacterial agent, and self-leveling color paste, disperse at high speed for 30 minutes, grind to form a slurry, and add modified alicyclic amide and drier, stir evenly to form component B;
[0029] Mix components A and B evenly to form a floor coating.
Embodiment 2
[0031] Prepare raw materials according to the following parts by mass: 100 parts of bisphenol A liquid epoxy resin; 20 parts of 1,2-propylene glycol diglycidyl ether; 10 parts of zinc oxide whiskers; 1 part of anion antibacterial agent; 0.5 part of defoamer, 1 part of thickener, 0.4 part of wetting agent and 0.8 part of dispersant; 2 parts of self-leveling color paste; 3 parts of modified alicyclic amide; 0.3 part of drier;
[0032] Add bisphenol A type liquid epoxy resin to 1,2-propanediol diglycidyl ether, mix and stir evenly, and stir at a medium speed for 20 minutes to form component A;
[0033] Mix defoamer, thickener, wetting agent, dispersant, zinc oxide whisker, negative ion antibacterial agent, and self-leveling color paste, disperse at high speed for 30 minutes, grind to form a slurry, and add modified alicyclic amide and drier, stir evenly to form component B;
[0034] Mix components A and B evenly to form a floor coating.
Embodiment 3
[0036] Prepare raw materials according to the following parts by mass: 100 parts of bisphenol A liquid epoxy resin; 25 parts of 1,4-butanediol diglycidyl ether; 14 parts of doped polyaniline; 2 parts of negative ion antibacterial agent; 0.8 parts of defoamer 1 part, 1 part of thickener, 0.2 part of wetting agent and 0.3 part of dispersant; 3 parts of self-leveling color paste; 4 parts of modified alicyclic amide; 0.4 part of drier;
[0037] Add bisphenol A liquid epoxy resin to 1,4-butanediol diglycidyl ether, mix and stir evenly, and stir at medium speed for 20 minutes to form component A;
[0038] Mix defoamer, thickener, wetting agent, dispersant, doped polyaniline, negative ion antibacterial agent, and self-leveling color paste, disperse at high speed for 30 minutes, grind to form a slurry, and add modified alicyclic amide and drier, stir evenly to form component B;
[0039] Mix components A and B evenly to form a floor coating.
PUM
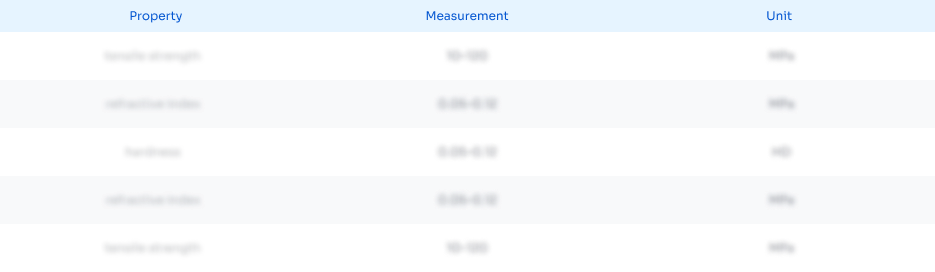
Abstract
Description
Claims
Application Information

- R&D Engineer
- R&D Manager
- IP Professional
- Industry Leading Data Capabilities
- Powerful AI technology
- Patent DNA Extraction
Browse by: Latest US Patents, China's latest patents, Technical Efficacy Thesaurus, Application Domain, Technology Topic, Popular Technical Reports.
© 2024 PatSnap. All rights reserved.Legal|Privacy policy|Modern Slavery Act Transparency Statement|Sitemap|About US| Contact US: help@patsnap.com